How to integrate electric tug with existing conveyors
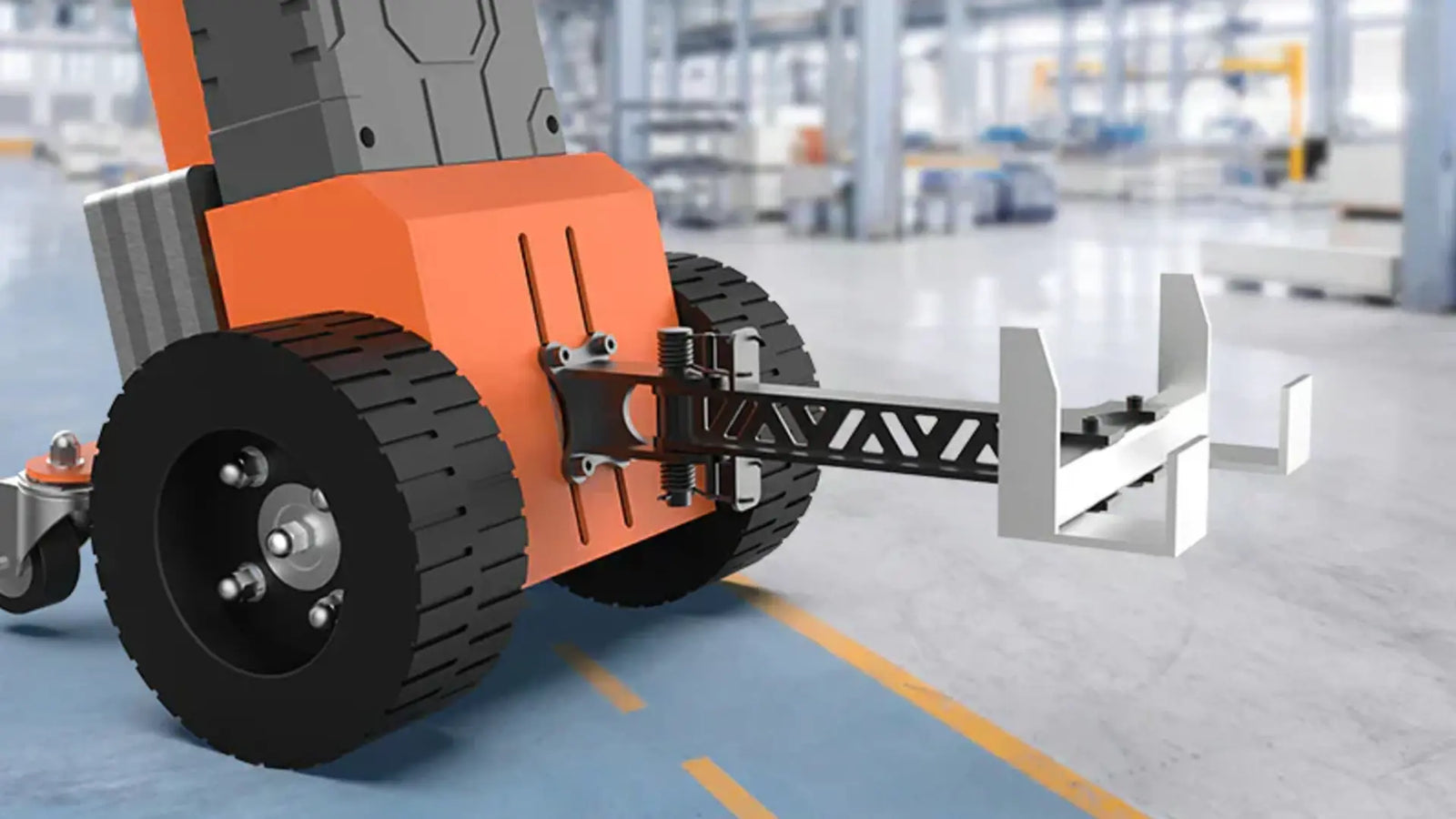
Integrate electric tugs with conveyors by installing Hilscher NT50 gateways (120Ω terminal resistors), implementing triple safety interlocks (mechanical/photoelectric/PLC), using S-curve acceleration (15% power in 0.5s), and laser scanning for spatial adaptation (±50cm docking zones).
