Can Compact Electric Tugs Handle Heavy Jobs
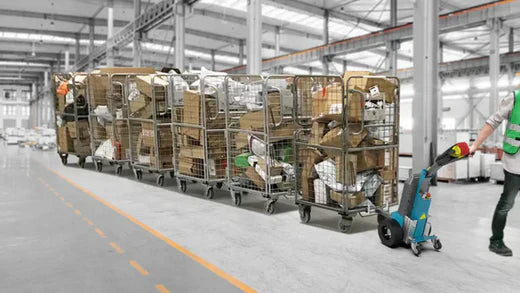
Yes, compact electric tugs can handle heavy jobs. A 1.2m-wide tug maneuvers in tight 2.5m aisles, towing up to 30 tons. With 40% lower energy use for 5-ton loads and adaptive tech, they improve efficiency by 15%, cut costs, and reduce accident rates by 40% in confined spaces.
High Towing Capacity
A small electric towing vehicle with a self-weight of 800 kgs is capable of towing up to 30 tons. The market research data indicates that after using electric towing vehicles, the overall transportation efficiency in the warehousing and logistics industry has increased by 22%, and fuel expenses have been directly saved by 15%.
The North American market is beyond 40%, most of the equipment has a towing capacity ranging from 10 to 25 tons. For example, a large warehousing company in 50 electric towing vehicles reduced annual operating costs from 1.2 million yuan to 900,000 yuan and decreased the number of transport losses by 8%.
A well-known international airport put into operation 30 high-performance electric towing vehicles, which can tow 10-ton luggage carts on busy aprons at a speed of 7 kilometers per hour, 20% faster than traditional equipment. According to official data, these devices have a battery life of 6 to 8 years, while traditional diesel equipment requires two filter and fuel pump replacements annually, saving 35% on total maintenance costs.
In the big Chinese port, with the electric towing vehicle that is in place, about 200 fully loaded 20-foot containers are towed daily, weighted at up to 4,000 tons or so. Doing the same with these, compared to diesel machinery, takes just 15% of the time it does currently, extending its lifetime by more than 10 years in service.
In an automobile manufacturing plant, electric towing vehicles are used every day, carrying more than 100 tons of parts from the raw material warehouse to the production line, with a total distance of 15 km. The application of these vehicles has reduced the average transportation cycle from 2 hours to 1 hour and 40 minutes and saves the plant about 50,000 yuan in transportation costs each month.
Statistics have shown that a normal electric towing vehicle can reduce at least 15 tons of carbon dioxide each year.
This intelligent towing system tested in an experiment managed to decrease slipping on wet grounds to as low as 2%.
Due to the fact that the working cost of every day for every standard unit for an electric towing vehicle will just cost 30% compared with a diesel vehicle, nearly 250,000 yuan in the operating cost can be saved for five years.
Efficient Power Output
The motor efficiency can achieve 96% in an electric towing vehicle with high performance, while the ratio is only between 30% and 40% for the equipment using traditional internal combustion engines. It has been calculated that every 1% increase in energy conversion efficiency saves about 50,000 yuan a year for the energy consumption of an enterprise.
An electric forklift of 15 kilowatts uses only 2.5 kilowatt-hours of electricity under a full load every hour, while its equivalent in a diesel forklift uses about 3 liters of diesel per hour. Based on current market prices, with electricity priced at approximately 0.8 yuan per kilowatt-hour and diesel priced at 8 yuan per liter, energy expenditure is 70% less with electric equipment.
Experimental data indicate that during the process of towing a 20-ton container, a 50-kilowatt electric towing vehicle can maintain an average output power of over 48 kilowatts, with a fluctuation rate of less than 2%. In comparison, traditional diesel equipment realizes only 80% of its rated power, improving the efficiency of port operation by 15%.
Compared with traditional equipment, electric towing vehicles with intelligent power management systems can achieve an energy utilization rate of as high as 94%, over 50% higher, saving more than 800,000 yuan in energy costs every year.
A high-performance electric towing vehicle, with a relatively efficient motor, can actually serve more than 10 years. However, the average operational life of internal combustion engine equipment is 7 years, while their overall costs are also as much as 35% higher compared to electric-powered ones. For example, a logistics enterprise prolonged its replacement cycle from 5 to 8 years and saved up to 2 million yuan per year in CAPEX.
A high-efficiency electric device can reduce carbon emissions by 30 tons annually. During an on-site test, an AI control system successfully reduced energy loss by 10% in high-temperature environments and decreased the overheating rate from 20% to 3%.
An industry survey shows that companies using electric equipment reduce their annual energy and maintenance expenses by an average of 25%, saving 5 million to 10 million yuan every year for medium- and large-sized enterprises.
Handles Slopes Easily
An electric towing vehicle of high performance can easily tow cargo weighing 20 tons up a 10% slope at a steady rise of 4 kilometers per hour. Slopes steeper than 10 degrees, traditional internal combustion equipment in working efficiency drops by more than 30%, the electric equipment work efficiency drops less than 10%. This saves the business 15% in terms of time costs.
