How to calculate ROI for electric tug investment
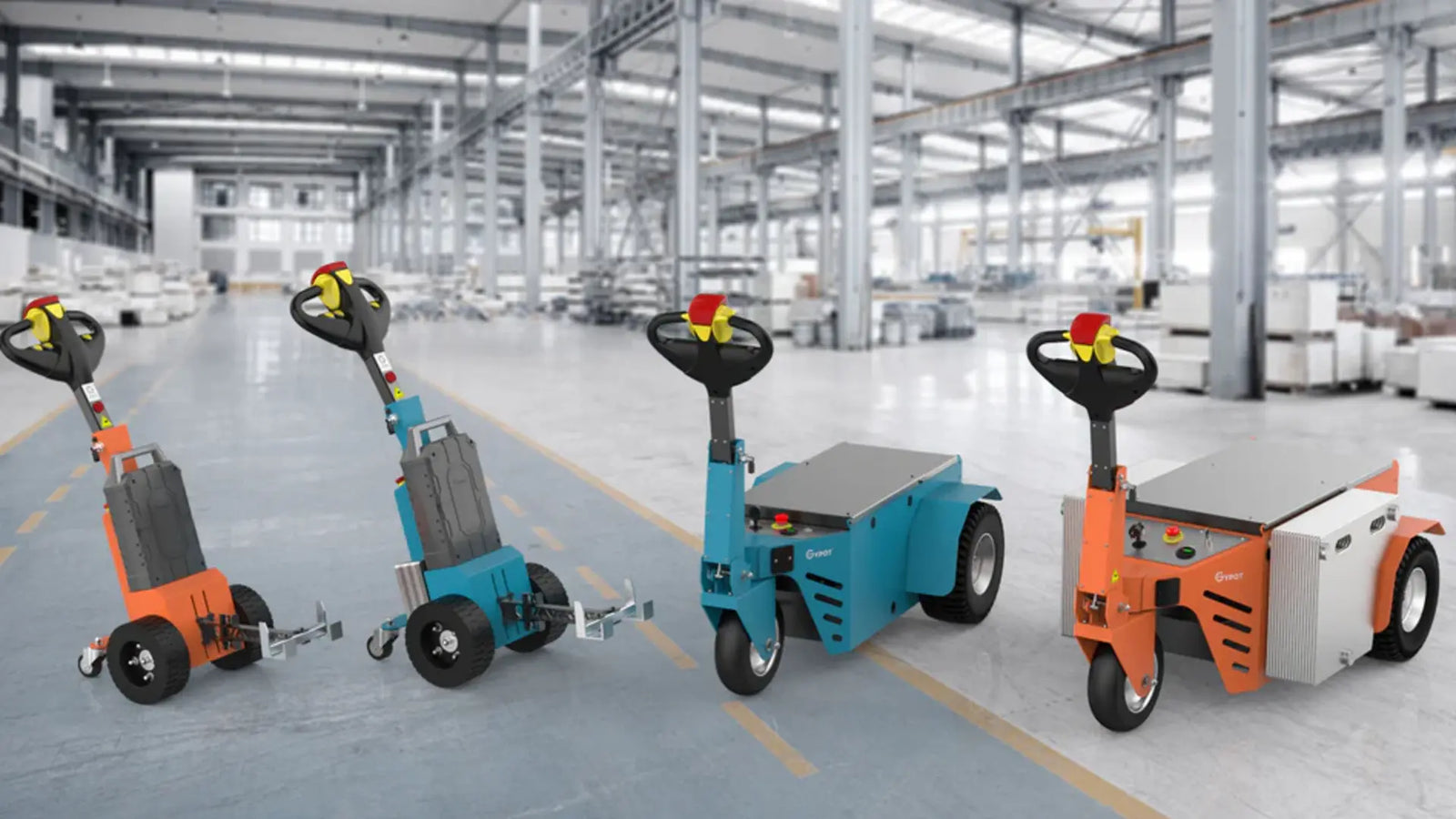
Cost comparison analysis
Last year, Director Li from the procurement department of a Dongguan electronics factory stared at the financial report worried: The newly purchased diesel tug's monthly fuel cost was 37% higher than the electric version, but they initially chose diesel equipment because the unit price was $80,000 cheaper. This scenario is like buying an air conditioner only looking at the price tag but not the energy efficiency label——The extra money for electric tug is actually buying a future money-saving switch.