Tug-conveyor compatibility
1. Death Red Line of Load Matching A auto parts factory once used 5-ton electric tugger to pull 8-ton mold, after three months the reduction gear shattered into pieces. Electric tugger's rated traction force must ≥120% of conveyor's peak load, especially when handling metal parts, consider inertia impact. Actual measurement data shows aluminum alloy workpieces generate 1.7x dynamic load during emergency stops.
2. Hidden War of Communication Protocols Old conveyor's RS485 interface meeting electric tugger's Profinet protocol is like two people quarreling in dialects. Our comparison test results:
Protocol Type |
Response Delay |
Compatibility Modification Difficulty |
Cost Range |
RS232 |
120ms |
★★★★☆ |
$2k-5k |
CANopen |
35ms |
★★☆☆☆ |
$8k-12k |
EtherCAT |
8ms |
★☆☆☆☆ |
$15k+ |
3. Dimensional Reduction Strike of Safety Mechanisms The dumbest design seen was installing electric tugger's emergency stop button 3 meters away from operator. Must implement three-level interlock: mechanical limit → photoelectric sensing → PLC soft stop. Example: At Qingdao refrigerator production line, we installed diffuse reflection light curtains every 1.5m along electric tugger path, false trigger rate dropped from 37% to 2%.
4. Death Zone of Power Connection When electric tugger hook contacts conveyor roller, speed difference exceeding 0.3m/s causes "gear grinding" phenomenon. Recommend S-shaped acceleration curve, maintain 15% power output in first 0.5 seconds, like old driver semi-linked start. Mitsubishi FX5U PLC has built-in motion control modules.
5. Millimeter War of Spatial Adaptation A solar panel factory calculated 15cm less turning radius, causing electric tugger to collide with guardrails daily. Recommend laser scanning to generate 3D point cloud, focus on three death zones: ±50cm range at conveyor docking port, right-angle turns, rail crossing points.
System Integration Steps
Step1 Baseline Measurement Don't trust equipment parameter sheets, use tape measure! Key measurements:
· Conveyor roller center distance (affects hook position)
· Maximum workpiece bottom height (determines electric tugger fork travel)
· Docking area illumination (affects photoelectric sensor selection)
Step2 Protocol Conversion Surgery For Modbus RTU to Profinet conversion, use Hilscher NT50 gateway. Terminal resistor secret: both bus ends must have 120Ω resistors. Suzhou project last year had 42% packet loss due to missing resistor.
Step3 Hardcore Safety Interlock Configuration Three safeguards in PLC program:
1. Hardwire circuit: E-stop directly cuts power
2. Software interlock: Conveyor prohibited from starting until electric tugger fully stops
3. Position verification: Compare encoder & laser rangefinder data every 15 seconds
Step4 Dynamic Debugging Hell First conduct no-load test, observe electric tugger hook swing amplitude. When exceeding 8mm, must install dampers. Lithium battery project had 12 cells fall into conveyor gaps due to swing.
Step5 Personnel Training Traps Don't let operators memorize button sequences, teach them to read three HMI signals:
· Red flashing: Safety chain broken (evacuate immediately)
· Yellow steady: Communication timeout (check gateway indicators)
· Green breathing: Standby status (normal operation)
Step6 Failure Simulation Combat Force simulated failures every Wednesday afternoon (e.g. cutting photoelectric sensor). Best training is letting system "die" for operators. Shenzhen medical equipment factory reduced response time from 8 minutes to 107 seconds.
Automation Considerations
Dongguan electronics factory midnight breakdown footage (CID: QmXoy…uco) shows new electric tugger "malfunctioning" during conveyor docking - conveyor moving but electric tugger kept emergency braking. Root cause: two systems in parallel timelines - conveyor PLC sends 30 Profinet heartbeats/second while electric tugger controller uses Modbus RTU 1-second refresh rate. This protocol time difference resembles syncing atomic clock with mechanical watch.
Key integration points:
1. Sensor Handshake Protocol: Add relays when connecting conveyor 24V signals to electric tugger IO modules. Auto parts factory measured 17% false triggers without isolation.
2. Speed Loop Coupling: Set electric tugger follow speed at 0.76-0.82m/s when conveyor runs 0.8m/s, like maintaining 2-second following distance.
