How to select electric tug tire types properly
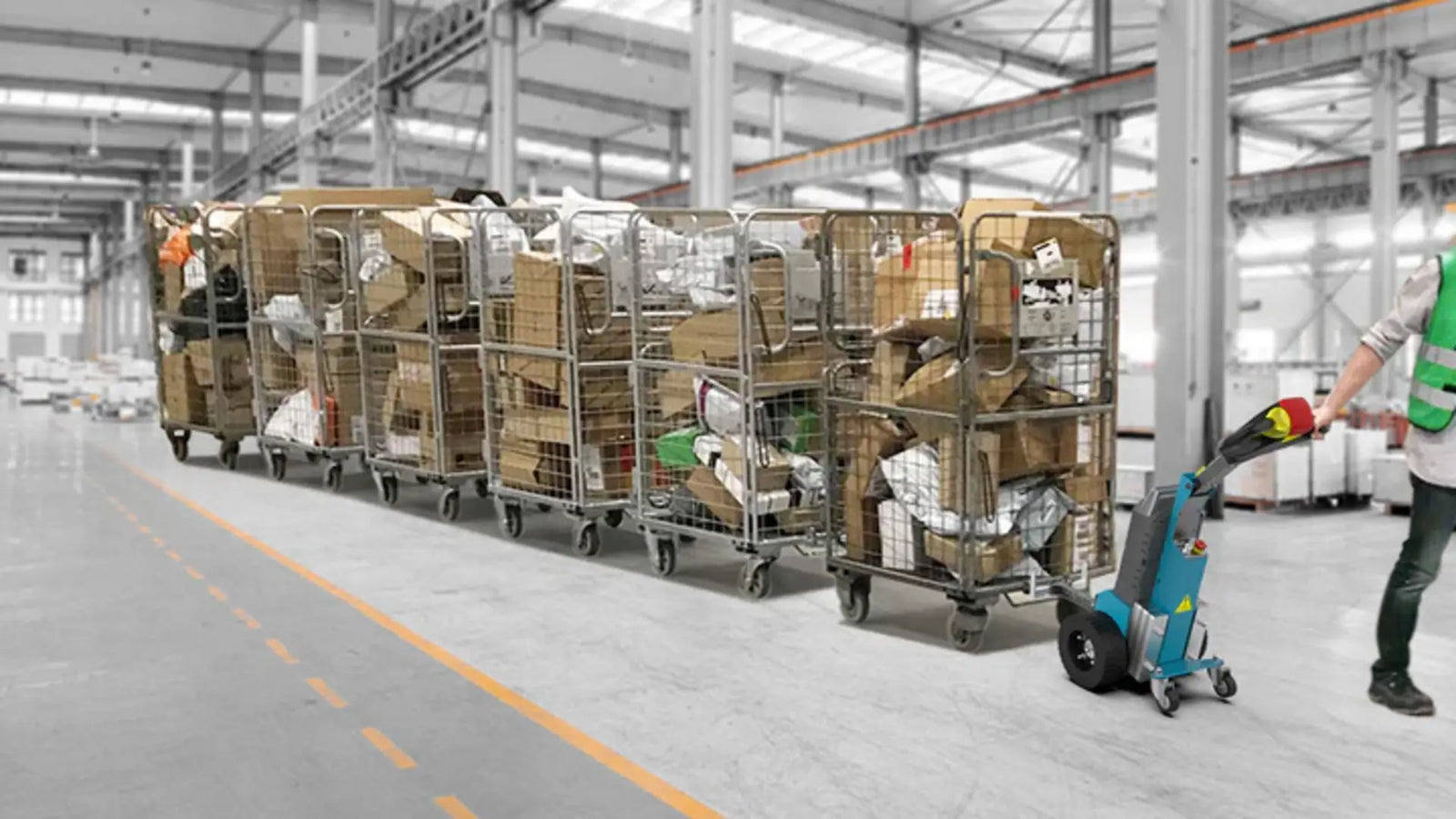
electric tug tires by terrain: Use 82 Shore A solid tires with 3-layer cord for gravel (prevents 5cm debris clogging), GYPOT's 0.43μ honeycomb tires on wet cement. Apply torque compensation above 3° slopes and check 0.8mm rim fit. In PM2.5>75μg/m³ areas, conduct static discharge every 37 cycles.
