What Is the Role of Tuggers in Warehouse Logistics
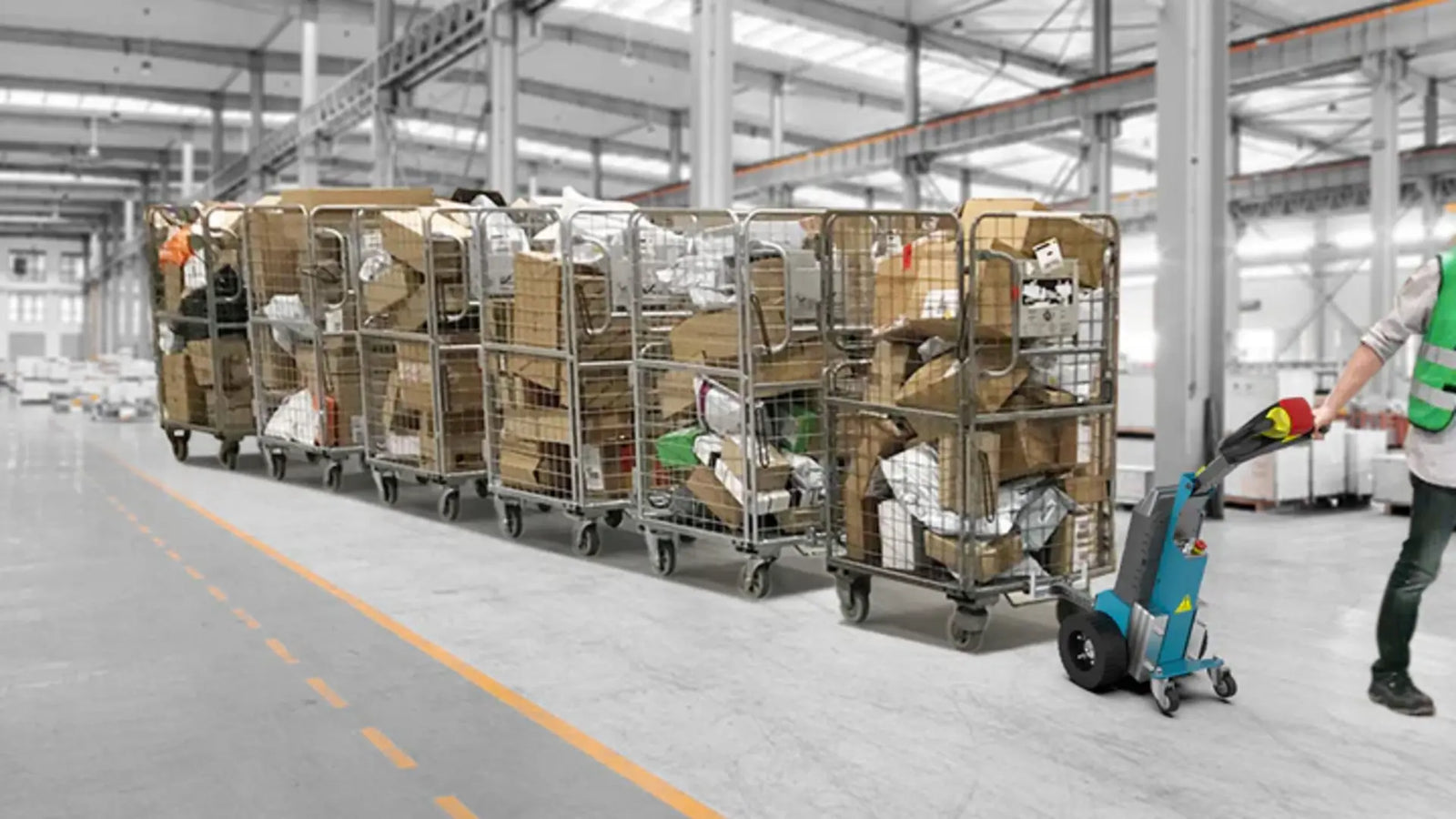
While electric tuggers may optimize the productivity of a warehouse by as much as 30%, they can handle loads ranging from 1,000 kg to 5,000 kg with minimum operator strain. It achieves route optimization and utilizes wireless control to decrease the trip frequency, thereby economizing time and energy for seamless operations.
What is an Electric Tugger?
