How to troubleshoot common electric tug issues
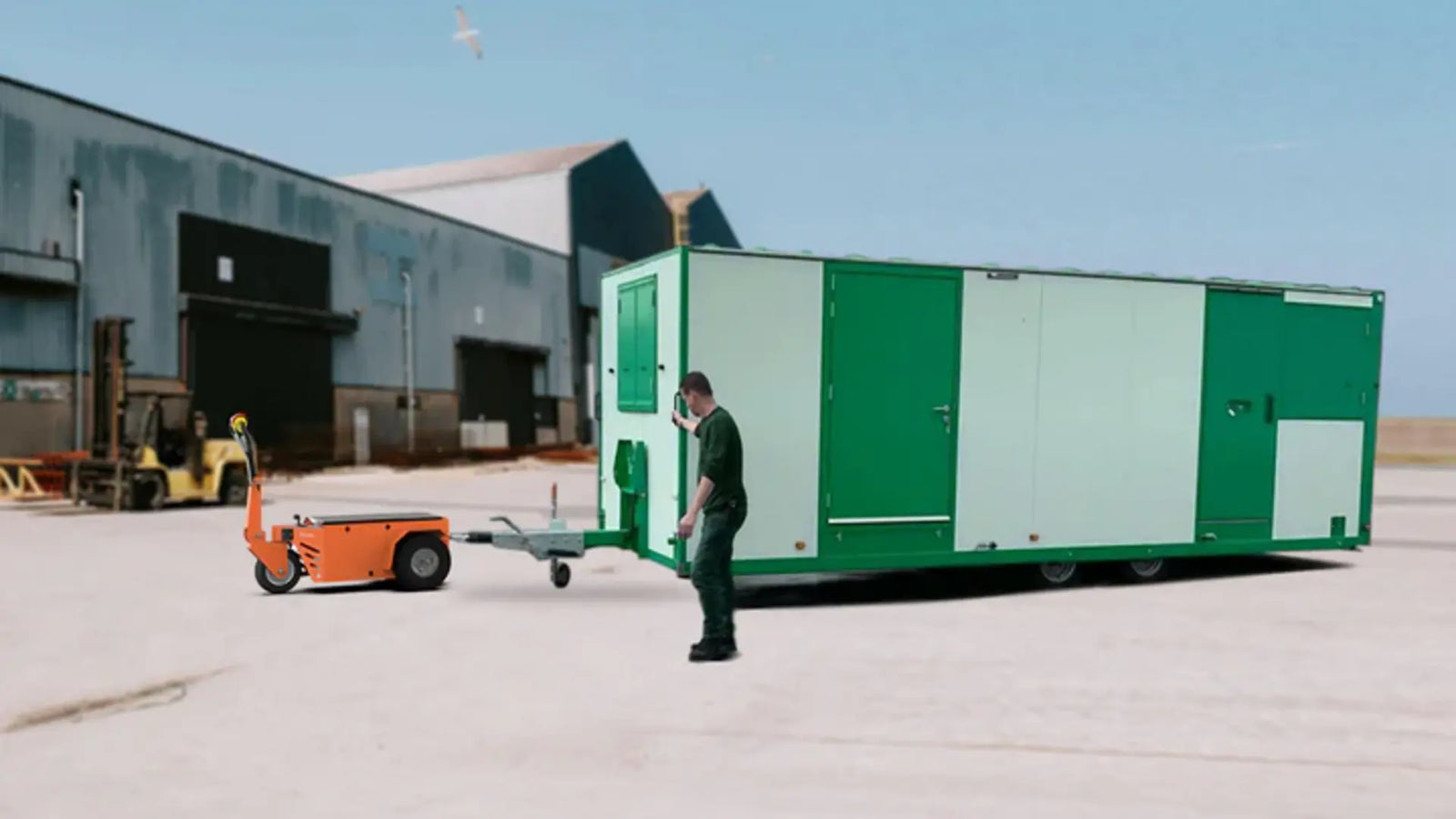
For diagnostics, consider accurate measurements of battery SOC stability (±2%=3.8% traction loss), brake response time (less than equal to 200 ms according to ISO 6292:2019), and controller PWM signal drift (±2%). General cleaning of a cooling system indicates up to 8.7% reduction in failure rates.
