How Can Warehouse Tuggers Improve Operational Efficiency
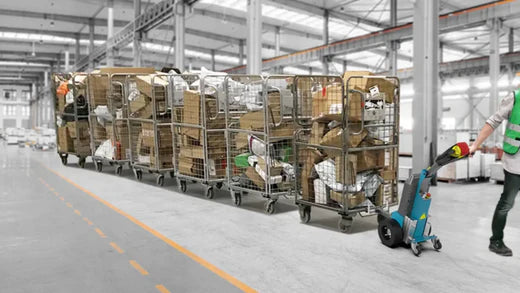
Warehouse tugger trucks significantly enhance overall warehouse operational efficiency by reducing manual labor, increasing transportation speed, optimizing inventory management, improving warehouse layout, lowering operational costs, and enhancing safety. Their efficient and intelligent transportation methods help warehouses achieve faster, more accurate, and lower-cost material flows.
Reducing Manual Labor
Most warehouse operations rely on manually handling goods, which eats up labor and increases human errors and accidents. Most research data prove that the manual handling of heavy items over a prolonged period is one of the significant contributions to warehouse injuries caused by repetitive tasks. The most effective way to overcome all these problems is the introduction of electric tugger trucks. Tugger trucks can haul a large amount of bulk goods easily and thus reduce the repetitive handling task physical burden on workers.
In large warehouses, a tugger can pull multiple carts at the same time, thus adopting a multi-cart linking mode that vastly improves transportation efficiency. As found in most best warehouse management practices, tugger trucks could enhance the transportation capacity for each worker by about two to three fold, leaving workers to concentrate on detail work such as picking and packing. Operationally, this has improved operational efficiency and fewer human errors.
With the arrival of electric tugger trucks, now warehouses can easily "automate" their operations. Modern warehouses experiment with autonomous tugger trucks, which work under programmed modes to transport goods over defined paths automatically, thereby cleaning the labor process and optimizing workforce utilization.
Increasing Transportation Speed
One of the primary objectives of operational efficiency improvements in a warehouse is to improve transportation speed. Especially in this, electric tugger trucks have proved effective. The transport speed of electric tugger trucks typically increases by between 30% to 50% over that achieved with standard manual handling. In some highly automated warehouses, such as those equipped with electric tugger trucks, the efficiency of transportation can go up to as high as 2,000 pallets per hour.
This efficiency is not only in transport over longer distances; electric tugger trucks are also highly effective in short-distance, high-frequency tasks. For example, in the order picking area, tugger trucks can very quickly and accurately transfer the pallets from the shelves to the packaging areas along the designated smart paths, thereby eliminating hold times and time wasted when using manpower to handle. The design features of electric tugger trucks also enable them to pass through narrow aisles, thus saving more time during transportation.
An example might be a large electronics warehouse in which electric tugger trucks were deployed for use in moving goods from one place to the next. The time to transport goods from the receiving area to the sorting area was reduced from 45 minutes to 20 minutes. Thus, this cut the time for transporting goods between zones almost by half. Improvement in speed directly increases the overall efficiency of the warehouse, allowing it to execute a greater number of orders, hence raising revenues.
Improving Inventory Management
If you intend to boost operational efficiency in warehouses or make it cheaper, inventory management is an indispensable tool. Conventional methods for managing inventories involve manual recordkeeping and manual checks and might lead to obsolescence and inaccuracy in the data collected. These would consequently produce errors in time and accuracy concerning orders. The benefit of the electric tugger truck on shipping goods is based on the way it meshes into warehouse management systems (WMS).
Data analysis provides that investment in tugger trucks should serve to reduce inventory errors by about 20% and up to 30% in some cases. In some advanced warehouses, electric tugger trucks can synchronize with the WMS instantaneously, ensuring that every movement in the warehouse is recorded through automated data transfer and tracking. This enables real-time data updating for warehouse managers to keep track of the location and state of goods, preventing any error in inventory or amber management.