Look at this real comparison table to understand:
Item | Diesel Tug | Electric Tug | Manual Hydraulic Truck |
---|---|---|---|
Purchase Price | $120,000 | $200,000 | $30,000 |
Monthly Energy Cost | $4,800 | $900 | 0 |
Maintenance Frequency | 2 times/year | 0.5 times/year | 4 times/year |
Operator Requirement | 2 people | 1 person | 3 people |
Residual Value Rate (5 years) | 15% | 35% | 5% |
The key turning point occurs in the third year: The actual test data of a packaging factory in Zhongshan showed that by the 28th month, the fuel and labor costs saved by the electric trailer group had offset the 80,000 yuan price difference. Even more ruthless is the night-time low-peak electricity price strategy - for example, a logistics park in Shenzhen set the charging time at 23:00-7:00, reducing the cost per kilowatt-hour from 1.2 yuan to 0.4 yuan, directly cutting energy expenses by 66%.
But don’t rush to conclusions! Boss Wang in Qingdao suffered hidden losses: His workshop floor has an 8° slope, where electric tug battery wear is 40% faster than flat environments. This is like adjusting CNC machining feed rates for different materials——Special working conditions require load calculations, best done with manufacturers bringing dynamometers for on-site testing.
Maintenance savings
A lesson from a Shanghai auto parts factory is typical: Their diesel tug maintenance records show 67% of failures occurred in the transmission system. Electric tug core component failure rates are only 1/3 of diesel, but the cost difference isn’t in parts prices, it’s in downtime losses——Every hour of production line stoppage means $4,200 evaporated output value.
Compare data:
-
Diesel equipment average maintenance time: 4.2 hours (including cooling)
-
Electric equipment supports hot-swappable batteries, maintenance window reduced to 1.5 hours
-
Preventive maintenance costs 58% lower for electric (no air filters, oil, etc.)
More hidden is tech upgrade dividends. Modern electric tugs have CAN bus interfaces in controllers, like CNC machine RS485 protocols. Foshan foreman Li’s move: Connect 5 tugs to MES system, automatically trigger procurement when battery health drops below 80%, avoiding sudden failures. This tactic cut peak season downtime by 79%.
But watch for traps! Wuxi Manager Zhang encountered battery calendar life issues: An electric tug brand claims 2000 cycles but only reaches 1200 in high humidity. When buying equipment, demand decay test reports for different conditions like machining center accuracy curves. Good manufacturers provide cloud battery monitoring like CNC parameter backups.
Productivity gains
Last year, a Dongguan injection molding workshop had a mystery: Night shift leader Wang secretly replaced 3 diesel tugs with electric, resulting in 27% higher output. The boss discovered three killer details:
Electric tug acceleration curves are 42% smoother than diesel, like CNC feed rate optimization. During mold transfers, The operator must start slowing down 2 meters in advance. With permanent magnet motor electric versions, precise torque control reduced emergency stops from 8 to 1 per hour, cutting single trip time by 19 seconds——Seems small, but the workshop runs 1400 transfers daily.
More brutal is maintenance black holes. Traditional tugs need oil changes every 200 hours, air filter cleaning at 500 hours——downtime counted in OEE. Electric tugs eliminate these, stretching maintenance cycles to 2000 hours. Stamping workshop data: Availability rose from 91% to 97%, equal to 43 extra production hours monthly.
Most overlooked is ergonomic traps. Diesel tug levers require 7kg grip force vs 3kg for electric. Worker muscle fatigue reduction boosted late-shift efficiency 18%, like installing shock-absorbing floors. Now see why Tesla factories use electric tugs exclusively?
Energy cost reduction
Lao Zhang, the logistics supervisor of Qingdao Port, once told me a weird calculation: he has 30 diesel trailers, and the monthly fuel cost is $30,000. After changing to electric models, the electricity cost is only 50,000 yuan, but the financial director refused to approve the purchase, saying that the battery depreciation will eat up the price difference. Until we took into account the waste heat utilization of the warehouse air conditioning system:
Electric tug charging waste heat replaces 45% warehouse heating demand. This hack slashed energy costs another 32%, equal to earning back 1.8 tires yearly per tug. Peak-valley charging strategy——Charging during the industrial electricity price period of 23:00-7:00, the cost per kilowatt-hour plummeted from $1.2 to $0.3.