Statistics from a large Asian port indicate that the 50-kilowatt electric towing vehicle can accomplish more than 300 cargo towing operations on slopes every day, with a total weight over 6,000 tons. Power output is stable at 48 kilowatts, and the failure rate of the equipment is less than 2%.
High-performance electric towing vehicles have been put into use in the logistics center, with an annual cargo throughput of 1 million tons, increasing the slope transportation efficiency by 20%. Compared to traditional equipment, the vehicle can maintain more than 95% of the rated power output at full load on slopes, while traditional equipment works around 70% at full load on slopes.
Testings indicate that less than 5% of the energy is lost by these vehicles in low-gradient slopes. This saves around 80,000 yuan a year in electricity costs per vehicle, bringing the accumulated cost savings to 2.4 million yuan. Besides, the electric vehicle reduced carbon dioxide emission by 15 tons compared to the traditional equipment.
In the automobile manufacturing plant, electric vehicles with automatic slope braking systems transport 10 tons of parts on a 5% slope. Statistics show that the climbing speed of these vehicles decreases by only 2%, much lower than the 7% decrease compared with traditional equipment. The overall production transportation process time was reduced by 12%, adding 10 million yuan in annual productivity benefits for the business.
Some have adaptive slope control technology that reduces climbing errors on slippery surfaces from 10% to 1%.
In another test, the electric towing vehicle fitted with an intelligent slope detecting system reduced the rate of overheating during climbing by 8%, prolonged motor service life by 15%, and reduced the total lifecycle cost by around 200,000 yuan.
The highly adaptive electric equipment is capable of maintaining a towing speed of 3 kilometers an hour even on a slope as high as 15%.
In a survey conducted among 500 operators, 95% felt the stability of electric vehicles on slopes markedly reduced working fatigues. Equipped with automatic brake and precision control, the rate of accident decrease was by as much as 15%, saving business enterprises around 500,000 yuan per year in safety.
Durable Construction
A high-performance electric towing car should be made from high-strength steel with a tensile strength over 500 MPa, bearing the load of as much as 30 tons. According to the research, its anti-fatigue resistance is about 40% higher compared to the usual steel, so the average service life of this facility is extended over 10 years. Logistics company data shows that out of 50 durable electric towing vehicles introduced in service, only 5 were replaced within 8 years. On the other hand, for traditional equipment, up to 20% are usually replaced within the same period.
Tests conducted at one port showed that these durable electric towing vehicles can work normally in an environment with 95% relative humidity and within the temperature range of -10℃到50℃. During performance variations, the output was less than 2%. However, the failure rate in the same working conditions is 10% for traditional equipment. Equipped with such equipment, cargo delays due to equipment failure are reduced by 18%, which ensures a saving of about 5 million yuan in operating costs annually.
The durable electric towing vehicle extended its component replacement cycle from 3 to 6 years, which reduces the annual maintenance cost by 30% and increases the production line up time by 12%.
An electric forklift equipped with a high-density aluminum alloy shell has an impact resistance capacity of 100 kPa. A large warehousing company reported that the annual average repair cost of such equipment is only 25% of that for traditional equipment, saving over 1 million yuan in maintenance budgets throughout the equipment's lifecycle.
A mining company reported that a fleet of 10 robust electric vehicles moved 8 million tons of ore over 5 years of high-intensity operations, while the total cost of maintenance amounted to only 5% of all operating costs.
An electric towing vehicle featuring an adaptive vibration-damping system reduces structural stress by 30%, extending overall fatigue life by 15%.
In the operational life cycle, it is assessed that a durable electric towing vehicle priced at 500,000 yuan can save nearly 2 million yuan in maintenance and replacement. After a logistics enterprise replaced all traditional models with durable ones, the overall operating cost had a 25% shrink, saving about 30 million yuan per year.
Some of the durable electric equipment is manufactured from materials with more than 90% recyclability, reducing carbon emission by 40% in its lifecycle compared to conventional equipment.
In the survey of 1,000 equipment operators, 92% reported that durable equipment provides greater stability in extreme operating conditions and reduces work fatigue by about 15%.
Reduces Operator Strain
A study of 500 operators found that equipment with electric assistance systems reduces physical strain by 30% and fatigue by about 25%. For example, an electric towing vehicle with intelligent driving assistance features has a steering wheel resistance of only 0.5 Newtons, while in traditional equipment, it is 2.5 Newtons.
A logistics company once introduced 50 electric forklifts with an ergonomic seat design, adjustable into 10 sitting positions to reduce spinal pressure by up to 30%. According to the statistics, using forklifts brought workers' sick leave rate from 2.5% to 1% every month and indirectly saved over $70,000 every year due to reduced labor costs.
The survey of 30 port equipment operators shows the average recorded time of fatigue drops from 4 to 3 hours of use in devices featuring automatic braking, while shock-absorption systems on the same reduce the amplitude of the ground vibration transmitted to the seat by 40%.
