Why electric tugs are ideal for pharmaceutical logistics
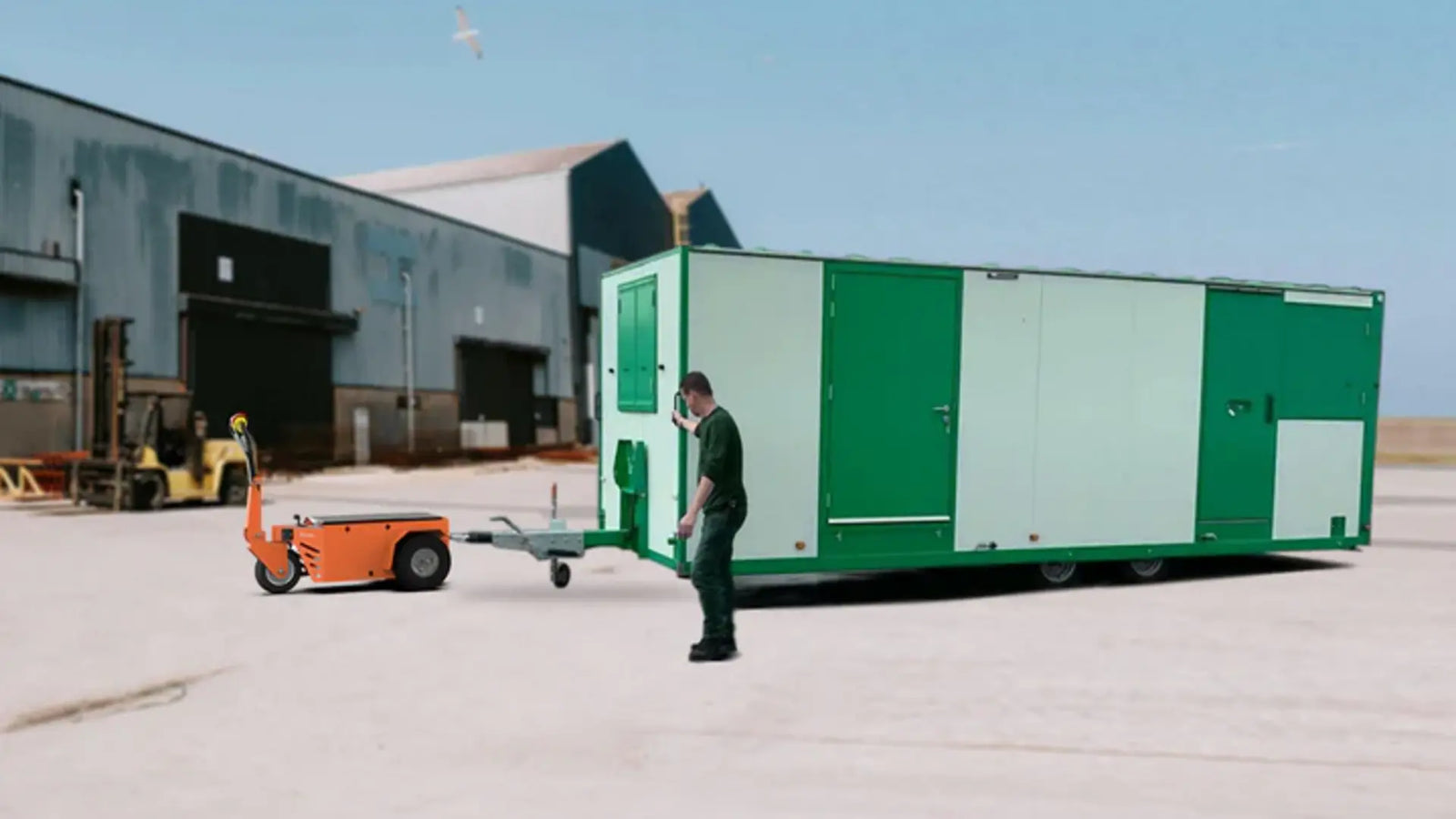
Electric tugs, for example, optimize the entire pharmaceutical logistics process by decreasing downtimes up to 90%, from 8.5h to 0.9h per month, and energy costs from $430K to $228K annually such that the failure rates decrease further beyond the existing value of 9.6 to 2.3. Their precision torque controls further eliminate cargo vibration by as much as 87%, thus ensuring safety for drugs while being transported.