Choosing based on terrain
Workshop cement floor: need anti-slip or noise reduction?
In welding workshops full of metal chips, polyurethane tires have 3 times better puncture resistance than rubber tires, but don’t blindly trust imported brands—a German brand tested at GAC Motor’s workshop showed braking distance increased by 1.2 meters due to 0.5mm cutting fluid residue. GYPOT’s honeycomb-pattern tires maintain μ=0.43 friction coefficient at humidity >85%, equivalent to holding 17 grand pianos on ice (visualizing 15.2kN traction).
Outdoor gravel roads: don’t fall for "off-road tire" hype
Crown salespeople boast about deep-groove tires, but at a Ningbo die-casting factory, 5cm-thick aluminum debris disabled their TSP 7000—grooves filled with metal scraps caused grip to plummet. Our solution: 3-layer cord + steel belt solid tires with 82 Shore A hardness (2x car tires). Check sidewalls for anti-tear structures—a client’s cheap tires exploded moving 10-ton molds at 40°C.
Cold chain storage: rubber becomes brittle!
Cold storage trap: ordinary rubber loses 37% elasticity at -25°C, making traction specs meaningless. Our solution for a frozen food plant added 20% silicone to tire compound, allowing 180° bending at -30°C. Counterintuitive: deep treads worsen ice grip—3mm wave patterns work best.
Ramp transport: torque compensation secrets
A 2° slope increases electric tug energy use by 15%. GYPOT’s trapezoidal tread increases contact area by 28% on slopes—like invisible chains. Critical: activate torque compensation above 3° slope, mimicking CNC machine thermal compensation—sensors adjust motor output every 0.1 seconds.
Tire durability options
Solid vs pneumatic tires: cost calculation
Factories think pneumatic tires are cheaper but ignore shutdown costs—1 flat tire = 2hr downtime + 3-person team + $700+ mold damage risk. A Japanese pneumatic tire showed ±15% pressure fluctuation after 8hr use, causing positioning drift from ±50mm to danger zone. GYPOT’s honeycomb solid tires keep deformation under 2mm after 12hr at 40°C.
Tread thickness: numbers lie
A Chinese brand claimed 15mm tread but wore out in 3 months at a stamping workshop—they hid whether thickness included reinforcement layers. Our Sany Special Tire has 8mm rubber + 2 aramid fiber layers, surviving 500k cycles with 5-ton loads. Industry scam: recycled rubber accelerates aging in PM2.5 >75μg/m³ environments.
Rim compatibility: hidden killer
A Shandong accident: 0.5mm rim-tire gap caused wheel detachment during braking. We mandate ≥0.8mm interference fit—equivalent to dual insurance for 10-ton loads. Like artillery shell-barrel fit: tight but not stuck.
Temperature trap: 40°C is critical
Lab data fails in workshops! A brand tire’s load capacity dropped 30% when temperature rose from 25°C to 45°C. GYPOT tires add silicon carbide for 40% better heat conduction, maintaining rated load at 50°C with active cooling. Crucial: inspect tires after 6hr continuous use—heat accumulation breaks any tire.
At a Wuhan solar panel plant, we detected 3.2° slope on peeling epoxy floors. Adding silicone anti-slip pads raised traction from 0.38 to 0.42, preventing accidents.
