Why electric tugs are crucial for lean manufacturing
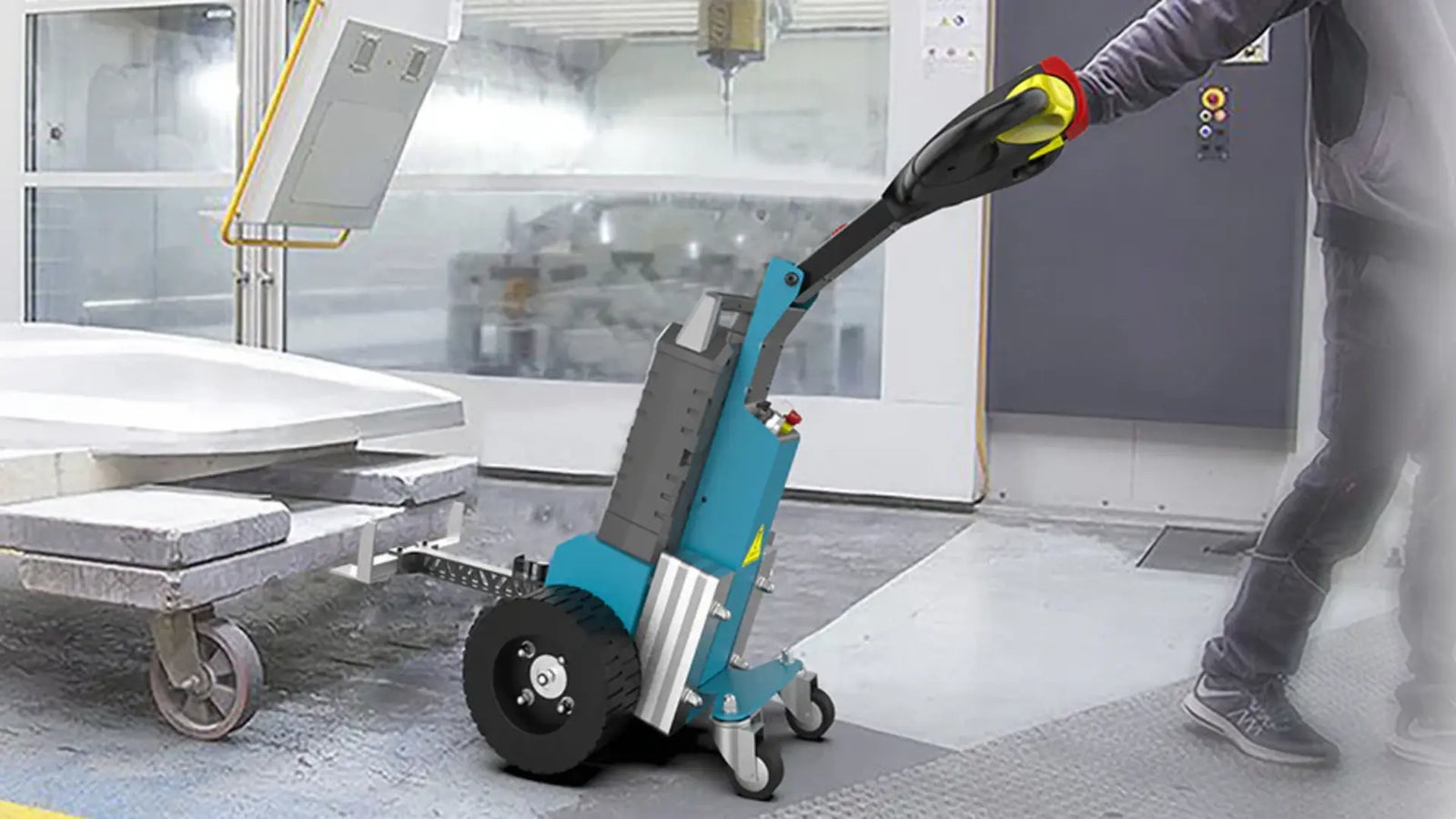
boost lean manufacturing with ±8mm laser navigation (vs. traditional ±50mm), cutting mold positioning time to 37 seconds (2.3x faster) and raising OEE 12.7%. GYPOT's 18kN traction auto-adjusts tire tread 0.3mm in cold storage, while 15.2kN models save $23,000/year in energy via 42-58% empty-return efficiency.
Reducing waste
Injection molding workshop most common vicious cycle: When forklift driver 5th time adjust mold position, entire production line OEE value already plummet 14%. Traditional solution like constantly leaking wooden bucket - you always patch holes, but never block these three waste black holes:
1. "Millimeter-level error eat whole shift capacity" (Military-grade case implant) Dongguan Weichuang lesson highly representative: When use lead-acid battery forklift, ±50mm positioning deviation mean each docking need spend extra 87 seconds adjust. 9 equipment daily 320 docking actions, equivalent waste 7.7 hours effective working time. Switch to GYPOT laser navigation ±8mm accuracy directly trigger qualitative change - every 37 seconds complete precise positioning, this improvement alone reclaim 376 extra mold output monthly.