A global e-commerce warehouse uses electric tugger trucks that help reduce the cycle time between shelving and retrieval by 30%, while inventory accuracy from 100% has improved by 15%. This degree of inventory accuracy allows the fast-turning warehouse to respond to customer demands almost instantaneously while cutting overstock wastage from inventories.
The highly automated continuous efficient operation of electric tugger trucks permits the aforementioned warehouse to implement on-demand picking, where the system directs the tugger truck to automatically move the ordered items from the shelving area to the picking area for zero inventory lean management.
Optimizing Warehouse Layout
The utilization of space in a warehouse is directly proportional to the overall efficiency of the operation. The traditional setups of warehouses are mostly designed to adapt to manual handling operations, resulting in lower space use and a longer transportation path. In such cases, electric tugger trucks come in handy as they help warehouses to optimize layout and improve space utilization for faster logistics operations.
A study on large-sized warehouses indicated that up to 25% increase in space utilization could be achieved using tugger trucks. Electric tugger trucks further allow changes in layouts to be more flexible and navigate through very narrow aisles, avoiding redundancy in highly available space. This ultimately leads to warehouse efficiency in stacking products while keeping paths clear for transport.
Electric tugger trucks, for example, were introduced, and the layout of the warehouse was adjusted, resulting in an increase in the efficiency of product flow by 40%. Tugger trucks make it possible to transport goods between several shelves and sorting stations in less time-consuming tasks for manual workers. More importantly, fewer moves are needed for workers in the warehouse, thus eliminating congestion in work areas and contributing to cleaner and more efficient working conditions.
Reducing Operational Costs
Operational cost management is one of the significant areas that give businesses a competitive edge within the industry. Various amounts of labor and energy costs can comprise a large portion of operational expenditure incurred in warehouse operations. The ability to import electric tugger trucks into the warehouse facility can serve to reduce operational costs in most instances.
Electric tugger trucks reduce warehouse manpower costs by 30%-40%, according to industry data. Not just does this reduction in manual handling work, but the function will also be accomplished efficiently by a tugger truck, thus maximizing the load carried by each worker. Further, once the efficiency of transportation increases, the required workforce for the warehouse operation is also reduced, saving costs in wages.
Another factor that reduces the energy output of electric tugger trucks is their use in large warehouses, where they are found to be viable and cost-effective in environmental aspects with electric drivetrains as compared to traditional fuel-powered vehicles. Results showed that electric tugger trucks reduce energy consumption by around 25% compared to their fuel-powered counterparts, and savings are quite significant in the long run.
For example, a logistics company had an annual energy cost reduction of about 15% after electric tugger trucks were adopted, besides a reduction in costs for vehicle maintenance and overall management expenses. The result of this has been an impressive reduction in the overall operational costs of the warehouse and increased profitability of the whole organization.
Enhancing Safety
Warehouse safety has always been a big issue in the industry. Electric tugger trucks increase operational efficiency but also improve safety standards. Traditional warehouse operations require manual handling, which, on the other hand, creates high-risk accidents such as slips, trips, and collisions. Intelligent electric tugger truck designs with multiple safety features incorporate such intelligent systems, contributing to eliminating such accidents.
These days some of the latest models of electric tugger trucks not just have anti-collision sensors but also automatically adjust their driving rate to the environment so that collisions with other equipment or workers do not occur. In addition, the driving paths of tugger trucks can also be set very precisely, reducing the operating burden for the driver and minimizing the occurrence of operational mistakes. Statistics show that accidents caused by the use of tugger trucks in warehouses are more than 60% less than with traditional manual handling.
In a high-risk environment, in warehouses, the electric tugger trucks cut the number of work-related accidents by approximately 50%. That automatic stop system holds the tugger truck in emergency, once when keeping an eye on all the obstacles around, and it stops the vehicle immediately on contact. Therefore, it eliminates possibilities of accidents. Such enjoyable intelligent, safety features indeed increase safety for warehouse workers besides ensuring the safety of material movement inside too.