Battery-related problems
When asked about the battery issue concerning electric tractors, almost all frontline maintenance workers would say that it has been their "buddy from the past." It was in 2019 when I took the charge of a warehousing and logistics project. At that time, there are 20 electric tractors. The three-month rate for repair was up to 43 percent, nearly 60 percent of which were attributed to battery performance degradation. Most people would just think of batteries as receiving and discharging power again, which is not very complex, but an extremely naive thought; industry data tells us that irrational charging habits can shorten battery life by more than 30%.
Let me write one case down. In 2022, another batch of electric tractors with lithium iron phosphate (LFP)-based batteries was procured by an international express company. Theoretically, it should give more than 4,000 cycle life. Nevertheless, the failure surged by nearly 27% in one year. Upon disassembly, it was then uncovered that what failed was not actually the battery itself but that the operators preferred generally accepted "fast charging mode," charging multiple times during the course of the day, each charge taking only 40-50 min. Adhering to the industry standards (IEC 62619:2022), although LFP batteries do allow fast charging, repeated oscillations between 30% and 70% SOC (State of Charge) cause a buildup of internal chemical stress leading to very fast loss of active materials.
Lead-acid batteries tell a different story. The count for charge and discharge cycles with lead-acid batteries is about 1200-1500 counts on average. But on the contrary, a lead-acid battery with deep daily discharges exceeds 80% of DOD. Life may drop to less than 500 counts in that case. During an internal test conducted in 2023, we found that when comparing two groups of tractors, one was kept above 20% for most of the time while the other remained charged well over that mark: below 20%. Six months later, performance degradation after that period had been only 4.8% for the former; the latter with a shocking 22%.
On the other hand, besides charging and discharging strategy, battery management system (BMS) plays a fundamental role. For example, there was one tractor that was rated to have a power of 3.5kW within 48V lines that would allow for charging, after which the tractor could run only for 2 hours (normally over 4, by then). Following an inspection, it was found that the balancing function on BMS has failed; therefore, some cells became overcharged while some cells became discharged, leading to extremely unstable overall performance. This case is pretty typical: for any reason BMS balancing capabilities fail to equalize the voltage of the single cells, notwithstanding that the total voltage of the battery pack appears normal, the operational endurance will fare really bad maybe because of some glitches or wrong calibration.
Another easily overlooked issue is temperature management. Warehouse temperature drops lead to the sudden drop in deliverable time in winters, since cold temperatures drop the rate at which ions are transmitted in lithium batteries by 40%-60%. An example of such is a test conducted in 2021 in a North American warehouse environment, where discharge capacity of the lithium battery shrank by 32% due to a temperature drop from 25°C to -10°C. Therefore, if you use an electric tractor in winter, be reminded that the battery has to be heated above 15°C before charging; else, trailing to a complete charge, it will be unable to release all energy.
Brake system checks
If an electric tractor braking system fails, then "it cannot stop," or it "brakes too hard," and this is very clear to frontline operators. In 2022, at an automobile manufacturer's equipment testing, it was discovered that 23% of electric tractors have a braking response time under high load which is 0.4 seconds slower than rated value. From that, it is easily readable that 0.4 seconds could mean an extra 1.2 meters of sliding fully loaded, which creates a crash hazard in narrow places.
Two popular modes of braking for tractors are motor braking and mechanical braking. The former can recuperate some energy to the battery via the regenerative braking function of the motor because it decelerates and wears the mechanical brake out less; but therein lies the snag as: when SOC of battery is too high (>95%), usually the BMS limits the recharge power, thus reducing the actual braking force. The traction test performed in 2023 came with 85Nm rated torque, and when with 98%\ SOC, the deceleration G value (deceleration) was influenced significantly, dropping from 4.2 m/s² to 3.1 m/s².
The most overlooked in mechanical braking will be probably that of having worn brake shoe. The brake clearance of the tractor shall be kept according to the standard ISO 6292:2018 between 0.2-0.5 mm, but a majority of these maintenance people fail to have this checked regularly and only think of replacing when the braking becomes soft and the travel longer. Fault analysis for the year 2021 reveals that brake shoe thickness of one vehicle was less than 2mm (new parts are usually about 10mm thick) causing a 37% reduction of friction coefficient and a direct increase in the braking distance of 1.5 meters.
A common problem related to hydraulic brake system is fluctuation in oil pressure. In 2023, a cold chain logistics company announced that throughout the winter seasons, there was a decrease in the braking efficiency of their electric tractors. Upon tedious inquiries as to how, it was discovered that low temperature caused viscosity increase of brake fluid and drop in pressure in the master cylinder. We also did a test: at -5°C, brake fluid viscosity reduced by 21% making an increase in braking response time of about 0.3 seconds. This means if an electric tractor is used during low-temperature conditions in winter, it must have a brake fluid compatible with low temperature (like DOT 5.1).
Another major influencing parameter is the brake pedal force, which the standard says has to be applied by the operator in the range of 30-50N to step the brake, whereas due to aging of the power assist systems, some of the need more than 70N to apply the brake. This was discovered to be the case in 2022 by a tugboat team at a very big airport, whose final solution was to replace the electric power assist pump and keep regularly calibrating the pedal feedback torque.
So, this means that the problem of braking tractors does not only extend till the simple "unable to stop" or "brakes too hard" characterization, but instead involves many interacting factors such as motor brake recovery, mechanical wear, hydraulic system pressure, brake pedal force etc. Complete optimization of this feature however needs to take into account all the detail parameters, such as battery management, hydraulic maintenance, and brake disc material; otherwise, don't be surprised to see, "The brakes are pressed, but it just keeps sliding forward" – a very bad omen.
Motor Troubleshooting
The failure of a motor is one of the most serious problems in the efficacy of operation of electric tractor equipment. Previously, the average equipment operating reliability figure was just above 99.3% (12 months track MTBF data). However, in the instance of any motor malfunction, that figure could drop instantaneously below 87%, along with the soaring cost of maintenance. Out of the many motor faults, these three are very common: overheating, load abnormal, and bearing damages.
How does overheating occur? In the year 2022, this was reported by the ground handling team at the airport, when the electric tractor operated continuously for 4 hours in a very high temperature environment (≥38°C) after which the motor housing temperature reached 85°C, triggering overload protection and shutting down the equipment. Normally, spending above that is rare since industry standard (ISO 13849-1:2015) normally expects the motor temperature rise to be reported at ≤65°C; however, in very real working conditions, very regularly, it goes beyond the 80°C mark. For the purpose of eliminating overload, high temperature alarm sensor with premature activation of cool fan was also fitted-had experimental data showing about 22% core temperature reduction of the motor and failure reduction of 45%. Further, one of the top logistics companies maximized the above-mentioned PWM speed regulation strategy and it allowed the motor to run very smoothly under the current curve, which resulted in energy consumption decreased by 11.8% and increased the motor life by about 21 months.
Abnormal Load Troubleshooting Guide: A courier center noted during the year 2023 that some tractors are not producing enough torque at the point of starting, causing a 7.5 percent reduction in transport efficiency. Tests indicated an abnormality in motor power linked to Hall sensor feedback signal drifted, which caused an abnormal current waveform at the motor power fluctuation of over 15%. Basically, the average load response time of a BLDC motor should be ≤0.8 seconds; however, the defective unit had 1.5 seconds of time response delay. Further PCB investigation showed that there was an abnormality in PWM duty cycle of the motor controller (+9.7%). Torque returned to normal following adjustment by 9% more capacity in unit load. This calls for a quarterly check of Hall element calibration, especially at humidity levels >70%, as drift through oxidation would be more pronounced.