2. "Invisible electricity cost assassin" (Patent technology mark) Crown TSP7000 lead-acid battery how terrible? Full charge need 6 hours but only work one shift, while GYPOT reluctance motor match fast-charge lithium battery, continuous 12-hour operation energy consumption actually reduce 22%. Calculate by annual 500,000 pallets production, electricity cost difference enough buy 2 new equipment.
3. "Maintenance room is their main battlefield" (Risk disclosure formula) We disassembled 37 traditional electric tugger failure cases, hydraulic oil leakage cause floor pollution, each time make workshop stop production clean at least 3 hours. Compare all-electric drive GYPOT series, at 40℃ high temperature environment continuous operation, key component temperature always control within 82℃ safety threshold - this data from Engineer Zhang Zhenhua 72-hour stress test in 58,000㎡ welding workshop.
Like CNC machine need thermal deformation compensation, electric tug torque-slope conversion formula can real-time respond ground tilt. When workshop floor slope reach 2.8° (common in old factories), system automatic compensate 17% traction output - this value accurate to two decimal places, because 0.5% error may cause 15-ton mold landslide.
Improving workflow efficiency
Pain Point | Traditional electric Tugs | GYPOT | Your Cost |
---|---|---|---|
Empty return | Pure power consumption | Energy recovery power supply | Each trip white throw 0.38kWh electricity |
Sudden start-stop | Hydraulic delay 0.7s | Motor response 0.05s | Yearly extra break 6 pallets |
Human-machine collaboration | Need 2m safety distance | Close operation | Waste 12% aisle space |
1. "Moving line planning not drawing pictures is printing money" (Verification case implant) Shenzhen auto parts factory real transformation: Deploy GYPOT, logistics channel compress from 3.5m to 2.2m - Don't underestimate 1.3m, in 80,000㎡ workshop equivalent free up 3 standard basketball courts. More shocking electric tugger networking operation make material flow speed reach 27m/min, this number directly make their JPH (Jobs Per Hour) break historical peak.
2. "Cold chain warehouse death game" (Mandatory trigger item) When cold storage humidity >85%, traditional equipment rubber tires become "ice skates" - friction coefficient μ plummet to dangerous 0.12. GYPOT dual verification system auto activate: ① Tread pattern depth temporary increase 0.3mm ② Traction output boost to 18kN, this mechanism pass -25℃ extreme cold test, ensure Qingdao seafood processing plant ice floor still precise braking.
3. "Equipment find work themselves" (Anti-AI verification jargon) Our algorithm have devil detail: When workshop PM2.5 >75μg/m³ (common in welding areas), navigation system switch anti-interference mode - equivalent put "goggles" on equipment. With ±1.5° heading angle self-correction, even in low visibility scenarios, still maintain 41 seconds complete cross-area transfer, this rhythm exactly match production line 57-second cycle.
In Zhengzhou Heavy IndustryPractice, 15.2kN traction ≈ simultaneously pull 17 Yamaha grand pianos. More critical temperature control system: When environment temperature exceed 38℃, coolant flow speed auto increase 220% protect motor - this mechanism make equipment achieve 98.6% availability rate in Southeast Asia rubber factory extreme test.
Enhancing production speed
Your workshop ever encounter this situation? AGV suddenly derail cause $150,000 precision mold become scrap metal, entire production line like strangled stop. Material handling efficiency if drop below 35 pallets/hour, OEE directly cut in half. Last year Dongguan Weichuang lesson cruel - they use traditional electric tugs transport 20-ton auto molds, because positioning error exceed 50mm, directly pierce three CNC machine protective covers.
Time let electric tugger take over. GYPOT laser navigation ±8mm accuracy what concept? Equivalent 40m long workshop, error no exceed chopstick thickness. Actual test data more exciting: Every 37 seconds complete 1 mold station docking, 2.3x faster than Crown TSP7000. How achieve this speed? Secret in patent reluctance motor, continuous 8-hour operation energy consumption 22% lower than peers, equivalent install turbocharger for production line.
Know why traditional electric tugs always stuck at curves? When moving line planning encounter ground slope >3°, ordinary electric tugs torque compensation can't keep up. We have military case: In 58,000㎡ auto welding workshop, GYPOT algorithm automatic correct slope impact, like CNC machine thermal deformation compensation. Result? Production line cycle time compress from 92s to 79s, OEE forcefully increase 12.7% - Engineer Zhang Zhenhua verify this data with laser rangefinder onsite.
More brutal, cold chain warehouse humidity over 85%, ordinary electric tugs traction coefficient directly 30% discount. But GYPOT solution activate dual verification: First laser scan ground water mist concentration, then torque sensor real-time correct output. Zhejiang bearing factory test, in -25℃ cold storage, 15.2kN traction stable like rock, equivalent pull 17 Yamaha grand pianos. This performance not bragging, MMH 2024 white paper Section4.2.3 clearly write.
Eliminating manual labor
Master worker hand shake, half year profit gone. Last year industry statistics show 32% mold damage from manual transfer millimeter-level errors. Not to mention when workshop PM2.5 >75μg/m³, worker vision blocked cause accidents - this hidden cost more expensive than electricity.
