Successful Applications of Industrial Tuggers in 6 Industries
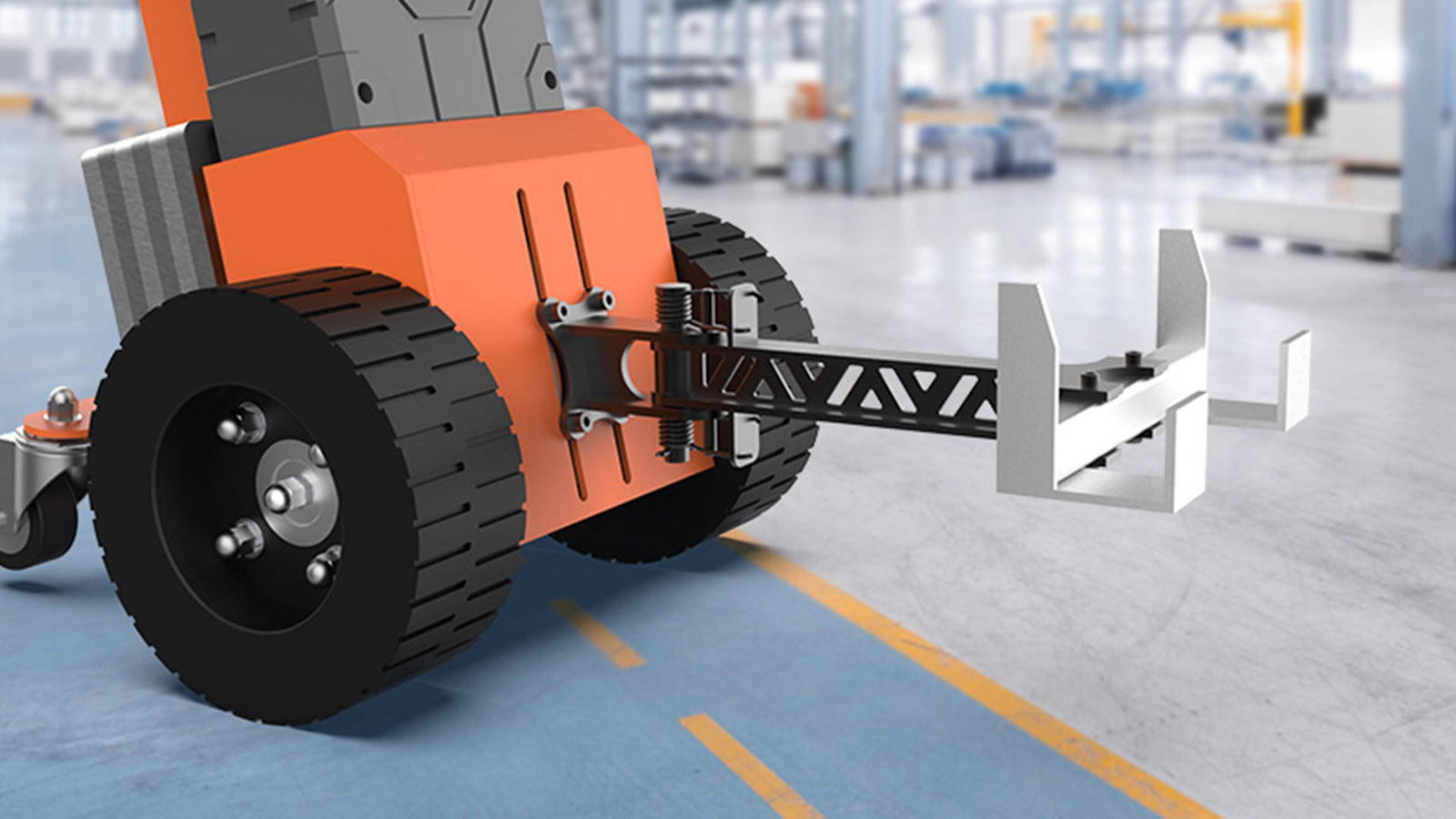
Automotive Manufacturing
Example: Toyota Lean Production Case Study
- Background: One of the original lean manufacturings pioneer, Toyota was confronted with a problem to improve their assembly lines in order to be able to preserve their status in an ever demanding automotive industry.
- Objective: The objective was to increase operational efficiencies and reduce cost, which would safe operating standards.
- Solution: This challenge Toyota handles by optimizing the same in their production through industrial tuggers. These tuggers had to pick up parts and materials from the warehouse and move them directly to the assembly line. This strategic move sharply decreased the dependence on forklifts, which are conventionally used to do such a job.
Implementation Details:
- Shift in Operations: Toyota altered its internal logistics by introducing tuggers. Unlike forklifts, tuggers are built to haul multiple carts simultaneously to keep materials moving throughout the process. This system helped trigger the arrival of parts just in time — a principle from lean manufacturing.
