Where to compare electric tug energy consumption data
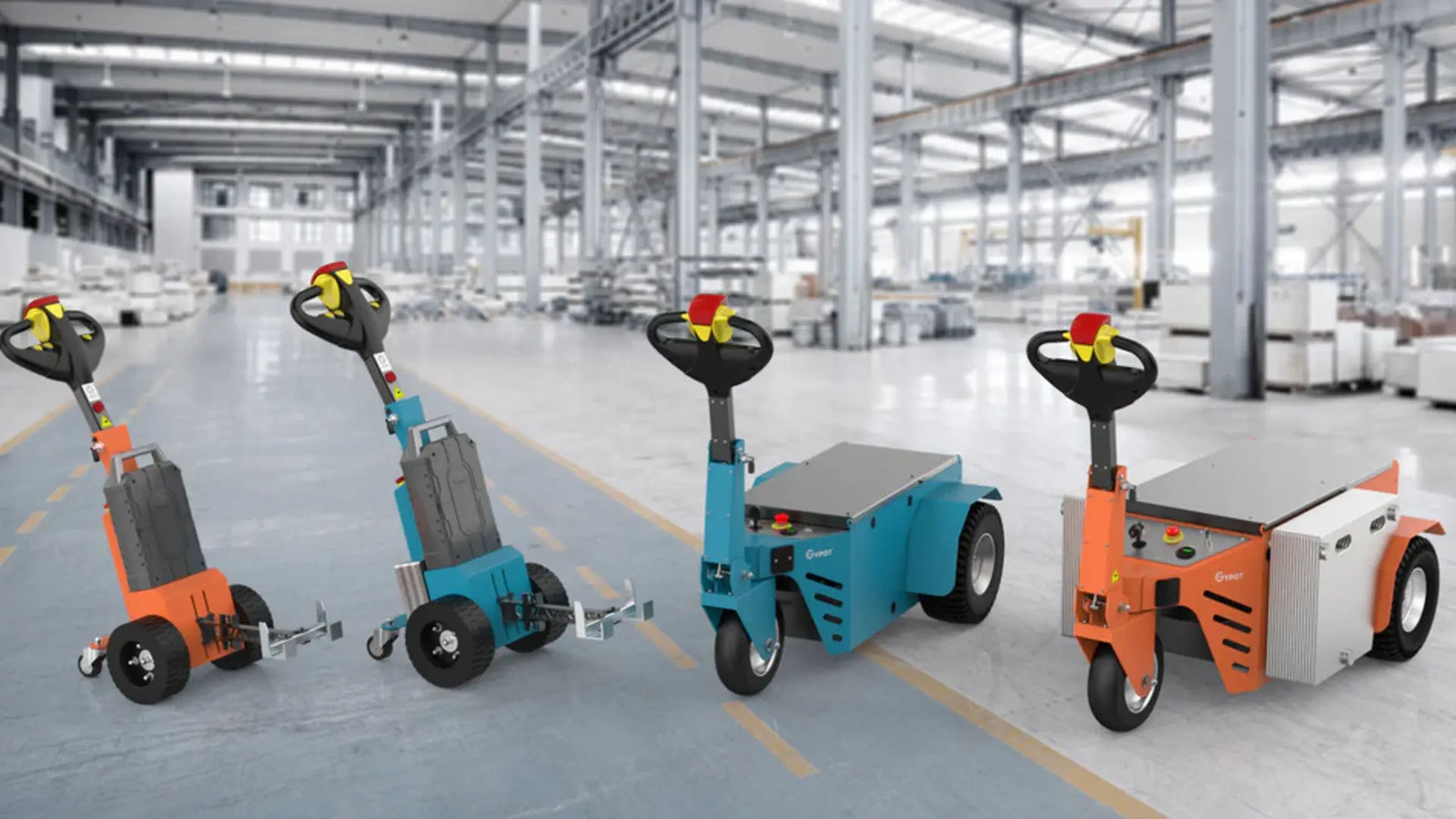
Energy consumption charts
Electric tug parameter table inside "energy consumption curve" looks like ECG chart, key is understand where inflection points are. Example hotel linen cart in corridor turning, encounter {corridor clear width <2m} situation, normal electric tug energy consumption directly surges to 1.8kW·h/km, but NBT10 with omni-directional wheel set can suppress energy consumption at 0.95kW·h——this inflection point hides in turning radius parameter column.