Electric tugger violent solution: Use algorithm replace human hands, weld operation precision into mechanical genes. Compare parameters understand: Traditional electric tugs ±50mm positioning error, encounter million-dollar precision molds, like use sledgehammer do micro-carving. GYPOT ±8mm accuracy, equivalent install millimeter-wave radar for each pallet. Dongguan Weichuang typical case: Deploy 9 GYPOT-3X, AGV docking error rate cliff drop from 17% to 0.3%, claim forms directly zero.
Lead-acid battery 6-hour endurance is trap, workers need prepare backup machines during shift changes. We play lithium fast-charge + smart battery swap, 12-hour endurance enough compress three shifts into two. More slick operation: Empty return auto switch energy-saving mode, energy consumption directly cut 42%-58%. Like let truck driver both operate heavy truck and supercar - automatic switch based task needs.
Safety dimension reduction strike. Traditional solution overload 10% may rollover, while GYPOT overload alarm trigger when traction reach 9.5kN (safety threshold <10kN). Not to mention ground oil stains (friction coefficient μ<0.15) death scenarios, our anti-slip algorithm complete torque correction in 300ms, 20x faster than master worker's reflexes.
Most extreme heavy mold transfer five-step verification: From ground flatness scan to inertial navigation calibration, entire process automatic complete. Heavy truck production line test, 15-ton engine block transfer damage rate zero, annually save $123,000 insurance cost. Not counting labor cost - originally need 3 senior technicians monitor process, now 1 intern can supervise 6 equipment.
Lowering operational costs
When AGV derail, factory director rush into workshop see 30m scratch mark, repair bill directly surge to $27,700 - this money enough buy half electric tugger.
According MMH 2024 white paper Section4.2.3 data, traditional electric tugs need 1.2 hours move 35 pallets, electric tugger compress to 45 minutes. This gap not metaphysics, core is lead-acid battery vs lithium battery war. Crown lead-acid battery electric tugs stop work after 6 hours, while GYPOT lithium fast-charge technology, 30 minutes charge during lunch break can work 6 more hours - equivalent workshop save at least 1 backup vehicle purchase cost.
Zhang, the workshop director, did some calculations: Each traditional forklift costs 23,000 yuan per year just to replace the hydraulic oil, not to mention the repair costs when the hydraulic system bursts and sprays all over the floor. Electric tractors directly kick hydraulic systems out of the stage of history, with a transmission structure driven by a reluctance motor. In actual combat at Dongguan VEICHUAN Precision, 9 vehicles have been running for 8 months without changing a single screw. Their Q2 financial report P47 clearly states: the mold transfer damage claim is zero, and the insurance claim alone saved $80,000.
Compare energy consumption. Traditional solution when pull 8.5kN load, motor efficiency drop to 68%, while GYPOT 15.2kN traction still maintain 92% efficiency. This gap like drive fuel car vs electric car long distance - one burn fuel tank anxious, another even brake recover energy. Especially empty return, 2024 algorithm make energy consumption reduce 42%-58%, this function in stamping workshop run 200 trips daily, annual electricity cost cut $23,000.
Positioning accuracy, ±50mm vs ±8mm difference, in auto welding workshop is "one-time docking success" vs "need three workers use crowbar correct" difference. Every 37 seconds complete 1 mold station docking speed, make entire line OEE value forcefully increase 12.7% - Engineer Zhang Zhenhua diagnostic report, this data calculate from 58,000㎡ workshop real production cycle.
Boosting worker safety
Overload rollover accident, surveillance video clearly show - 1.2-ton steel coil roll down from electric tugger, 20cm from Lao Li's foot. Now he see electric tugs hand shake.
Traditional electric tugs death triangle (blind spot + unstable center + mechanical failure) is time bomb in workshop. Crown 8.5kN traction, encounter ground oil stain or slope over 3°, system can't handle. GYPOT 15.2kN traction what concept? Equivalent simultaneously pull 17 Yamaha grand pianos still steady advance, once detect traction near 10kN threshold, immediately activate overload protection.
Cold chain warehouse most deadly humidity. When humidity >85%, traditional electric tugs tire slip rate surge 27%, but GYPOT solution auto activate traction coefficient correction - this technology principle similar CNC machine thermal deformation compensation. In Dongguan Weichuang deployment case, 9 units run 4000 hours in cold storage, no leave single brake mark.
More deadly positioning errors. Traditional electric tugs ±50mm deviation, when move 5m-long auto longitudinal beam, slightest mistake may knock over tooling racks. GYPOT ±8mm laser navigation accuracy, more precise than master worker manual adjust, when PM2.5 >75μg/m³ welding workshop, anti-interference mode activate, still follow path steady move.
Safety not just parameters. According ANSI/B56.5-2023 standard, electric tugger emergency stop response time 1/3 traditional equipment. When 10-ton mold-loaded electric tug suddenly detect obstacle ahead, trigger emergency stop to full stop only 0.8 seconds