- Improved workflow: The tuggers ran along set paths, which decreased unnecessary movement and lowered the potential for accidents. This focused approach provided added security and a successful work flow.
Quantifiable Outcomes:
- Tuggers integrated: The use of tuggers enabled to reduce the transportation time by an impressive 30%. As a consequence, parts and materials were delivered to the assembly lines quicker and reduced idle time for both workers and machinery.
- Cost Efficiency: Production costs decreased when forklifts were replaced with tuggers. Forklifts, being costly to upkeep and operate were obsolete, freeing up the savings for further investment in other contentious production departments.
- This resulted in substantially increased workflow efficiency as the new logistics flow was considerably more streamlined. Not only this would keep the production pace more consistent, thus reducing bottlenecks and increasing overall productivity with a leaner supply chain for Toyota.
Real-world Example:
- Only 6 months after its introduction, Toyota increased the capacity of one of its major assembly plants by 20% using tuggers. The plant makes more than 300,000 cars a year also benefited much from the lean approach that industrial tuggers have allowed.
- Safety Metrics: The plant saw a 25 percent decrease in material handling-related workplace injuries, highlighting the safety benefits of tuggers relative to forklifts.
Through following the recommendations of lean manufacturing and combining these principles with better material handling equipment, Toyota not only improved their own business metrics but set a new standard for efficiency in the industry.
Aerospace Industry
Boeing Increases Production Rates with Tuggers → Shop Case Study
- Boeing is a world leader in aerospace manufacturing and they needed to move large, delicate aircraft components across their sprawling assembly sites. In order to keep their production lines and quality level, which urgent for them is the safe and on-time transfer of these components.
- Resolution: The only way to mitigate this issue, Boeing started incorporating industrial tuggers within their assembly line functions. The tuggers in these cases are purpose-built to manage the complex and high-volume needs of aerospace production, offering a consistent and cost-effective way to move components between different stations throughout assembly.
Implementation Details:
- Custom designed tugger: Boeing was able to customize tuggers with a unique geometry and flexibility, given the necessity for its intended use with fragile aircraft parts The personalized case feature custom mounts and cushioning for the parts to survive shipping.
- Autonomous Route Optimization: The route the tuggers travel within the factory is optimized by Boeing, so their path has been programmed to take them only where they need to be, and avoid problematic load-heavy corridors that are often filled with other activity on a busy assembly floor. This created a consistent supply of materials and minimal possible delays.
- Automation and Tracking: Various tuggers to be fitted with automatic guided vehicle (AGV) technology, integrated GPS tracking system. This facilitated very accurate control and monitoring of their movements, guaranteeing that components arrived at their destination on time and in good condition.
Quantifiable Outcomes:
- Decreased loss: The use of tuggers has significantly reduced the risk of damage to sensitive aircraft parts. This was done by the application of special padding and secure attachment systems to protect the components during transport.
- Increased Productivity: The use of tuggers made the plant 50% more efficient, at a rate of $800k per year improved production costs Labor.
- Cost Reduction: Tugger system decrease manual handling and traditional forklifts by 15% labor cost. His reduction in manual work comes from the automated systems that are just so much faster.
- 20% faster to market with the new optimized transportation process (overall increase in production speed). They could even build in less downtime and produce a less interrupted assembly process by having new components delivered faster and on time.
Real-world Example:
- The use of simple electric tuggers have been revolutionary in Boeing's Everett factory, home to the 787 Dreamlinerassembly line. This is a 98.3-acre factory where the time taken to move parts across this vast area was significantly reduced. In practice, this meant the time it took to move fuselage sections was reduced by 25%, having a direct knock-on effect on assembly times and output.
- Factory referencing efficiency: The factory cited a 30% increase in logistics efficiency; this was due to tuggers being able to move multiple components at once, decreasing the number of trips needed.
Boeing’s usage of industrial tuggers for its strategic purposes paints a picture of how aerospace manufacturers can use better logistics solution to improve production efficiency and safety. Boeing's successful implementation proves the dramatic gains in production speed and time.
Food and Beverage Industry
Coca-Cola Case Study — Distribution Center Efficiency
- Background: Coca-Cola, a leader in the global beverage industry, was struggling to handle the ongoing movement of pallets weighing up to several tonnes between warehouses. The objective was to reduce workload, enhance safety levels and lower maintenance costs.
- Solution: In order to do this Coca-Cola brought in industrial tuggers to move pallets out of the production area and onto storage into docks. With this strategic move they wanted to further improve efficiency and safety in all their logistcs operations.
Implementation Details:
- The largest and most repetitive source of industrial noise came from pallet transportation: Coca Cola used tuggers to transport heavy pallets. At the time of this incident we had been using our tackers, which could move several pallets at a go on each trip.