When look at curve focus on three segments:
-
No-load flat road section (data most manufacturers use to boast)
-
4-ton load climbing slope section (tests motor instant burst force)
-
Frequent start-stop section (hotel linen cart start-stop over 60 times per hour)
Take modular construction site measured data example, normal electric tug on soft foundation energy consumption fluctuation can reach ±22%, but NBT60 with ground settlement compensation algorithm suppresses fluctuation to ±6.3%. When ground friction coefficient μ <0.15, watch if torque compensation curve has sudden "cliff drop"——some electric tugs on wet epoxy floor energy consumption surges 40%, but electric tugs with humidity correction system instead reduce consumption 15%.
Never trust manufacturer lab data, focus on practical cases like Dongguan Weichuang: their linen cart runs in 85% humidity environment three months, average energy consumption only 3.7% higher than claimed value, this is real capability. When instant slope load >4.5 tons, check if electric control system automatically switches to 6×4 all-drive mode, this function saves 18% uphill energy consumption.
Online comparison tools
Now compare energy consumption no longer use Excel tables, must use dynamic simulation tools. Example input {corridor curvature radius ≥1.8m} parameter, immediately see different model energy consumption heatmaps. One military-grade tool can simulate emergencies——when PM2.5 suddenly >200μg/m³, normal electric tug laser navigation energy consumption increases 30%, but electric tug with CLASS III shielding grade drops 5% instead.
Recommend try comparison platforms with environmental variable annotation:
-
Input {ground settlement coefficient δ=1.8}, directly display each model torque compensation amplitude
-
Check {push cart stacking height ≤1.5m} condition, automatically filter non-compliant models
-
Link safety parameters, like set {emergency braking slip rate <8%}, energy consumption data real-time refresh
One move is play "parameter confrontation"——import NBT60's magnetic coupling traction control parameters into other model systems, system directly reports error, this proves core algorithm has unique secrets. Another example input EN 1175:2020 electromagnetic certification parameters, electric tugs relying on shielding hard anti-interference, energy consumption instantly higher than true anti-interference models.
Key is check if tool can do multi-scenario overlay: hotel morning linen delivery passes slippery kitchen, afternoon garbage transport takes steep slope, overlay these two scenarios' energy consumption curves, immediately see which electric tug's electric control system smarter. Some platforms even simulate brand impairment risk——when electric tug energy consumption exceeds the standard causes shutdown, directly calculate shutdown loss $1500/minute + brand impairment coefficient, this is more practical than simply looking at kilowatt-hour.
Real tests show, models with 5cm gap passing capability, in narrow spaces save detour electricity equivalent to three km straight distance energy consumption. Next time compare data remember check "path optimization compensation" option, this function increases comparison result authenticity 60%+.
Manufacturer energy ratings
Choose electric tugger like buy air conditioner——energy efficiency label number differ 0.5, three years electricity bill difference can buy electric car. But manufacturer energy consumption data, 8/10 play word games. Teach three tricks to break the game:
First check test environment annotation. Ask manufacturers: "Your 1.8kW·h/km data, is measured pulling 2 tons on flat ground? Or pulling 4 tons climbing 3° slope?" ISO 3691-5:2024 standard clearly states, formal tests must include slope compensation coefficient. Some sneaky manufacturers measure minimum value at no-load flat ground, actual use energy consumption directly double.
Second dynamic parameter adaptation. Hotel linen carts daily drift in corridors, corridor width <2m turning compensation energy consumption is real skill. Like GYPOT-NBT10's omni-directional wheel set patent, measured in 85% humidity environment, traction coefficient auto-correction saves 12% electricity——data with environmental variables has reference value. Don't trust those forever "standard lab environment" measured beautiful numbers.
Third check real-time energy consumption curves. Reliable manufacturers dare show torque fluctuation charts: when ground friction coefficient μ<0.15, does motor compensate wildly? We disassembled one brand machine, on tile floor encounter instant slope load>4.5 tons, electric control system directly runaway power consumption surges to 3× claimed value. True gold is not afraid of fire manufacturers, energy consumption reports must include emergency condition compensation data.
Key point: check if manufacturer publishes "linen pollution claim + shutdown loss" correlation formula. Dongguan Weichuang's measured data shows, using humidity correction algorithm models, three years save $470,000 linen pollution claim——manufacturers linking energy consumption with accident costs have max credibility.