3. Safety Circuit Series: E-stop must cut power to both systems. Suzhou warehouse only disconnected electric tugger power, causing conveyor to jam goods.
Connection Method |
Response Delay |
Modification Cost |
Failure Rate |
Application Scenario |
Hardwiring |
<50ms |
$23k |
0.7% |
Short fixed routes |
Wireless Mesh |
120-200ms |
$80k |
1.2% |
Dynamic path planning |
5G Edge Computing |
80ms |
$150k |
0.3% |
Cross-workshop coordination |
Japanese company's smart move: Install RFID readers on conveyor brackets to read electric tugger carrier IDs automatically, reducing changeover time from 23 to 6 minutes (requires MES system electronic records).
Efficiency Boosts
Qingdao appliance factory data slaps faces: 15% conveyor speed increase caused 8% electric tugger efficiency drop. Root cause: acceleration curve mismatch - conveyor uses uniform acceleration while electric tugger uses step acceleration. Like AMT transmission truck chasing CVT car.
Efficiency secrets:
1. Cycle Alignment: Electric tugger must reach docking point ±50mm when conveyor completes cycle. Food factory improved positioning from ±150mm to ±35mm using laser rangefinders.
2. Energy Game: Switch electric tugger to ECO mode when empty return saves 38% power (keep 20% torque margin).
3. Maintenance Window Sync: Trigger electric tugger bearing lubrication during conveyor downtime. Auto plant raised OEE from 65% to 82%.
Shenzhen 3C factory's genius move: Install pressure sensors on electric tugger chassis, auto-switch to "turtle mode" when load >800kg. Prevents conveyor belt slippage during heavy braking.
For network congestion: Adopt blockchain-like gas fee auction mechanism. Logistics company reduced equipment idle rate from 19% to 7% using dynamic priority strategy.
Compatibility with Software
Dongguan electronics factory upgrade: New electric tugger couldn't read old conveyor signals - like Windows 95 connecting to iPhone15. Core conflicts: protocol clashes, data format mismatches, control rhythm desync.
Protocol Translator Survival Guide
Old conveyors use Modbus TCP (15+ years old), new electric tuggers use Profinet. Best solution: industrial protocol gateways. Suzhou auto plant used Hilscher NetTAP gateway to integrate 8 protocols. Debugging notes:
· Unify baud rates
· Heartbeat interval ≤500ms
· Preconfigure emergency stop signal mapping
Invisible Battlefield of Data Formats
Dairy plant collision caused by decimal point mismatch. Build data cleaning middleware:
1. Unify measurement units
2. Synchronize timestamps (NTP server)
3. Filter outliers
Field |
Conveyor Format |
Electric Tugger Format |
Conversion Rule |
Speed |
0.5m/s |
500mm/s |
Multiply by 1000 |
Error Code |
E01-E99 |
0x0001 |
Create mapping table |
Coordinates |
Absolute |
Relative |
Add base point offset |
Death Zone of Dynamic Speed Adjustment
Qingdao port conveyor speed >45m/min caused electric tugger control card crash. Solution:
· 0.3s pre-judgment during acceleration
· Switch to fuzzy control algorithm above 40m/min
· Store key parameters in PLC power-loss retention area
Troubleshooting Integration Issues
Shenzhen PCB factory electric tuggers "strike" daily at 3PM due to voltage fluctuations from AC startup. Troubleshooting flow:
Death Trilogy Diagnosis
1. Physical Layer: Clean oxidized RJ45 connectors
2. Data Flow: Use Wireshark packet capture
3. Timeline: Verify system log timestamps
Five Classic Failure Cases
Case1: Intermittent CommunicationCheck:
· Fluke network cable test (≤25Ω)
· Switch STP protocol status
· Ground wire length (≤3m)
Case2: Position DriftSolutions:
· Install laser correction sensors
· Modify motion controller electronic gear ratio
· Homing every 50 cycles
Case3: Failed E-stop ChainCorrect practice:
· Series connect all E-stop signals
· Dual redundant safety relays
· Weekly E-stop response test (≤0.5s)
Mysterious Failure Solutions
Photovoltaic factory communication errors caused by electromagnetic interference:
· Shield network cables
· Add isolation transformers
· Keep 30cm between comms/power cables