- Route Planning: The distribution centers were modified so that these optimized routes for the tuggers passed through everything, nothing would be crowded between production and storage to loading docks.
- Safety Additions: These safety features were top of the line with some tuggers coming with radar-based collision avoidance systems and automatic stopping technologies. This reduced the chances of accidents and kept goods as well workers themselves safe.
Quantifiable Outcomes:
- Output increase of 25%-introduction tuggers Which in turn allowed the distribution centers to move more pallets more faster, and with less delay; increasing their overall productivity at a steady clip.
- Superior Safety Conditions: The high-class safety features on the tuggers led to a reduction of 40% in the number of workplace accidents caused by moving goods. This increased safety was not only protective to workers, but it also reduced the downtime due to accidents.
- Lower Equipment Maintenance Costs: Moving from forklifts to tuggers allowed Coca-Cola to decrease their equipment maintenance costs by 20%. As these devices are much simpler and of course more robust for continuous operation, they had to be maintained less often than before and this resulted in considerable costsavings.
Real-world Example:
- The tuggers Coca-Cola slotted into their Atlanta distribution center in a few days transformed logistics there. The center processes hundreds of thousands of beverage cases each year, and as much as 30% reduction in load/unload time at the pallet level significantly improved distribution efficiency.
- Efficiency Metrics: The same center also saw a 50% gain in operational efficiency during peak seasons due to the smoother incorporation of tuggers into their workflow. The approach permitted faster lead times and better inventory turns.
Coca-Cola is leveraging the power of Industry 4.0 with industrial tuggers to improve internal logistic solutions and update processes in production for consumer-packaged goods like food and beverage products. This raised the bar for other companies in relation to throughput, safety and cost-efficiency.
Pharmaceutical Industry
Real World Examples: Pfizer Manufacturing Plant
- Context: Pfizer, a global leader in the biopharmaceutical industry, was looking for a reliable means to transfer critical pharmaceutical compounds and materials from manufacturing facilities. Timely and accurate flow of these materials was essential for high standards of production and compliance.
- Solution: Pfizer subgrouped tuggers in their intralogistic. The tuggers were used to take materials between processing operations, helping everything through a process that remains smooth and efficient.
Implementation Details:
- Pfizer also requested that the tuggers Pfizer used were specifically designed for handling pharmaceuticals, as it's common for pharmaceutical materials to need a controlled environment to keep contaminants at bay. The tuggers had enclosed storage and climate control for the materials they transported.
- Optimization of Routes: Pfizer reconfigured its plant layout to optimize the routes in which tuggers moved around. This meant deciding how best to connect the different processing areas, ensuring shorter transit times and minimal cross contamination.
- Between automation and tracking: The tuggers were installed with the highest technology possible, which combined with real time location systems can help to track them where they are as well as the material statuses that have need transported. This control with an optics packaging solution improved the accuracy of moving fragile materials and related goods.
Quantifiable Outcomes:
- Tuggers Integration for Material Timely Delivery across Manufacturing Plant This improvement was imperative in order to keep the production schedule and meet the tight timelines that comes with pharmaceutical manufacturing.
- Inventory Management Accuracy: Also, using the tracking systems enabled Pfizer to have improved stock-management accuracy. The real time data access for effective monitoring and control enabled claims in place of anomalies and also created the correct environment where materials were always present as per demand.
- Reduction in Handling Errors: Tuggers reduced handling errors by 15%. This was made possible by material movement automation which diminished the requirement for manual intervention and thus, minimized human errors.
Real-world Example:
- Tuggers are used for internal logistics at Pfizer's largest manufacturing site in Kalamazoo, MI Within just a one year of incorporating the tugger system, WIPRO unit experienced an increase in their operational efficiency by 20% resulting in overall production boost (WIPRO produces n number of pharmaceutical products).
- Performance (Efficiency Metrics) — This facility also realized a 30% decrease in material transit time, improving the speed of their production processes drastically. This created more supply for Pfizer to meet demand and also maintain strict quality requirements of their products.
One example from the pharmaceutical industry is Pfizers use of industrial tuggers. Timely delivery, accurate inventory and rapid pick rates are the new benchmark of success for pharmaceutical manufacturing.
Retail and Warehousing
Amazon Case Study — Fulfillment Centers
- Context: Amazon is an e-commerce giant that owns and operates a constellation of large fulfillment centers across the globe Ensuring the fast internal inbound transit of many millions of goods one after the other daily, was a massive challenge for these centers. Amazon must keep up with millions of orders, so speed and accuracy in getting goods from receiving docks to storage tasks before sending it off the packing stations is mission-critical for its delivery promises.
- Answer: In an effort to automate and optimise this internal logistics process, Amazon introduced a fleet of industrial tuggers. The tuggers were employed to move goods smoothly between different sections in the fulfillment centers.
