How Do Tugs Revolutionize Material Handling in Modern Warehouses
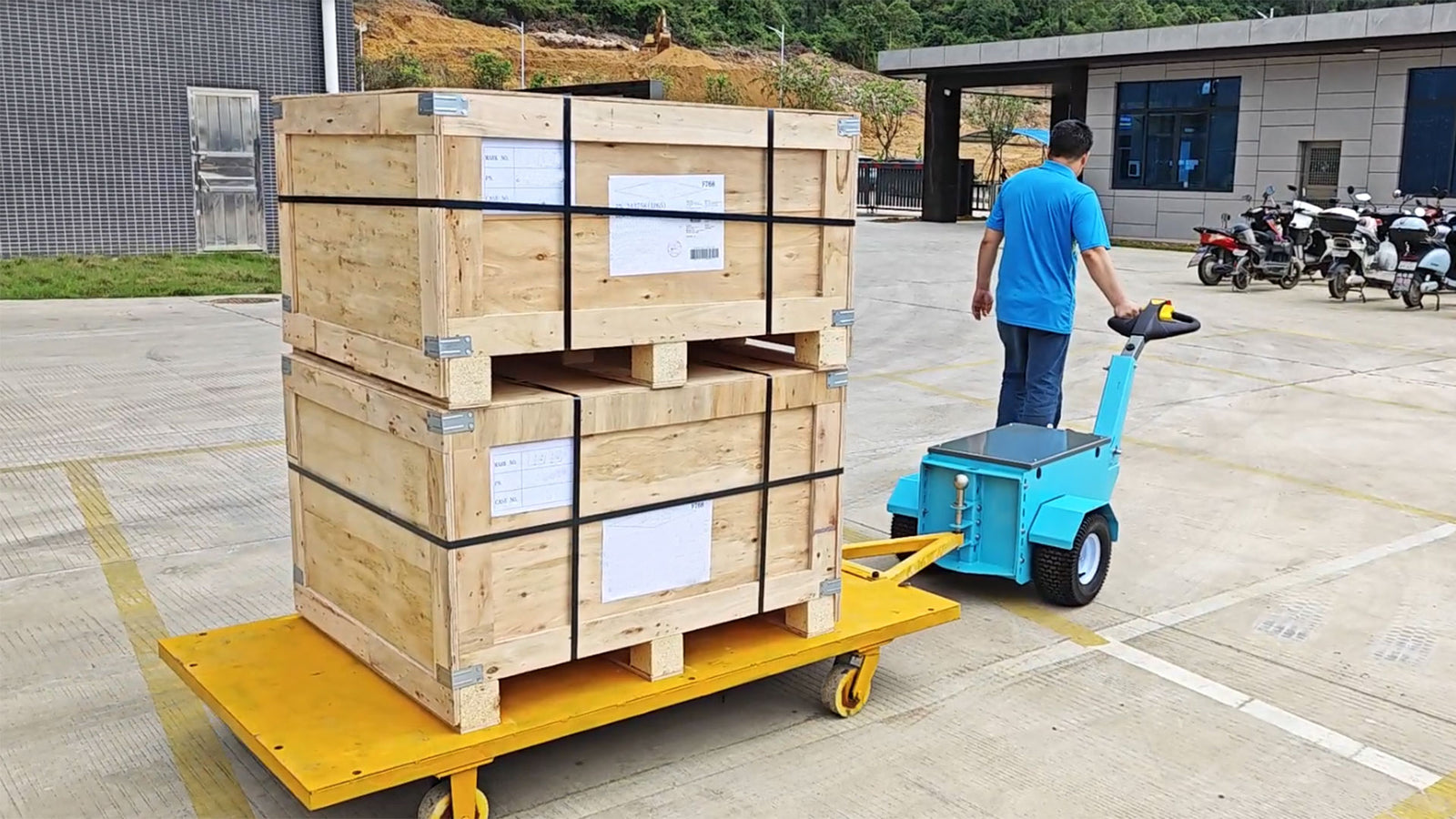
Tugs have taken material handling in modern warehouses to the next level by increasing handling efficiency by more than 50%, reducing labor costs by 30%, and lowering breakage rates by 20%. Their compact design with an automatic navigation system can reduce aisle widths by 30% to optimize storage space utilization.
Improving Efficiency and Productivity
With the inclusion of tugs into warehouses, material handling efficiency and productivity have remarkably improved compared to traditional material handling equipment like forklifts. Tugs have design and functional advantages over conventional equipment. By either towing or pushing, tugs are able to move materials, move more goods, and complete jobs faster, adding value to overall productivity.
Tugs can move more goods in one trip. Whereas conventional forklifts are normally restricted by the load capacity of their forks, a tug is able to tow a convoy of several material carts—like box carts and pallet carts—and considerably increase the quantity of merchandise moved per trip. This, in return, reduces the number of round trips and subsequently cuts down on transportation time. It can be estimated that tugs used in the warehouse can deliver many box carts to the production line in one trip, reducing material waiting time and therefore increasing the continuity of production operations.
