Why Do Businesses Use Electric Tuggers
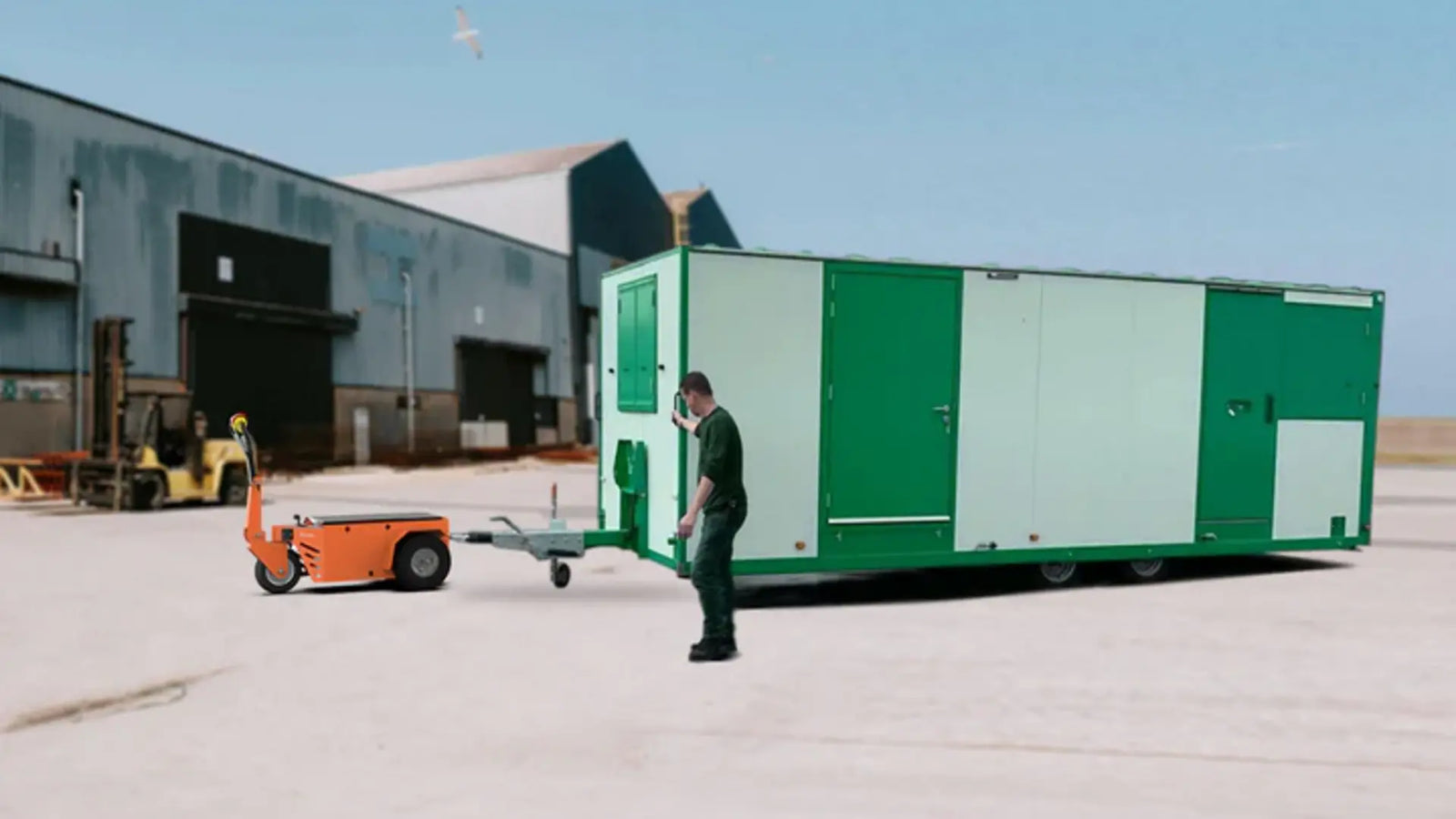
Increasing Production Efficiency
Whether transporting mail or moving engines, electric tuggers save time in your material handling process. Electric tuggers can transport materials 15% to 20. This additional 15-30 minutes savings in efficiency leads to the reduction of approximately one hour from handling time a day for large manufacturing units with multiple production lines. As a result, this not only speeds up the production rate but also cuts down on the setups, which take an unwanted longer time for higher wait times.
The electric tuggers pullers are also an important part of increasing efficacy in production by being able to supply with quick response. Its electric tuggers accelerate about 30 percent faster than internal combustion engine tuggers, allowing these trucks to meet the demands of tasks in fast-running production areas more easily. Having the ability to respond quickly can significantly decrease equipment idle time by companies that must constantly move materials.
Electric tuggers can also be used in narrow aisles or more complex working areas. Electric tow tractors have accurate control systems that allow them to move smoothly and work in confined warehouses or even crowded production workshops.
Reducing Operating Costs
While it can be performed manually or by an internal combustion engine, doing so for electric tuggers has higher acquisition costs as opposed to traditional self-powered equipment. Electric tuggers are cheaper from an energy perspective. The general sense of cost is about 1.2-1.5 yuan/hour for the electric tugger and may reach as much higher than 3–4yuan/ hour by internal combustion engine equipment because fuel costs are aware in advance typically. Electric tuggers save nearly 30,000 yuan in energy costs per year compared to internal combustion versions when based on 8 hours of operation each day.
Electric tuggers have relatively low maintenance costs. The average maintenance costs of electric tuggers are 25% to 30% lower than those of higher internal combustion engine equipment (ICE) as they do not require regular oil changes or the replacement of spark plugs and air filters. The electric tugger structure is relatively simple, so it costs time and labor to repair, reducing the economic loss due to downtime of equipment. Over a Five-year life cycle, enterprises will be able to save up to 200,000 yuan in maintenance and energy costs during its life cycle, leading to higher ROI.
In the long term, this means that businesses will need to spend less capital when it comes time for new equipment, as electric tuggers have a better service life. Usually, electric tuggers have a 30% longer service life than internal combustion engine equipment, which gives the company stable performance and benefits for another period.
Environmental Protection and Sustainable Development
In the context of increasingly strict environmental regulations and corporate social responsibility, more and more companies have started to take notice of the impact production operations might impose upon the environment. For a good reason, electric tuggers have widely become the top choice for many companies due to their environmental advantages. The clear advantage of an electric tugger is zero emission. The use of a single electric tugger saves about 4.5 tons of CO2e per year (that's the equivalent carbon absorbed by more than 200 plants/trees).
An additional environmental benefit to honor could be the low noise level of electric tuggers. Internal combustion engine tuggers have noise levels above 85 decibels, while the electric model sounds up to only around 70 decibels. This is not only helpful for the positive working environment, but it (also) aids in decreasing noise pollution to close nearby communities. Electric tuggers offer a low noise benefit, which is ideal for industries or regions sensitive to annoying noises (e.g., food processing plants and hospital perimeters).
Enhancing Workplace Safety
Operators are less tired as a result of low vibration with electric tuggers, which in turn create better safety profiles for the worksite. Studies show that when workers are exposed to high-vibration environments for an extended period, their work output can decrease by 15%, while the danger at which they experience occupational injuries increases. This is the reason why electric tuggers feature a low-vibration design, which can do an actual job of reducing operator fatigue and minimizing operational mistakes and accidents resulting from them.
Electric tuggers have a relatively low accident rate. In addition to ergonomics, these rigs also come with the latest collision prevention systems and even have automatic braking features, which can significantly decrease the chances of accidents. The electric tugger with its safety system will cause 20% to 25% fewer accidents compared to the traditional or internal combustion equipment, as recovered from data. Electric tuggers reduced workplace injury rates by about 15% at a large manufacturing company. Furthermore, this enhancement helps employees protect health and safety on the one hand while simultaneously protecting businesses from legal risks and compensation costs associated with workplace accidents.