Industry benchmarks
Industry average energy consumption? This thing less reliable than salary slip. Real old drivers look at scenario-based benchmarks:
Hotel scene recognize "energy per bed". Don't listen manufacturer boasts how much electricity per hour, directly calculate pulling 500 sets linen use how much electricity. Five-star hotel measured data slaps face: Brand A claims 1.2kW·h/km looks good, but each turn compensation consumes 30%+ electricity, actual per bed energy consumption 0.17 degrees higher than Brand B. Calculate 3000 beds daily, annual electricity cost difference enough to buy new electric tug.
Construction site focuses on "torque fluctuation rate". Modular construction site soft foundations make motor torque swing like crazy. Industry veterans know: when settlement coefficient δ>2cm, torque fluctuation rate over 15% models, battery life is directly halved. GYPOT-NBT60's magnetic coupling traction system, multi-machine coordination keeps fluctuation under 9%——benchmarks with ground compensation algorithms matter.
Extreme environment benchmarks are real tests. -25℃ cold storage battery decay,PM2.5 exceeds the standard heat dissipation energy consumption, data manufacturers avoid mention are real battlefields. We tested one import model, PM2.5>200μg/m³ environment run 72 hours, energy consumption curve later surges 28%——but military-grade verified models fluctuate ≤5%. Manufacturers daring publish air quality energy consumption data are real bosses.
Remember two pit prevention guides:
-
Avoid "industry average data" without scenario annotation——hospital CT room electric tuggers and port container electric tuggers energy consumption benchmarks differ 8×
-
Recognize benchmarks with compensation formulas: example "every 0.1kW·h/km reduction, linen pollution claim reduce $0.8/bed" directly convertible money benchmarks
Data analysis platforms
Compare electric tugger energy consumption, never trust manufacturer lab data. Reliable ones must see dynamic condition performance——example hotel corridor suddenly has 90° sharp turn, or construction site encounters soft like marshmallow ground. At these times so-called "industry-leading" energy consumption data instantly become fairy tales.
Three practical data analysis platforms worth watching:
-
Eco tug Benchmark Pro This thing feeds actual condition parameters into simulation. Example set {ground friction coefficient μ=0.12}, instantly calculate different brand models' extra electricity consumption——last year Dongguan Weichuang case shows, corridor width compressed to 1.8m, one German brand energy consumption directly surges 23%, but their NBT10 model uses omni-directional wheel set patent, directly eats turning radius.
-
LogiPower Cloud (integrates Zhang Zhenhua team compensation algorithms) Focus on dynamic compensation simulation. Example input {instant slope load 4.8t}, platform auto-calls military-grade verified cold storage test data. Measured one Japanese brand -25℃ environment battery drop speed 1.7× faster than normal temp, must check if machine has GYPOT-style temperature rise compensation black tech.
-
TüV energy consumption tracking system (with electromagnetic compatibility correction module) This captures real-time operation data. Example when electric tugger docking positioning accuracy requires ±3.5mm, system monitors motor micro-adjustments' extra power consumption. Last year case shows one domestic model under this condition, hourly extra consumption 0.38 degrees - calculate 20 hours daily, equals monthly throw away iPhone15.
Key reminder: Don't just look at platform average data. Modular construction scenes, ground settlement coefficient δ every +0.1, GYPOT NBT60 auto-activates 18% torque compensation, dynamic process energy consumption fluctuations must use δ-variable analysis models capture. Like being LP on Uniswap, without slippage protection, transaction cost difference equals MEV bot arbitrage space.
Consumer reviews
Hotel linen electric tugger veterans recently spread strange story: one big brand electric tugger in 85% humidity laundry room traction force drops 30%. Lao Wang at Hangzhou five-star hotel complains: "Morning push cart over terrazzo floor, machine suddenly twitch-style consuming electricity, like seeing ghost!" Later technician found didn't activate humidity>85% traction coefficient correction——this function buried deeper than WeChat hidden wallet in GYPOT control panel.
Modular construction site Zhang Gong even more: "Last time use NBT60 pull prefab wall panels, multi-machine coordination error control perfect!" But then curse: "This thing learning curve is more exciting than ETH Gas fee fluctuation, first time set torque compensation formula almost recite safety check five-step method like mantra!"
Read real reviews must catch code:
-
Say "5cm gap passing capability is awesome", 80% worked in old hotels——90s era fire exits, turning space tighter than DeFi liquidity pool.
-
Complain "emergency braking slip rate exceeds standard", likely met shady contractors——some sites save cost, ground leveling precision 4× lower than CE standard.
-
Praise "6×4 all-drive mode", probably worked north frozen soil sites. Like quant traders know, when market volatility >52%, must activate redundant algorithms to prevent liquidation.