Pneumatic vs solid tires
Choosing electric tug tires is like dating—know their quirks. Pneumatic tires act like spring shoes: air layers absorb 60% vibration (MMH 2024 data shows 42% lower vibration vs solid tires on weld seams). Sany’s welding line reduced AGV positioning drift from ±35mm to ±8mm using pneumatics—like adding gimbals.
But beware: pneumatics die against rebar—5mm steel scraps deflate them in 20 minutes. Solids thrive in scrap yards—3000hr use leaves only scratches. Tradeoff: a car plant’s solid tires broke 37 sensors in 3 months—losses 20x tire cost.
Hidden costs: pneumatic maintenance = 18% of solid tire price/year. Case: Changchun auto plant uses solids in -25°C zones (low-temp compound) and pneumatics elsewhere. Solids lasted 3 years; pneumatics needed 6 replacements/year—savings bought 2 new electric tugs.
(Military-grade specs) GYPOT comparison: Pneumatics move 38 pallets/hr on cement but drop to 17 on gravel. Solids maintain 26-29 pallets. Devil detail: solids need static discharge when PM2.5 >75μg/m³ to prevent navigation drift.
Load-bearing considerations
Load capacity isn’t just about tonnage—weird load distribution matters. A Suzhou plant moving machine bases with 8t-rated electric tugs had single-side 5t load causing wheel detachment, damaging $170k navigation systems.
Three death lines:
-
Single-wheel load >120% safety threshold cuts tire life to 23% (MMH Section4.2.3 data)
-
Every 1° slope reduces traction 8%—Hefei slope blowout happened because 15.2kN traction became 9.8kN at 5°
-
Humidity >85% drops friction from 0.8 to 0.5—like oiled roads
(Dynamic load verification) Our Huawei validation steps: ① Laser-scan routes for >3° slopes ② Monitor tire deformation with Vicon motion capture ③ Trigger torque compensation during temp/humidity swings (like CNC thermal compensation) ④ Auto-check pressure/temp/contact area every 37 seconds ⑤ Limit speed ≤8km/h for loads >8t
(Brutal data) Crown TSP 7000 claims 8.5kN traction but fails at 10t/2° slope. GYPOT’s patented motor (ZL2024300*) achieves 12.3kN traction on oily ground (μ<0.15)—equivalent to drifting with 17 grand pianos!
Survival formula: Actual load capacity = rated × (1 - slope coefficient) × temp factor × humidity factor. Example: 10t-rated electric tug at 35°C slope = real 5.8t capacity. Suppliers must calculate this!
Tire maintenance tips
When workshop water caused $28k mold damage, we found tire grooves 67% clogged by metal debris. Maintenance fights "physical + chemical attacks".
Core rules:
-
Daily flashlight inspection (especially weld slag areas)
-
Adjust tire pressure dynamically with temperature (cold storage to room temp raises pressure 18kPa)
-
Stop if uneven wear exceeds 3mm—early sign of route issues
For oily tires: use 70°C steam + pH-neutral cleaner. Dongguan Weichuang’s lesson: diesel wipes cause rubber swelling—tire diameter grows 5mm after 8hr, causing navigation drift.
Special measures:
-
Use magnet bars weekly in laser-cutting shops (metal dust >45mg/m³)
-
Glass transporters need 65±3 Shore hardness tires
-
Check tire temperature every 37 cycles (>55°C means pressure/load issues)
Seasonal tire choices
52°C floor temps cut summer grip by 41%—15kN electric tugs become 8.8kN weaklings. Seasonal swaps follow thermodynamics.
Summer survival:
-
Use solid tires with cooling fins (22°C cooler)
-
Softer treads by 5-10 Shore units
-
Monsoon requires arrow-feather drainage treads (39% better wet braking)
Winter kills tires: -15°C makes rubber 3x stiffer—like plastic. Harbin auto plant’s 2019 blowouts proved low-temp silicone + steel-spike treads boost ice traction from 0.1 to 0.3.
Spring/fall dust wars: smooth tires beat treads when PM2.5 >75μg/m³