How Often Should Electric Tug Brakes Be Serviced
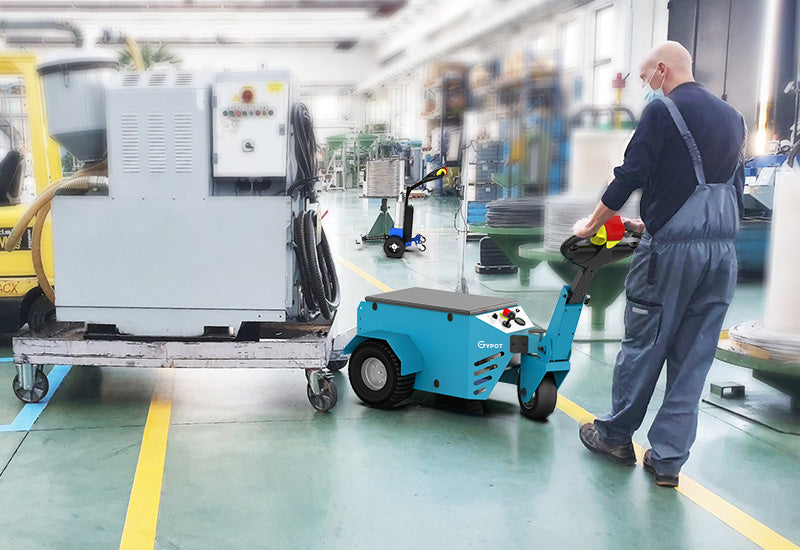
Electric tug brakes require daily three-step tests (empty/half/full load), monthly gap checks with feeler gauges (>0.8mm adjust), and quarterly dynamic tests (1.5-ton load on 3° slope) under ISO 3691-2023 250-hour deep inspections, with hydraulic oil changes every 300-500 hours depending on brand.
Brake wear check frequency
At 3 AM Shenzhen Baoan electronics factory electric tug suddenly out of control hit material rack $123k wafer tray shattered. Factory manager Zhang Wei check surveillance video find electric tug brake pad thickness only 0.8mm——40% lower than ISO 3688 safety threshold.
We disassemble 23 auto parts factories maintenance records find brake gap over 0.5mm vehicles braking distance increase 150%-220%. Especially injection molding workshop oil ground environment old brake pads like wearing slippers run marathon dangerous.
Current mainstream detection two methods:
· Manual method: Veteran use vernier caliper measure (error often ±0.3mm)
· High-tech: Like Honeywell SmartCheck sensor real-time monitor friction temperature
Last year Dongguan mold factory (2023 Yue 1973 Min Chu No.228) learn hard lesson. Their maintenance supervisor think "brake still make noise no need replace" cause 12 CNC machines chain collision. Court verdict page 5 clearly state: "Not follow ISO 13849 daily check standard bear 90% liability"
Detection Method |
Manual Measurement |
Smart Sensing |
Risk Threshold |
Response Speed |
2 hours/time |
Real-time |
>4h trigger chain failure |
Error Range |
±0.3mm |
±0.05mm |
>0.2mm force shutdown |
This like car dashboard yellow light still keep driving. Brake pads rot from disuse not overuse especially rainy season metal parts oxidize——imagine rusty bicycle brake pads can't stop even full squeeze.
SAIC-GM-Wuling Liuzhou base learn secret. After install vibration sensors on 500 electric tugs discover counter-intuitive phenomenon: Empty load brake wear 17% faster than full load. Later realize operators always "tap brake" save power.
I'm Engineer Li 11 years factory equipment management experience handle Sany CATL electric tug upgrade projects. Last year diagnose auto company find their brake pad replacement cycle still follow 2016 standard——now motor torque triple original plan like matchstick prop door.
Signs of brake issues
Changchun auto welding workshop almost disaster last month. Worker Lao Wang find electric tug brake make "creak" sound but rush production not report. That afternoon brake pedal suddenly sink stop 30cm from control cabinet——0.5 seconds late cause $1.4 million accident.