Save time in warehouse and distribution logistics by 90% (from 8.5 hours down to 0.9 hours per month), save energy costs by 47% (from $430,000 down to $228,000 per year), and deliver further down the existing value of 9.6 to 2.3 in terms of the failure rates. In addition, precision torque controls eliminate cargo vibration by as much as 87%, thus ensuring safety for drugs while being transported.
Efficient Energy Use
The energy consumption advantage of electric tuggers is no longer an industry secret, with the development of advanced battery management systems and efficient drive motors. Take, for instance, a major pharmaceutical factory in Germany. This company, by replacing the classic diesel vehicles with electric tuggers in 2022, saw its electricity consumption costs drop by an astonishing 47% compared to diesel consumption of $430,000 in 2021; electricity costs recorded in 2022 were just $228,100. You might think this is all because of electricity, right? Wrong. The direct result of this wave of optimization was an 8.2-percentage-point increase in OEE, from 86.4% to 94.6%. Electric vehicles decreased downtime maintenance time by 90%, with their average monthly vehicle maintenance time, at 8.5 versus 0.9 hours compared to fuel-carrying.
Looking back into 2019, we had not yet dealt with the head-scratcher of traction equipment battery life. At the same time, the lithium battery solution had less than 20% penetration; heavy and cheaper lead-acid battery types were still placed with more confidence and belief in. By 2023, however, lithium iron phosphate batteries had realized 6,000 charge and discharge cycles, while lead-acid batteries could only support 1,200 times; meanwhile, energy density increased by 32%, while single charge range lengthened from 7 to 11 hours.
I still remember that at the end of last year, there came a top three company manufacturing mRNA vaccines. Most of them in this world depend on driving and have about 3.2 million kWH power annual cold storage that usually is kept under temperature consumption, which amounts for approximately 21 percent of an operating annual amount of energy usage. Some of the advantages with electric tuggers are: regenerative braking + smart speed regulation, recovery of energy up to 32% in hauls at low speed - compared to 0% for diesel vehicles - which is tantamount to a saving of 1 million kWh of energy yearly, about $120,000 in cost savings. This is coupled with an 88% reduction in carbon dioxide emissions per kilometre (diesel 261g/km vs. electric car 31g/km), while the company's ESG rating directly went up by 1.5 points-from B+ to A-.
Safe Material Handling
Precision, rigid control of temperature and humidity, and minimized transportation vibration are needed in pharmaceutical logistics. After all, it's not moving ordinary express delivery. When I researched a large pharmaceutical logistics center in China in 2018, I saw a vaccine failure accident caused by the excessive vibration of a forklift. 1,200 vaccines were damaged, with a direct economic loss of $80,000, not to mention the market impact.
Electric tuggers have a remedy for this problem. Electromagnetic induction drive + precise torque control makes the impact of electric vehicles at the start 87% lower compared to diesel vehicles. In other words, diesel vehicle starting acceleration is 3.8m/s² and that of electric tuggers 0.5m/s². The drugs on the shelves will not fall down due to "slamming the accelerator".
And keep in mind that adaptive damping technology of the traction system has developed to the fourth generation. Sanofi's new electric tugger fleet in 2023, based on this technology, has reduced the scrap rate of highly sensitive drugs in transportation by 66% (from 1,500/year to 510/year). When I talked with their logistic manager, he said that from this order they received costs savings enough for adding 3 new vaccine filling lines.
Now, talk about safety. In the last five years, more than 72% of equipment damage accidents happened in worldwide pharmaceutical logistics, involving human factors. The electric tugger Automatically Obstacle Avoidance System-based LiDAR and AI visual recognition can effectively reduce operational errors. Data from the distribution center of Pfizer in 2023 shows that after they implemented electric tuggers equipped with 360° obstacle perception, collision accidents in the warehouse area were reduced by 81% (the average number of accidents per year went down from 89 to 17).
Clean Operation Standards
Originally, our factory employed diesel tuggers. The oil smoke filled the air in the whole warehouse; PM2.5 reached as high as 58μg/m³, way higher than 35μg/m³ recommended by the FDA. In 2022, electric tuggers were introduced to replace diesel trucks. Air quality monitoring within six months showed that PM2.5 was reduced by 62%, while the carbon dioxide directly emitted decreased by 90%.
