Electric Tugger: An Efficient Solution for Heavy Load Handling
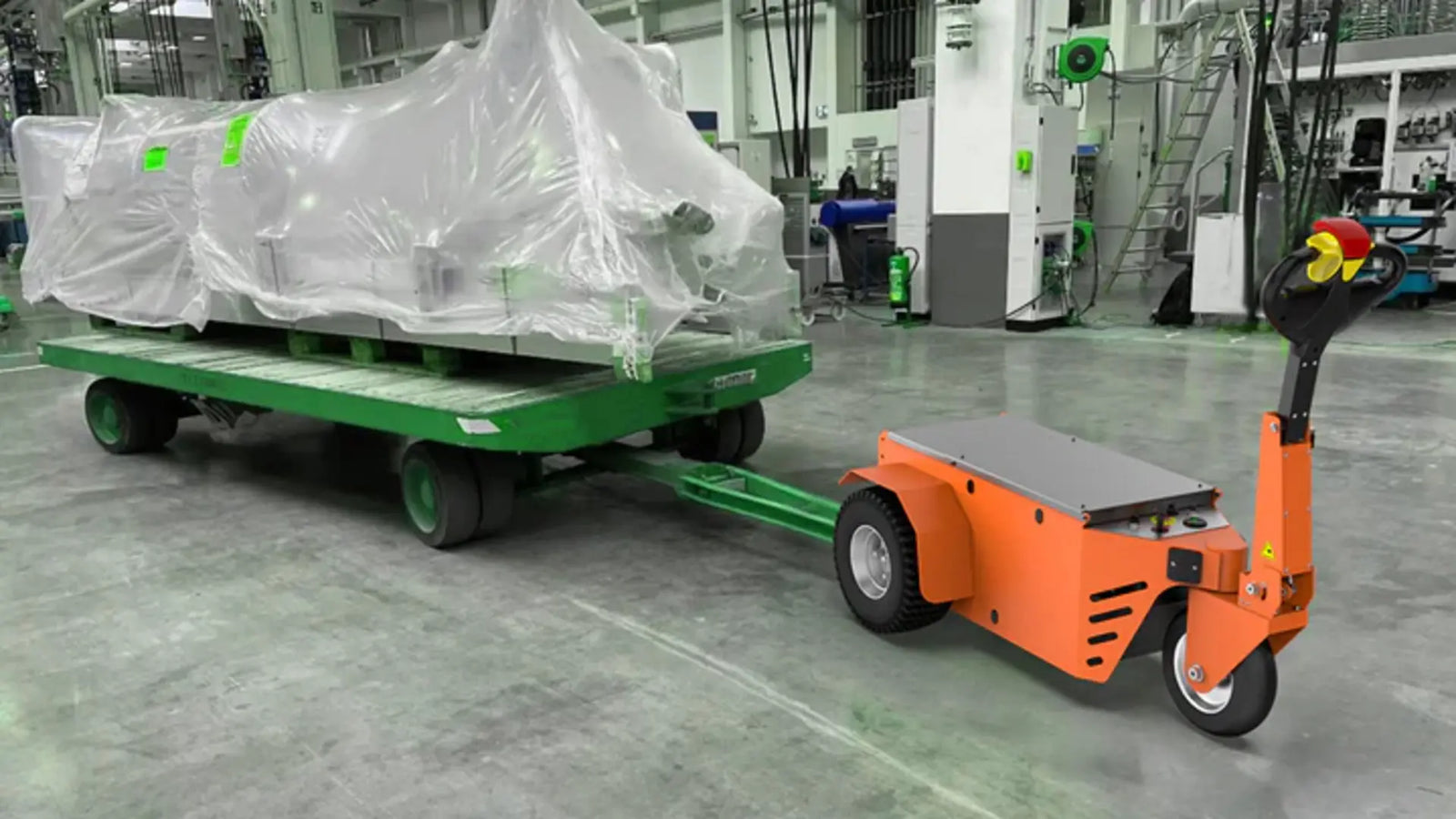
Its electric drive system allows it to easily handle several tons of material, with a single charge lasting 8-12 hours, suitable for long-term operations. Data shows that electric tuggers can increase handling efficiency by more than 30%, replacing the workload of 3-5 workers. The operation is simple, with control through a handle or remote for moving forward, backward, and turning. Equipped with automatic braking and intelligent navigation functions, it is suitable for multiple scenarios such as warehouses, factories, and logistics, effectively reducing the burden of manual handling.