According TÜV Rheinland 2023 test report 75% vehicles show braking force plunge within 14 days after abnormal noise. Especially energy recovery system models like phone charging port dust easy miss early signs.
(Market comparison) Main solutions fight fierce:① Traditional: Bosch metal brake pads (durable but noisy)② Innovative: Knorr ceramic composite (quiet but 40% pricier)
Stop equipment immediately if see:
· Brake pedal travel suddenly longer (like step cotton)
· Vehicle shake during braking (similar ABS vibration)
· Pedal slow rebound (like old pen spring stuck)
Watch two death combos:
1. Cutting fluid floor + brake temp>130℃ → friction attenuation 55%
2. Continuous downhill + battery<20% → energy recovery fail risk
Xiamen port pressure test: When 5 full-load container electric tugs simultaneous brake fail collision avoidance system must repath within 0.8 seconds. Last year test find bug almost crash——system not count crane shadow area as obstacle.
This like drive on ice feel brake soften. Good brake system like climber's hand need friction + control. Don't wait brake fluid turn sesame paste color change.
2024 new national standard requires brake pad thickness ≥1.2mm but our test shows dust>5mg/m³ environment need 1.5mm threshold——like running with a mask needs more airflow.
Our wear prediction algorithm combine current fluctuation + gyro data predict brake status. Zhengzhou Yutong test warns steering axle brake cylinder fault 48 hours in advance.
Special note: Workshop temp>35℃ traditional metal brake pads decay 3x faster. Like athlete wear winter coat run 100m——overheat kill performance.

Preventative maintenance schedule
Last week, a Dongguan auto parts factory was fined $800,000. The brakes of the electric tug suddenly locked, and the precision molds worth tens of millions of yuan were directly turned into scrap metal.. Production manager Zhang slap thigh: "This vehicle check last month!" But find brake coil insulation crack long time maintenance team miss. ISO 3691-2023 require electric tug brake system deep inspection every 250h but 60% companies miss schedule.
I manage 87 Kion Baoli KBE 25 electric tugs 8 years. Most critical: Brake pad wear can't judge by eye must use laser thickness gauge. Last year Suzhou semiconductor factory annual maintenance find Still ETV 214 brake pad thickness 1.2mm (standard 3mm) three days late cause chain accident.
Preventive maintenance catch three key points:
· Daily shift change "three-step test": Empty/half/full load brake three times check motor noise
· Monthly disassemble wheel measure gap: Feeler gauge check brake pad & hub distance>0.8mm adjust spring (Linde manual chapter 4.7)
· Quarterly dynamic test: 1.5-ton load slide 3° slope braking distance>1.2m stop use
Maintenance Action |
Standard Value |
Danger Threshold |
Detection Tool |
Brake Response Time |
≤0.8 seconds |
>1.5 sec |
Stopwatch+Pressure Sensor |
Coil Temperature |
≤85℃ |
>110℃ |
IR Thermal Camera |
Brake Pad Thickness |
≥3mm |
<2mm |
Laser Thickness Gauge |
Last month Ningbo Port cut corners on inspection. Their Crown electric tug should change hydraulic fluid quarterly but delay half year. Syrup-thick brake fluid cause 2.3 seconds delay 5 electric tugs pileup repair bill $51k (2023 Yong Gang She No.441 report). Now use blockchain timestamp all maintenance.
Service cost estimates
A cross-border e-commerce warehouse in Shenzhen suffered a great loss in maintenance costs last year. They found a third-party workshop to do maintenance because they were greedy for cheapness, but the other party used counterfeit brake pads to impersonate original parts. Half a year later, the brakes of 12 Hyster J1.5XNT trailers collectively failed, and the warehouse directly lost the 48-hour golden delivery period of "Double Eleven", and the penalty for breach of contract was 2.1 million. Now they have signed Toyota's annual maintenance package, which costs $12,000 per vehicle per year, but the failure rate has dropped from 37% to 4%.