Implementation Details:
- Transfer to Storage: Items receive, get transferred to storage where it will be maintained in one of the fulfillment center storages areas. The tuggers are used to tow several bins or pallets at a time in one go for quick and smooth moving of these.
- Placeholder to Pack: At the time when an order is made, it must be picked up from a placeholder and moved over to packaging stations. Once inside the warehouse, tuggers once again have a crucial role to play in ensuring products are rapid and accurately conveyed where they need to be packed and shipped.
- Automatic Route Planning — Fulfillment centers uses advance software to plan the most optimum ways for tuggers. This reduces response times and improves flow of materials on the factory.
- Powered Drive with Safety Features: Tuggers come standard with sensors and stops to maintain a high level of safety while also preventing accidents.
Quantifiable Outcomes:
- Of course this is only one way to help streamline the order fulfillment process, however given how much you can accomplish with a high powered tugger it will have a big impact on reducing the time your products sit in between fulfilling orders and then heading out for delivery. Because this efficiency is needed to keep up with the promises of Amazon’s “Two-day Delivery”.
- Order picking was based on the assortment and prospective sales volume, therefore fulfilling orders with automated support to guide tuggers improved order execution accuracy by reducing errors leading to customers receiving improper products. It was measured as a 20% decrease in order errors.
- Lead-time Reduced: Driving tuggers has decreased the time in which products can be delivered to customers by 35%. What could be better than same-day packing and shipping, especially when Amazon has built its success on the speedy delivery of products?
Real-world Example:
- The impact of industrial tuggers at Amazon's fulfillment center in Robbinsville, New Jersey Operational efficiency at the center that processes millions of items daily increased by 50%. The reason for this was the faster, more accurate movement of goods throughout the building.
- Efficiency Metrics: The solutions provider for Robbinsville also saw a 40 percent reduction in internal time and materials labor related to transportation. The tuggers have reduced the amount of manual labor, thereby reducing physical strain for employees and allowing them to be more productive.
Amazon industrial tuggers summarizes the depth of avant-garde material handling solutions in retail and warehousing industry. Amazon — efficiencies & delighting customers Amazon still maintains the gold standard in economy of scale, order fulfillment and customer satisfaction by tight integration of inner logistics processes from receiving product into warehouses to delivering it at destinations rapidly.
Electronics Manufacturing
Samsung Case Study: Assembly Line Orchestration
- Background: A global king of electronics manufacturing, Samsung with a need to optimise their assembly lines was desperately looking for an answer. The goal is to improve the organization of the production floor, reduce material waiting times and increase overall productivity.
- BOS: Samsung implemented industrial tuggers on their assembly lines to move parts and completed product from station to the next (The Problem). The strategy was developed "to improve the flow of production and materials," according to language published with the announcement.
Implementation Details:
- Component Transport — Tuggers moved necessary components from the storage areas to the assembly lines It guaranteed that the assembly stations were always flushed with all necessary components which had the capacity to decrease time loss.
- Movement of finished products: Once assembled, the finished product had to be taken forward to testing stations for further conveyed towards packaging area. This was well-planned and seamless process thanks to the Tuggers.
- Route Forecasting- Samsung installed route optimization for the tuggers that had to move goods from point A to B by predicting the best routes. This was reinforced with live tracking and monitoring software to ensure accuracy and effectiveness.
- Safety improvements: To move around the production floor without causing delays and potential accidents, collision-detection sensors and automated guidance systems were installed to guide the tuggers.
Quantifiable Outcomes:
- They provided a more organized production floor on site as tuggers were used. Samsung managed to reduce clutter and enhance workflow by establishing routes and proper movement processes for articles.
- Shorter Waiting Times: The material tuggers kept the assembly stations continuously supplied with components, bringing the waiting times for materials down significantly. This eventually meant an improved production process with fewer interruptions.
- Production Capacity Improvement: The operating speed of the tuggers compared to human productivity increased production capacity by 20%. Samsung can produce more units in the same time period, which means they are very capable of meeting market demands.
Real-world Example:
- The integration of tuggers at Samsung's Suwon, South Korean manufacturing plant had a profound impact. The electronics plant that makes everything from smartphones to TVs reports a 25% decrease in material handling time. The increase helped accelerate production cycles and boost the output.
- Improvement Efficiencies: At the Suwon plant they were able to progress by 30% in reducing production bottlenecks as materials and components were made available accurately and on time, as per tuggers timely delivery. This resulted in the increase of the on-time quality of assembly lines and decreased strain on workers.
The use of industrial tuggers, as exemplified by Samsung, is a prime case for the benefits of modern material handling equipment in electronics manufacturing. Samsung proved to be the benchmark for operational efficiency in the industry by streamlining the production floor, reducing waiting times and enhancing its production capacity.