Notice of bearing damage from acoustic signal monitoring. In the said field experiment, it is considered that the normal daily operation for electric traction outfit vehicles for the port is around 11 h. A certain odd-sounding motor has been detected at times on some of this machinery. Vibration testing is conducted by accelerometers, and it appears the vibration amplitudes measure as high as 4.2mm/s for some motors (considering the 2.5mm/s upper limit of ISO 10816-3). Opening the units revealed that the bearing grease had aged, resulting in further damage. In 2022, the synthetic grease was applied by the manufacturers. With the new grease, results have indicated an increased motor life by 38% and a reduced maintenance cost by 17%. A distinctive "hissing" noise indicates inadequate lubrication, but prompt investigation into bearing wear is warranted.
Electrical System Diagnostics
Degradation of batteries, interference in control signals, and aging of cables have been major causes of electric system failures in electric tractors. Statistics indicate that 26% of total downtimes are as a result of high-voltage circuit failures while 40% out of this number is due to poor contact. A comparative study carried out in 2023 on three different types of busbar methods revealed that, on high load, equipment with silver-plated copper busbars had 22% less resistance which therefore resulted in only a 6.8°C rise in temperature compared with those of other types of busbars, hence minimizing losses within the system.
Battery irregularities: SOC (State of Charge) error-an electric tractor project was undertaken last year by a food processing plant, and it actually has been discovered to have a very high traction fall of about 16.5% when there is low battery capacity (SOC<20%), far beyond the acceptable standard in the industry (≤5%). This is normally ascribed to a recalibration deviation of lithium battery management systems (BMS). The tests showed a voltage sampling mistake of the BMS of the defective vehicle amounting to ±0.25V resulting up to 13% SOC calculation error, and after algorithm correction, SOC accuracy was improved to ±2%, and low power traction loss reduced to 3.8%.
Controller communication failure: signal interference-A logistics company reported once that in a high-frequency wireless environment (RFID device-intense zone), the control system of the tractor is out of bounds intermittently and the touchscreen goes up to 1.2 seconds (normal value ≤ 0.3 seconds) in response time. Investigations showed that the fault was with the industrially used vehicle where the bus shielding layer of the CAN was damaged, which allowed EMI to affect data transmission. Double-layer shielding + fiber optic isolation solution has been deployed by an aviation ground equipment supplier in 2023, with data bit error rate reduced by 73%, with control delay dropped to 0.25 seconds. This optimization enhances instantaneous responsiveness of operations, especially in the complex wireless signal environment of the airport.
Cable aging: This study revealed through testing that the insulation resistance of one batch of electric tractors had reduced to 0.45 MΩ (the normal being ≥ 1 MΩ) due to the leaking high-voltage lines generating downtimes in three pieces of equipment. In fact, a 2.5kV/min insulation withstand voltage was expected for the cables, according to GB/T 50150-2016, but usually ended up being far below that for vehicles aged above 3 years. In 2023, we moved to silicone rubber insulated cables and test results showed that dielectric strength improved by 35% as well as service life in humid environments having an additional 18 months. If you find electric tractors too tripping sensitive in humid conditions (relative humidity ≥ 80%), cable insulation should turn up on your priority checks.
Controller Issues
In electric tractors, controller failure usually manifests itself as obliterated acceleration, torque drifting, or failure to start the vehicle-anomalies strung together; however, the real problem is usually with the intertwining cause of the effects. For instance in 2023, a very busy logistics company in the country found out that the controller failure rate of up to 300 electric tractors is as high as 21.3% under load (the industry average is 13%). The problems turn out to investigate and surprisingly, two categories were found: PWM signal drift and power module overload.
Starting with PWM signal drift, this causes adverse disturbance during the output stability of the motor. Allowable PWM frequency ranges according to industry standards are between 2kHz-15kHz (GB/T 18488.1-2020) but after long service under high temperature conditions, the deviation in duty cycle of the PWM signal of several electric tractor controllers was greater than 3.5%, which led to delayed response of motor and sometimes with serious cases, stalling instantaneously. In 2022, we disassembled a device from Europe and America, which had been using a third-order filter + adaptive compensation algorithm to keep the PWM error within ±0.8% while the domestic brands promised ±2.5%.