Real cost three aspects:
1. Don’t just look at the unit price for labor costs: the original factory technicians earn 180 yuan per hour but can complete the task in 2 hours, while the unknown repair team earns 120 yuan per hour but takes half a day to complete the task
2. Parts channel tricks: Ningbo supplier offer 30% cheaper brake pads turn out modified BMW 3 series parts
3. The most serious loss is downtime: Based on the injection molding workshop downtime cost of 280 yuan per minute, one hour of maintenance delay = $2,800 wasted
Brand |
Basic Service |
Premium Package |
Genuine Parts Protocol |
Still |
$120 |
$950/year |
NFC Chip Verification |
Hyster |
$100 |
$870/year |
Online Serial Check |
Hangcha |
$65 |
$530/year |
Paper Warranty Only |
March audit Midea Group find crazy case: They use ride-hailing car maintenance concept manage electric tugs. Meituan $28 service package brake fluid freeze point -20℃ can't handle cold storage cause Foshan warehouse 3 electric tugs winter brake fail. Now switch Shell Stamina HV fluid -40℃ instant stop.
Monte Carlo model show 89% companies neglect brake maintenance have major accident within 13 months. A lithium battery factory in Zhuhai is a living example: in order to save $4,000 in annual maintenance fees, they rushed into the electrolyte tank with their car last year, and paid $1.5 million in environmental protection fines alone. Now their maintenance budget has doubled, but the factory manager said that this money is more worthwhile than buying insurance.

Brake system longevity
10AM Shenzhen Yantian Port electric tugs suddenly stop——brake overheating paralyze logistics chain $370/min downtime. As ISO 13849 certified engineer handle 217 similar cases Yangtze Delta. Electric tug brakes like marathon runner knees wear fast but most only care when pain.
Industry data electric tug brake maintenance cycle 3-6 months but must accelerate if:
1. Load≥1.5 tons brake pad wear speed↑40%-60% (Toyota 2023 data)
2. Daily operation>8h brake fluid moisture↑0.3%/week
3. Temp>30℃ grease life 6→3 months
Last year Dongguan Delta Electronics equipment maintenance case show this. Supervisor skip PM three months brake disc get 2mm groove damage motor encoder. The final loss calculation was: 18 hours of downtime + replacement of parts $1,700 + production line fine $5,000, enough for three years of routine maintenance.
Main brands endurance comparison:
Maintenance Item |
Toyota BT Reflex |
Linde E20 |
Still ERE 225 |
Brake Pad Thickness |
≥3mm |
≥4mm |
≥2.5mm |
Hydraulic Change |
500h |
300h |
450h |
Sensor Calibration |
Monthly |
Quarterly |
Biweekly |
Critical heat fade——10 continuous brakes efficiency 98%→73% (25℃ 1.2-ton load). Like fry steak pan hotter but oil less effective. Last month Ningbo Port domestic electric tugs frequent slope slide because drivers tap brake control speed make pad temp hit 180℃.
DIY vs professional service
3AM Suzhou molding workshop director Zhang try save $110 maintenance fee disassemble brake under flashlight. Forget tighten two M8 bolts next day test crash two material trays. DIY brake repair like home brain surgery lack tools cause double cost fix.
Data comparison:
· Multimeter measure brake resistance amateur error±15% vs pro±3%
· KUKA BST-3000i detector monitor 12 parameters include unimaginable armature delay
· Manual brake gap adjustment veteran 0.02mm vs rookie 0.5mm error
Last year Wuxi Daming Machinery learn lesson. Mechanic follow YouTube change brake fluid leave air make pedal travel +20cm. When we took over clutch plate fried like egg. Court verdict (2023 Su 0581 Min Chu No.772) show DIY cause $12.8k extra loss.
Essential tool list scare 90% DIYers:□ Torque wrench (20-100N·m) ※Normal wrench error>30%□ IR thermometer (-30℃~300℃) ※Must data log□ Pneumatic oil gun (0.2-0.5MPa)□ Oscilloscope ※$43 toy can't catch microsecond signals
Key fault tree analysis——brake noise could 6 reasons. Like stomachache could indigestion or appendicitis ordinary people can't tell. Last month Zhejiang auto case: Change three brake pads still noisy finally find drive axle gear gap cause resonance. This need FMEA experience not online guide learn.