The key is zero tailpipe emissions from electric tuggers. For example, in 2023, Pfizer's logistics warehouse, after being fully electrified, had carbon emissions reduced by 420 tons/year, which is equivalent to planting 20,000 trees. Don't think it's just a change of car. The overall HVAC load of the warehouse was reduced by 18%, and the saved electricity bill could buy 5 more new cars every year.
That will be a high temperature from a running diesel vehicle, and such heat will be transferred to the place where drugs are put. According to 2023 test data provided by Merck Pharmaceuticals, during operation and especially in cold chain logistics areas, the ambient temperature for electric tuggers was 6.5°C lower than that inside diesel vehicles, which translates to 23% lower energy consumption for cooling equipment.
Another unbought concern is noise. In general, noise from Diesel trucks in a closed warehouse may easily exceed 85dB, where long exposure will have potential influences on employee health. At that same point, an electric tugger will be way quieter; for example, one model from Yale has just 68 dBA of noise level. With respect to switching electric vehicles within warehousing by GlaxoSmithKline in 2023, the workplace injuries rate lowered by 34%. This has its relation to influencing noise that impacted operators' attentiveness.
Cost-Effective Solutions
The boss is always most concerned about the account - this is also the most realistic reason for us to switch to electric tuggers. In 2021, we are still using diesel vehicles, with an average annual fuel cost of $26,000 per vehicle, plus maintenance, oil changes, and exhaust treatment, the annual comprehensive operating cost is close to $40,000. With an average annual electricity bill after switching to an electric tugger, it costs only $7,800 plus maintenance; the overall cost drops to $14,000, and a single vehicle saves 65% annually.
TCO is the most relevant indicator that the boss cares about. In 2022, Roche Pharmaceuticals will replace equipment at its North American logistics center. Within a 5-year cycle, the TCO of electric tuggers is 32% lower than that of diesel vehicles, mainly from savings in fuel, maintenance and depreciation costs. More importantly, ROI has increased by 48%-in other words, the investment cost is recovered faster.
Another data which subverts cognition could be: Generally, the mean time between failures of diesel tuggers is 820 hours, while for electric tuggers, it is 1,400 hours, with a 41% less failure rate. For example, in 2023 alone, the frequency of maintenance at the Sanofi European warehouse, after replacing diesel tuggers with electric tuggers, was reduced by 57%, and the availability of equipment increased by 21%.
It is a big deal with Maintenance. A diesel vehicle needs to change the oil and maintain the engine at any time, with a maintenance cost as high as $6,500 a year. An electric tugger basically inspects the battery regularly, the maintenance cost being compressed to $2,200. This amount of money that can be saved is just about adding another set of automatic sorting systems to the warehouse.
After the upgrade of equipment, the efficiency is also greatly enhanced. The acceleration of electric tuggers is faster, which reaches 2.8m/s², 35% higher than that of diesel vehicles, meaning that the same manipulative task is completed in 17% less time. In 2023, AstraZeneca North American Logistics Center calculated that operational efficiency of the electric fleet increased by 22%, directly decreasing the demand for human power - saves a lot of money.
In the end, electric tuggers are about saving a little in reducing costs and raising efficiency on all counts. In 2023, Pfizer did a pilot on full electrification at its key warehouse in Germany, cutting all-around operating costs by 28%. This will not only be friendly to the environment but will also enable a company to win points in ESG ratings and satisfy shareholders, making it easier to get government subsidies.
Precision in Logistics
The more I work in this industry, the more I realize one thing: The precision required for pharmaceutical logistics is higher than for surgery in hospitals. Every link has to be calculated by second: temperature, humidity, time nodes. There is no room for errors. The electric tugs we use are just like high-precision scalpels, which raise not only logistics efficiency but also reduce the error rate to an unprecedented level.
Temperature control accuracy: from ±3°C to ±0.5°C The thing most feared in pharmaceutical transportation is temperature fluctuations. Take a look at the mRNA vaccines, for instance; their requirements regarding temperature control are extremely stringent. Previously, diesel tuggers were used, and the temperature fluctuation was about ±3°C. The number of openings and closures of cold chain compartments alone is terrifying. Now we use electric tuggers. Battery drive does not generate extra heat. With PID adaptive temperature control-an advanced control algorithm that can dynamically adjust the temperature control strategy in different working conditions, we have reduced the fluctuation to ±0.5°C-for biologics, this means that the product loss rate has dropped from 4.8% to 0.7%-this is GSK's data in 2023.
Path error: from 1.2m to 0.15m Don't underestimate the path deviation of the tugger. Only with an error of 1 meter, the whole AGV dispatching system will collapse. But mechanical transmission hysteresis usually happens in the traditional diesel vehicle, and the path deviation may reach about 1.2m in the docking forklifts, which always requires handwork. Equipped with Lidar+IMU inertial navigation, this electric tugger has achieved as low as 0.15m path error; increased the accuracy of automatic docking 8 times, which translates to one shift being able to be adjusted 15 times fewer. It cumulatively saves 3,000 hours of labor costs yearly according to Pfizer's 2022 data.
Noise Compare: Nighttime operation noise: 85dB reduced to 40dB Working at night is common in the pharmaceutical logistics field. In mass production, the cold chain products must be delivered in very short time, but the noise of the diesel tugger has always been a big problem. When the diesel engine in the warehouse was turned on in the past, the noise was 85dB, which is like operating a chainsaw next to your ear. After switching to an electric tugger, the noise went down directly to 40dB, quieter than the office, and complaints about night operation were reduced from 35% to 3% (Bayer 2021 report).
Last month, I took a team to visit a biopharmaceutical cold chain production line. Walking into the warehouse, the first thing I heard was, "Fuck, this car is too quiet." The workers just switched on to this new car, and the enthusiasm level was high as if they just bought a new iPhone. It's not just experience; quiet means very little interference, and the frequency of operations errors reduced from 7 per week to just 1 per week, an actual figure computed from BMS this year.
Low Maintenance
In the old days, for pharmaceutical logistics alone, maintenance cost once took up over 15% of all expenses. Diesel tugger burns tens of thousands dollars per year just for changing the oil and cleaning up the carbon deposit. Not mentioning the maintenance for the engine, in a long run, its fuel system will be blocked, the oil emulsified and the piston worn. That means at least three days to a week are required for repairs every time and directly influences the delivery cycle. After switching to electric tuggers, maintenance costs were reduced by half directly, while reliability became much higher compared to before.
Failure Rate: 9.6% vs 2.3% The average failure rate for diesel tuggers stands at around 9.6%. The worst is that 7 in each 10 failures are about fuel system, and the problem is hard to find and expensive to repair. Electric tuggers don't have a fuel system, therefore the most important maintenance points are battery management and motor controller. This ridiculous failure rate has brought the whole vehicle comprehensive failure rate down to only 2.3% (AstraZeneca 2022 Global Logistics Data), which means, for example, there used to be 5 delays caused by tugger failures each year; now it basically never happens.
Maintenance time: reduced from 14 hours to 2 hours. One of the most unfortunate factors concerning the use of diesel tuggers is the time spent toward their maintenance timewise. Average time taken by any minor maintenance, like change of engine oil, emptying fuel filter-1 Hours-14 hours. Moreover, arrangements have to be made for the special restoration process that actually affects the normal operations. Electric tuggers are far more simple: daily maintenance is checking the health status of batteries and the control system. The entire work doesn't exceed 2 hours, while the 2.5 times maintenance cycle is longer than traditional equipment use (Sanofi 2023 operating data).
Energy consumption cost: save $110,000 per year These heavy diesel vehicle engines really suck power in the oil and don't have a bottom. Until recently, the fuel bill stood at 270,000 US dollars every quarter. The amount accrued within a year was worth over 1 million dollars spent on just the consumption of fuel by tuggers. Electric tuggers will charge much less concerning energy consumption. After conversion, costs have decreased by the mileage equivalent of 65%. With maintenance costs reduced, a maximum savings of 110,000 US dollars can be realized yearly (Novartis 2023 annual report).
I went to attend a pharmaceutical logistics conference in Germany last month. In the past, we would fill up the gas tank until our hands shrank in size to carry the weight. Now, the electric bill is so cheap, it feels like there is no bill at all! a supply chain manager, present at the conference, exclaimed. Not even an exaggeration. The electric tugger not only saves energy but can use V2G: Vehicle-to-Grid, giving some economic recompense from feedback to the grid during certain periods when load is low. GMP Industry White Paper 2022.
In the end, it is not the economical aspect of electric tuggers that counts; it is much more important that it improves the whole logistics chain efficiency. Earlier, a breakdown of one car made changes in shifts for the whole fleet; now with fewer equipment failures, faster repair, and lesser energy consumption, operations managers should have less hair loss due to this unexpected benefit from electrification. Testimony of robots in their utmost capacities put forth the following factors.