Electric tuggers are material handling vehicles that help in moving big and heavy loads in an effective and efficient manner in warehouses, distribution centers, and industrial facilities. Whereas forklifts move loads vertically, electric tuggers are designed to work horizontally in pulling or towing carts and other wheeled loads. Such positioning of the machine allows it to carry several loads at one time and smoothes workflow by reducing trips across the warehouse floor. Advanced drive systems and ergonomics on electric tuggers reduce the physical demands on operators, boost productivity, and further workplace safety.
Basically, electric tuggers differ in their technical designs for applications. They range from manually operated electric tuggers that offer some degree of operator control to fully automated or remotely controlled tuggers that offer hands-free operations. The manual ones have ergonomic controls to reduce operator fatigue, while the automated design has sophisticated navigation and control technologies that include sensors and software, enabling autonomous movement.
Types of Electric Tuggers
Electric tuggers have been categorized into various types according to their application, load capacity, and their control systems. Each kind has been designed to meet certain requirements for operations so that material handling in different industries becomes effective. Major types of electric tuggers include:
Manual Electric Tuggers
The manual electric tuggers are directly driven by personnel with hand controls, maneuvering the vehicle in any way desired. They do exceptionally well over shorter distances and with lighter loads, providing simple yet efficient solutions for tight environments where space is limited and maneuverability is paramount. Although very good in their purpose, they are unsuitable for heavy-duty or long-distance applications. Manual electric tuggers, however, are affordable equipment for small warehouses and retail outlets.
Remote-Controlled Electric Tuggers
The wireless control systems on Remote-Controlled Electric Tuggers enable the operator to control movement and speed from a distance. This has been made possible with radio frequency or Bluetooth technology, allowing operators to handle a tugger from a safe distance, which is useful in crowded and hazardous areas. It enhances maneuverability, improves safety for operators, and makes the tugger viable for complex layouts of warehouses or confined spaces devoid of direct handling.
Heavy-Duty Electric Tugger
The Heavy-Duty Electric Tugger is designed for high-capacity applications, using heavy-duty structures and high-powered drive systems to move extremely heavy loads. Such tuggers are highly important in industries that involve the manufacture of large-sized and heavy items, such as in automotive and aerospace. Heavy-duty tuggers normally incorporate high-powered DC brushless motors and sophisticated motor controllers to maintain reliable operation under intense conditions.
Automated Electric Tuggers
Advanced navigation systems are enabled on Automated Electric Tuggers with mounted LiDARs, cameras, and sensors to enable autonomous operations within predefined routes or dynamically changing environments. Often integrated with WMS and MES, these automated tuggers can perform material handling tasks requiring minimum human interference, hence enhancing efficiency and reducing labor costs. The autonomous capabilities of these tuggers are perfect for large warehouses and highly automated facilities.
Key Benefits of Electric Tuggers
Technical sophistication sets up several direct benefits that come with electric tuggers, making them indispensable in material handling. These benefits result from a combination of the following: an ergonomic design, modern drive technology, and intelligent control systems.
The ergonomic shape of electric tugger handles is designed in a way that drivers can operate the vehicle with minimum physical exertion. Handle shapes are fitted to the natural curve of the hand, with anti-slip materials for secure grip over long use. Controls for accelerating, braking, and turning are integrated into the handle, allowing precise maneuvering without needing complex actions. Electric tuggers become more comfortable for an operator when used for extended or frequent operation, considering ergonomics to reduce operator fatigue.
Wireless control systems further extend the capabilities of electric tuggers, enabling operators to operate the vehicle from a distance. This remote operation capability is invaluable in areas where the layout is complex and storage is at high density, making direct access to the tugger challenging. By eliminating the need to physically touch a tugger, accidents are reduced, as operators can stay at a safe distance from the tugger and its load. The remote control will have RF or Bluetooth technology for reliability and immunity to interference.
The drive assembly of an electric tugger comprises a DC brushless motor and drive axle assembly. Compared to traditional brushed motors, brushless DC motors offer several advantages: lower noise, lower energy consumption, and longer service life. In brushless motors, the function of mechanical brushes is taken over by electronic commutation, which decreases friction and wear, thus improving efficiency. This allows the tugger to work continuously for extended periods without overheating, making it ideal for high-duty cycles. The drive axle converts rotational energy from the motor into linear force, essential for exerting traction and moving heavy loads smoothly and efficiently.