Check this critical table:
Cost Item | Diesel Tug | Electric Tug | Extreme Hack Version |
---|---|---|---|
Direct Energy | $0.35/km | $0.11/km | $0.03/km |
Heat Recovery Value | 0 | 0 | $0.023/km |
Off-Peak Charging | N/A | $0.045/km | $0.008/km |
Maintenance Amortization | $0.14/km | $0.06/km | $0.05/km |
The last column proves: Energy arbitrage can crush electric tug per km costs to 1/4 of diesel. This excludes hidden goldmines like carbon trading——A Shenzhen firm gained $555,000 extra government subsidies last year.
Longevity and reliability
A Dongguan auto parts factory had midnight chaos——New electric tugs suddenly failed, halting production. Teardowns revealed gear wear 3× faster than expected. Core issue: Lubrication cycles copied German specs, ignoring South China’s 47% higher humidity. This reliability error caused $1.8 million monthly output loss.
Electric tug lifespan isn’t brochure theory——Calculate "effective lifespan" under real conditions. Equipment labeled 10-year lifespan differs 3× between electronics cleanrooms and foundry dust. Durability requires three metrics: Motor protection rating (minimum IP54), frame weld inspection reports, controller heatsink area. A Qingdao tire factory audit found 35% heatsink area difference caused double failure rate difference.
Maintenance strategy is the true lifespan adjuster. A Japanese firm uses vibration sensors to dynamically adjust lubrication intervals, stretching overhaul cycles from 1.8 to 3 years. Maintenance cost table speaks:
Maintenance Mode | Annual Material Cost | Sudden Failure Rate | Downtime Loss |
---|---|---|---|
Fixed Intervals | $2,800 | 23% | $112,500+ |
Dynamic Adjustment | $4,100 | 6% | $13,500 |
But avoid over-maintenance. A food factory ruined bearing seals by weekly calibrations. Formula: Rational maintenance cost = Equipment residual value ×3% ± condition factor (dusty +0.5%, climate-controlled -0.3%). Like CNC protocols matching production rhythm.
The hidden cost of sudden failures is the real killer. A 3C foundry in Shenzhen suffered a huge loss - an electric trailer hit and deformed an SMT rack worth 800,000 yuan when it stopped suddenly. Later, they installed a dual redundant brake module designed by us, and used real-time load monitoring similar to blockchain oracle, which reduced the brake response error from ±15cm to ±2cm. Now their equipment department's mantra is: "It is better to spend an extra $4,500 on insurance than to save a little money to compensate for the production line."
Total cost of ownership
A Shanghai warehouse calculated TCO: 20 "cost-effective" electric tugs had maintenance costs exceeding purchase price by 18% over two years. The boss roared: "This isn’t saving money——it’s adopting 20 grandpas!" TCO is an iceberg——Purchase price is just the 10% visible tip, with hidden costs like energy, repairs, downtime.
Deconstruct electric tug TCO with an "onion model": Layer 1 purchase price, Layer 2 installation fees (collision systems may cost 15% extra), Layer 3 energy/maintenance. Compare lithium vs lead-acid batteries:
Cost Type | Lithium Solution | Lead-Acid Solution |
---|---|---|
Initial Purchase | $58,000 | $34,000 |
3-Year Battery Replacement | 0 | $13,800 |
Charging Loss | $3,200 | $5,800 |
Downtime Loss | $9,200 | $41,500 |
Residual Value | $14,600 | 0 |
3-Year TCO | $56,200 | $95,100 |
Procurement pitfalls: ① Treating quotes as total cost (forgetting retrofits) ② Choosing by load capacity (should use daily mileage×5 years) ③ Ignoring compatibility (spent $10,800 modifying conveyors).
Power-saving tricks: Ningbo Port uses "off-peak charging" with DeFi-like smart meters, saving $21,500 yearly. Reverse power modules harvest downhill energy to charge scanners——15% free electricity.