Working Principle of the Electric Tugger
Electric tuggers operate through an electric drive system, with the core component being an electric motor, which drives the wheel group to move and push the heavy load. Electric motors are typically divided into two types: DC motors and AC motors.
DC motors, known for their simple structure and ease of control, are commonly used in smaller electric tuggers, ideal for lightweight handling tasks. On the other hand, AC motors are more suitable for high-intensity, long-duration work environments, providing stable and continuous power output, making them ideal for heavy load transportation.
Operators can precisely control the tugger through a handle or remote control, covering basic operations such as forward, backward, and turning. In addition, modern electric tuggers are often equipped with LCD screens, displaying real-time data on battery levels, load weights, and more, helping operators better control the equipment.
In some specific scenarios, electric tuggers are also equipped with intelligent control systems and automatic navigation functions, allowing them to autonomously choose the optimal driving route and avoid obstacles, further enhancing work efficiency and safety. Typically, an electric tugger can support 8 to 12 hours of continuous operation on a single charge, ensuring excellent performance in long-term, high-intensity transportation tasks.
Advantages of the Electric Tugger
First of all, electric tuggers excel at improving handling efficiency. According to industry statistics, using electric tuggers can increase work efficiency by over 30%. An electric tugger can typically replace the labor of 3 to 5 workers, effectively reducing labor costs, which is especially important in environments with labor shortages.
Secondly, electric tuggers are an ideal choice for environmentally friendly handling. They use electric power without requiring fuel and produce no emissions, fully meeting modern environmental standards. The application of electric tuggers is widespread, especially in industries with strict emission requirements, such as food manufacturing and medical equipment transportation.
Advances in battery technology are another significant advantage of electric tuggers. Modern electric tuggers commonly use lithium batteries, which not only have short charging times but also support thousands of charge-discharge cycles. The battery life of many high-end devices can last 5 to 7 years, greatly reducing replacement frequency and maintenance costs.
In terms of maintenance, electric tuggers have relatively simple structures, with routine maintenance focusing mainly on tire checks, battery maintenance, and motor lubrication. Compared to traditional fuel-powered equipment, electric tuggers reduce maintenance costs by 20%-40%, making them a cost-effective handling tool.
Wide Range of Applications
In warehouses, electric tuggers can flexibly handle narrow aisles and complex spatial layouts. With precise control, operators can quickly and efficiently transport goods from one shelf to another area, significantly improving storage turnover efficiency. Data shows that after using electric tuggers, the average turnover speed of goods in warehouses increased by 25%, greatly shortening the time goods are stored.
On factory production lines, electric tuggers also play an important role. They can seamlessly connect various production stages, transporting raw materials, semi-finished products, and finished goods, ensuring smooth production processes. Particularly on highly automated production lines, combining electric tuggers with automation equipment can further increase production efficiency and reduce the risk of production interruptions.
Logistics distribution centers are also key application scenarios for electric tuggers. They can efficiently handle large-scale goods loading and unloading, especially for heavy-duty tasks like handling tons or even tens of tons of goods. Electric tuggers can effectively reduce the burden of manual handling and improve overall work efficiency.
In addition, the use of electric tuggers is becoming more common at airports and ports. They are specifically used for handling large luggage, containers, and other equipment, often capable of handling single loads of up to 10 tons. In these scenarios, the use of electric tuggers not only enhances handling efficiency but also significantly shortens the docking time of planes or ships, improving the operational efficiency of airports and ports.
With the continuous development of electric tugger technology, intelligence and automation will become future trends, providing more efficient solutions for heavy load handling in various industries.