Other imperative parts that make up an electric tugger are high-performance, brushless motor controllers. These controllers drive the operational parameters of the motor, including speed, electromagnetic braking, and maintaining operating temperatures within acceptable limits. By controlling the current supplied to the motor, the controller regulates speed with smooth acceleration and deceleration under various load conditions. This sophisticated control increases the reliability and responsiveness of the tugger for continued use in multiple applications. Controllers may also feature thermal protection to guard against overheating, ensuring a long life for the motor.
How Electric Tuggers Work
Electric tuggers rely on interdisciplinary and integrated mechanical, electrical, and electronic parts for smooth and reliable performance. Fully understanding these components and their interaction reveals how electric tuggers achieve high efficiency and versatility.
To initiate and operate an electric tugger, the vehicle is turned on by the operator via handle or remote control. The handle will have directional controls, such as forward and reverse, along with buttons to steer it. The same functions are possible with remote control from much longer distances. Control inputs are relayed to the motor controller, where the motor output is adjusted accordingly. In complex warehouse settings, this system allows operators to navigate precisely around obstructions and through narrow aisles.
A DC brushless motor provides the torque to move large masses. In brushless motors, this is achieved by the periodic change in polarity of the electromagnetic field in the stator, turning the rotor without any physical contact. This reduces wear and allows the motor to run quietly and efficiently. An intermediate gear assembly couples the motor with a drive axle that converts the rotational motion into linear motion, allowing the tugger to operate comfortably even under full load.
Lithium-ion and lead-acid rechargeable batteries power different models and applications. Li-ion batteries offer high energy density and long cycle life, suitable for operations requiring frequent charge cycles. Lead-acid batteries are heavier with a shorter lifespan but are economical for less demanding applications. Power distribution and protection against over-discharge or overheating are managed by a BMS that monitors the state of charge, temperature, and battery health, ensuring efficient and prolonged operation.
A critical aspect of electric tuggers is the braking system, essential for safe operation. Most tuggers employ electromagnetic brakes that engage once the motor de-energizes, providing a fail-safe stopping mechanism. Electromagnetic brakes work by generating a magnetic field that attracts a metal armature to the rotor, halting the motor. This responsive braking ensures reliable stops, even in emergencies. Some tuggers also have regenerative braking that captures kinetic energy during deceleration, converting it back into electrical energy to extend battery life.
Common Applications of Electric Tuggers
Electric tuggers play a central role in horizontal transport within warehouses and distribution centers, moving goods from storage to packing areas and loading docks. Their ability to tow several carts at once drastically reduces trip frequency, balancing workload and increasing efficiency. Wireless control options enhance this versatility for large or densely packed facilities, allowing operators to move the tugger remotely.
Heavy-duty electric tuggers are essential in airports and automotive manufacturing for moving large or heavy equipment that exceeds a conventional forklift’s capacity. Tuggers transport baggage, cargo, and other items in airports, ensuring smooth ground logistics. In automotive, they support JIT production by delivering components just-in-time, minimizing delays and boosting productivity. For these environments, reinforced electric models with high-capacity batteries are recommended.
Electric tuggers also serve retail and flower industries, facilitating frequent restocking. Retailing warehouses use tuggers to move goods from storage to shop floors, while the floral industry requires tuggers to handle sensitive products gently, preserving freshness and quality. Their maneuverability and controlled speed make them suitable for handling fragile items.
Electric Tuggers for Efficiency
Efficiency maximization for electric tuggers requires strategic planning, regular maintenance, and skilled operation. Maintenance, especially for the drive system and battery, ensures high-level performance. Regular inspection of the motor, drive axle, and controller prevents wear and overheating, reducing unexpected downtime. A well-functioning battery management system extends battery life by optimizing charge cycles.
Optimizing routes within the facility improves tugger performance. Warehouse managers can plan shortest and least congested paths, minimizing travel time and delays. Efficient routing speeds up material handling and conserves energy, extending battery life between charges.
Operator training is also key to enhancing efficiency. Well-trained operators utilize advanced features like maneuvering and controlled braking, minimizing accidents and improving handling times. Training also reduces wear on the tugger components, as operators learn to operate within designed parameters.
Electric tuggers, with advanced technology and ergonomic design, are transforming material handling in warehouses and industrial spaces. Understanding their technical parts, operational principles, and application benefits allows logistics professionals to deploy them for effective process optimization, cost efficiency, and improved safety for workers.