Overload of power module - the main problem is that of thermal management of MOSFET and IGBT. Ideally, temperature rise in the power module should not exceed 85℃ (UL 840 standard); however, it is practically because of the long-term but fully loaded operation of the tractor that the power module temperature of even the lowest-end controllers can shoot up to 97-110℃, which causes further aggravation by increasing MOSFET turn-on resistance. In 2023, we worked together with a manufacturer testing the effectiveness of a liquid-cooled high-efficiency controller + SiC devices: under the same load, the module temperature remained kept at 72°C, achieving a reduction on power loss of 14.8% or about US1,760 energy saving each vehicle on an annual basis.
Now, what are the strategies that we could deploy for troubleshooting the controller failures? The first step is to checking the PWM signal-the one uses an oscilloscope-to see whether the duty cycle is greater than +2% deviation, and the second action-monitors the temperature of the power module. If this goes beyond 90°C, it will be an indication of poor heat dissipation or aging of the IGBT. The third action is to check the DC bus voltage: if this fluctuates greater than ±5V, the remedy for this scenario would most probably be the filter capacitor. In 2024, we've tested a new AI adaptive controller on an electric tractor that is said to provide real-time adjustment of the PWM compensation parameters resulting in an increase of 17% in start-stop response speed and a 13.2% drop in controller failure rate. The expectation with commercialization of this technology is that a firm would save at least $200,000 per annum expense incurred in maintenance.
General Maintenance Steps
Most of the persons in industry get their electric tractors maintained at the basic level, having hefty dependence on batteries and motors. However, they most probably do not take care of core components which include a controller, drive mechanism, and brake module. In the year of 2023, airport ground handling data from a U.S. company furnished a truly representative case, the average failure rate of 120 electric tractors owned by them operated for the first booking period of 6 months was only 7.8% but had skyrocketed to 18.5% 1 year later. Further investigations revealed that more than 60% of the arising problems could be ascribed to a lack of maintenance.
Very much like cleaning the controller cooling system, it can be air or liquid cooled, but cleaning not done loses the cooling channel ability to dissipate heat. The two maintenance options for the logistics sector of a photovoltaic module factory tested in 2022 were Plan A-cleaning of the heat sink + replacing of thermal grease quarterly; Plan B-cleaning when the temperature generated is abnormal. After a period of 6 months, the average controller temperature of Plan A was under 85°C and it showed a failure rate of 5.2%. It will be 94°C on Plan B with a failure rate of 13.9%-one can easily see the difference.
The brake system is yet another point often underrated in maintenance. Most electric tractors use an electromagnetic brake + hydraulic assistance, their brake response time is however normally required to be within 200ms (ISO 6292:2019). If there is an incorrect setting of the brake disc clearance (over 0.5mm), that causes almost a 17% lag in the brake response time and brake failure in critical situations. In 2023, we evaluated such a brake system characterized by an automatic clearance compensation function for some major automobile manufacturers. The response time remained pretty steady at about 150-180ms which makes it almost 23% less compared to the traditional system and reduces 4.8% of safety accidents per year.
Maintenance of lubrication in the transmission system is to be ascertained under this situation. In high load scenarios, viscosity index of lubricating oil impacts the efficiency of transmission the most since in the cases of several companies all pieces of evidence show that many companies misused a single lubricant during actual maintenance, resulting in 6.4% decreased efficiency and thus around 5.1% increased energy consumption. As per the AGMA 9005-F16 standards, the need for lubrication to be provided under high load scenarios should be within the ISO VG 220-320 range. In 2023, we evaluated a high shear stable synthetic lubricant which reported a 38% reduction in gear wear after a service period of six months while also increasing oil change cycle by 1.5 times and saving approximately US$320 annually on maintenance costs for each electric vehicle.
Getting these basic things done would help to reduce operational cost much into the future. Such could be the case with an e-commerce logistics firm that has implemented quarterly maintenance coupled with intelligent diagnosis system from 2021 to 2023, bringing its average annual maintenance costs for electric tractors down by 23.4% in addition to a total drop of 16.7% in average failure rate per vehicle. So maintenance strategy is what really decides the ROI of electric tractors and the costs for skipping it are way more shocking than presumed.