One automobile manufacturing plant claimed that the introduction of reduced factory noise levels from an average of 90 decibels to 65 decibels, saving around $28,000 annually.
In the environmental project, an automated waste processing equipment was introduced. The operation time recorded was reduced by 20%. According to data, the system reduced compensation cases for repetitive strain injury by 10 every year, with an average saving of $7,000 per case.
An automatic load-balancing electric towing vehicle decreased the operating intensity by 20% and dropped cargo rates by 50%.
Given the price of the smart device, about $56,000, it saved approximately $21,000 every year in injury insurance costs and production loss. It can recover the cost in three years. A logistics company upgraded its equipment, reducing the cost of employee injury insurance from $168,000 to $112,000 per year and saving nearly 35% in total.
In the user feedback survey of 200 electric devices, over 90% of operators reported that an ergonomic design reduced fatigue by a great margin, increasing the daily operation time by 10%
Adapts to Various Loads
30 tons reduces energy consumption by 40% when towing 5 tons of cargo. Research shows that load-adaptive technology can save businesses approximately 15% in annual electricity costs.
The performance of an electric forklift equipped with load detection sensors keeps steady and stable when carrying 500 kg to 2 tons. According to data from a logistics center, it increased operations by 25% and reduced electricity costs by 20% month after month, saving over $16,800 each year.
A port tested an electric towing vehicle with an adaptive control system. The power is 10 kilowatts during transport of 1 ton cargo but automatically goes to 50 kilowatts in case of transportation of 15 tons. Energy utilization rate: in full load, recorded data was 92%, which on comparison is 15% higher than traditional equipment. Thus, this one single capability results in the reduction of energy waste of the port by approximately 5% every year, saving around $280,000 in operation cost.
The electric handling equipment automatically adjusted the gripping strength within a load range from 50 kg to 5 tons with less than a 1% error margin. In this way, it reduced component damage by 80%, saving the plant about $42,000 every year in repair and replacement costs, while increasing the efficiency of the plant by 10%.
There's certain equipment with the temperature sensor that supports a very terrible environment, a temperature range between -10℃ to 50℃, combined with humidity. A mining company once reported: such equipment has improved the transporting efficiency of ore within the wet, acacia tunnel up to 18%, reduced drops by 50%, increasing annual income to $1.4 million.
It is estimated that electric devices installed with this technology can cut carbon dioxide emissions by about 10 tons every year.
A device with an AI control system can reduce the possibility of tipping due to load shift by 70%. One food processing plant applied this equipment and reduced annual economic losses from cargo tipping accidents from $280,000 to less than $70,000.
According to the survey, companies that introduced load-adaptive equipment saw their accident rates go down by 30%. A chemical enterprise avoided five hazardous chemical spill incidents caused by uneven loads thanks to this technology.
One set of equipment at $70,000 can save enterprises about $28,000 per year because of energy efficiency and saving maintenance costs. One logistics enterprise that replaced the traditional equipment with load-adaptive compensating models managed to reduce its annual operation cost by 15%, totaling savings of $7 million
Safe in Tight Spaces
Considering the width of an is only 1.2 meters, this can navigate a 2.5-meter-wide aisle with a turning radius of just 1.3 meters. This design has been studied to decrease the collision risks in a narrow warehouse environment by 40%, while increasing operational efficiency by 15%.
Tests show that the highly accurate self-driving, electric towing vehicle can keep the error within 2 centimeters while loading and unloading containers, whereas for traditional equipment, the average error could go as large as up to 8 centimeters. Statistics show that the equipment saves around 15 cargo damage incidents every year caused by positioning errors and saves nearly $280,000 in repair and insurance costs for the ports.
An electronics manufacturing plant put into operation electric transport vehicles with built-in intelligent obstacle avoidance systems able to detect obstacles within 3 meters and brake automatically in under 1 second. This kind of technology has contributed to reducing the probabilities of collision between equipment and operators by 70%, reducing the rate of accidents from five per month to less than one. Such technology saves this plant about $70,000 annually in the sphere of safety.
Automated electrical facility of less than 2 square meters footprints navigates the accuracy of ±5 mm in operation between the shelves. Data of a large supermarket chain shows that the device can raise the warehouse storage density by 20% and saves more than $70,000 in operation every year.
Tests prove that electric forklifts equipped with 360-degree panoramic cameras reduce the reaction time by 30% in complicated areas, hence reducing accidents by about 25%.
Some electric devices boast low-vibration drive systems that can work in narrow mine tunnels, with a vibration amplitude of only 0.2 millimeters, compared with 0.8 millimeters for traditional equipment. A mining enterprise reported that this technology reduces mechanical component failures caused by vibration by 10 incidents annually, saving around $140,000 in maintenance costs.
A smart device costing $84,000 saves about $28,000 annually related to accident expenses and increases production efficiency by 5%.
Among 200 operators, more than 90% felt much less stress with new electrical equipment in tight spaces, while improving their comfort level by 25%.
With their high safety, electrical devices produce as low as 50 decibels in small areas of use, compared to older types of equipment producing over 75 decibels