Because of the nature of the operations that tugs perform, they hardly require multiple lifting and lowering motions, which makes operations much easier compared to using forklifts. In addition, with electric steering and power systems, tugs can always work at a constant speed regardless of heavy or light load weights. Working efficiency can be guaranteed while completely avoiding issues such as when a regular forklift experiences heavy loads, the working speed slows down, making it hard to operate.
Tugs work very effectively in complex environments. Most modern warehouses are huge and consist of a complex network of shelves and aisles. Compact and flexible tugs can turn and reverse smoothly down narrow aisles because their design allows them to do so for more effective handling. Besides that, some high-end tugs are installed with intelligent navigation systems for automatic path planning and obstacle avoidance. The result is that tugs can move goods around the warehouse autonomously without the need for manual control, hence further streamlining operations.
Enhancing Safety
Traditional material handling within warehouses, such as by forklift and manual handling, has often posed high levels of safety risks. Large and complicated operations can easily cause forklifts to collide while turning or reversing, and manual handling can result in employee fatigue and injury. Therefore, improving the safety of handling operations has always been one of the most important issues in warehouse management.
Tugs have distinctive safety features in design. Tugs usually move at slower speeds and are also equipped with emergency brakes and collision avoidance systems, making it even safer to work in congested or complex warehouse areas. Compared with traditional forklifts, tugs offer better operational stability in narrow aisles and corners and effectively prevent collision accidents due to improper turning.
The driving and towing mechanism of tugs ensures that, in case of a load, the center of gravity is low, making the overall structure more stable and unlikely to tip over. Because of this, they are very suitable for high-stacked or large-sized material transportation, reducing the possibility of the goods tipping over and getting damaged. Also, most tugs are now electric-powered; as such, their operations become more stable since, unlike traditional fuel-powered equipment, they do not experience uncontrolled acceleration or braking due to surges in oil or air pressure, reducing the risk of accidents.
From an operational safety perspective, tugs are also equipped with multiple intelligent safety measures. For instance, some tugs include laser sensors and ultrasonic sensors for real-time monitoring of any change in the surrounding environment and to slow down or stop automatically upon detecting obstacles. User-friendly interfaces designed by many firms have made their operation simple and intuitive, thereby minimizing risks associated with operator errors.
Reducing Costs
Tugs save a lot in terms of warehouse operating costs. Operating costs usually include labor costs, equipment maintenance costs, energy consumption, and material damage costs, all of which can be effectively reduced with the introduction of tugs.
Tugs will reduce dependence on manual labor. Conventional material handling requires much manual work, while introducing tugs means that the same work can be managed by a few persons handling the equipment, thus saving labor costs. In this process, tugs are capable of working continuously for longer periods and can therefore replace night shifts or peak period work conducted by manual groups. This not only reduces the need for employee overtime but also avoids operational errors due to worker fatigue.
Using tugs also results in lower equipment maintenance costs. Traditional forklifts involve significant maintenance, such as the maintenance of the engine, hydraulic system, and wear and tear of tires. In contrast, most tugs are electric-powered and structurally simple, which decreases maintenance frequency as well as repair costs remarkably. In addition, electric tugs do not need consumables such as fuel and lubricants to be refilled frequently, which decreases operating expenses over time.
Tugs are more energy-efficient. Electric tugs consume less energy compared to traditional internal combustion forklifts; hence, they save costs of energy consumption and accommodate modern warehouse green and sustainable operational strategies. Moreover, since electric equipment produces less heat and noise during operation, tugs can reduce the energy use of auxiliary equipment such as air conditioning and ventilation systems in the warehouse.
Another key cost control feature of tugs is a reduction in the rates of material damage and errors. With higher stability and more precise control during the process of towing, tugs can reduce the possibility of material collisions and consequent damages during transportation, hence reducing losses that the company experiences on account of material damage. This is very essential regarding fragile or high-value items, as tugs make transportation safer, hence reducing the costs associated with material damage.
Optimizing Space Utilization
Tugs are effective at optimizing warehouse space utilization. Traditional material handling equipment, such as forklifts, have larger dimensions and turning radii, hence occupying considerable warehouse operational space. Tugs have compact bodies with flexible steering systems that operate efficiently in confined spaces.
Tugs can minimize the aisle width in the warehouse. Traditional forklifts need a big operation space when turning or reversing, which means the warehouse should also have wide aisles. Tugs can work much better in a narrow aisle. In designing, the warehouse can narrow down the aisle width and provide more area for storing goods, hence enhancing the overall warehouse capacity.
Tugs provide flexible convoy towing for warehouse layout and workflow optimization. Compact tugs enable close integration of transport ways with shelf layout in warehouse design, dispensing with unnecessary routes and raising efficiency in the retrieval and storing of goods. Meanwhile, tugs can do material handling tasks easily in different areas for changing places of goods from the receiving area to the storage area or from the storage area to the shipping area, further enhancing space utilization.
They are able to conduct their operations efficiently in multi-floor warehouses. Most modern warehouses are designed with multiple floors to maximize vertical space utilization. Compact design and lightweight allow a tug to change between floors by means of elevators, which minimizes inter-floor material handling complications and further enhances handling efficiency in general.
Related Products: