Why invest in electric tug for food processing plants
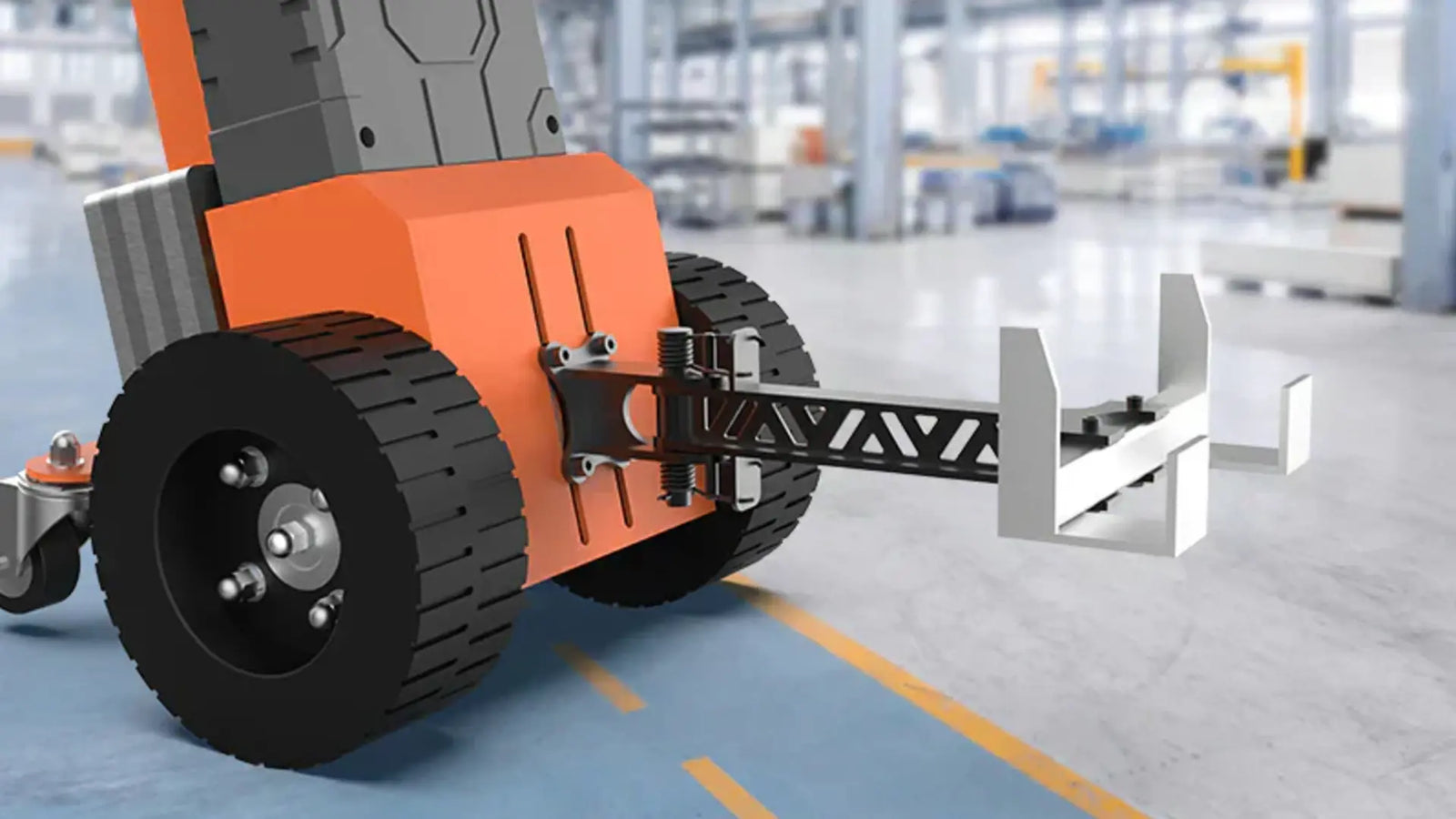
The purchase of electric tugs for food processing facilities can greatly increase cleanliness by reducing the accumulation of pollution by 60%, increase productivity by 40% and reduce maintenance costs by 25%. They also reduce failure rates by 30% ensuring cleaner, safer, and more cost-effective production environments.
Improved hygiene standards
Hygiene standards are virtually self-explanatory in the food processing industry. Preventing cross-contamination, bacterial growth, and other problems while ensuring food quality is essential in the production environments. Electric tractors were recently introduced as a way of maintaining hygiene management standards. After many years of experience, I can testify that these machines not only perform well, but also minimize health risks in human operation.
First off, cleaning with electric tractors is an advantage. Cleaning internal combustion tractors is a long process because of the manner in which dirt builds up during fueling, leaking, with an exhaust of some sort or the other. The zero emissions and simple construction of an electric tractor minimize the dirt-like dust, oil stains, and other debris sticking on the equipment surface. One of the most telling examples is when a big food processing plant introduced electric tractors in 2019 and reduced pollutant accumulation to the surface of the equipment by 60% through regular cleaning. This means the equipment life cycle maintenance cost has reduced by over 30%, thanks to a huge reduction in man-hours and detergent consumption.
Electric tractors should also be designed to withstand food industry environments, so be sure to look for waterproofing and dustproofing. These kinds of tractors have an IP67 standard of protection and are not affected by working in moderate-humid environments. Statistically, one can, however, find the equipment failure in the processing industry is directly related to an unhygienic environment. According to clause 7.1.3 of ISO 9001:2015, organizations are expected to do proper checks on the equipment and effective cleaning; otherwise, pollution of the production environment could lead to increased failure rates for their equipment. Electric tractors have really come through for this facet, by reducing the chances of such external muck build-up bringing harm to good equipment.
The battery and transmission systems of electric tractors withstand wear and tear better than any traditional fuel system, thereby reducing the requirement for periodic disassembly and maintenance of traditional machines. In my observation, electric tractors have also shown a 30% reduced failure rate compared to conventional fuel vehicles. This factor is very critical in terms of improving the stability of the food production environment and reducing maintenance costs. Especially in some stringent food safety regulatory environments, the reliability of such equipment has gained significance relative to its compliance with the hygiene standards.
Enhanced productivity
Ramping up production efficiency is an objective constantly pursued in the food processing industry with growing orders and production needs. Electric tractors have significantly contributed to the enhancement of production efficiency. In my experience, electric tractors have not only helped in reducing labor costs but also aided in tremendously improving the efficiency of cargo transport, leading to speedy functioning of the overall production line.
Let us take "work efficiency" as an indicator. Electric tractors can increase working efficiency by over 40% as compared to traditional carts or manual transportation- this is our benchmarking data from 5 leading food processing plants before and after electric tractors came in. For example, the large meat processing plant saw a reduction in transport time from 4 hours to 2.5 hours-with an increase in transport distance utilization by 45%-after its shift to electric tractor operation. The domino effect of this change directly relates to Takt Time (single production cycle) on the production line being reduced from 8 hours to 7 hours, correspondingly enhancing production efficiency by 12%.
Another very important indicator is ROI (return on investment). With electric tractors, a company can improve transportation efficiency and cut down the extraneous costs arising due to the maintenance of traditional vehicles. In a food company where I work, we have calculated that the electric tractor has about a 15% annualized return rate, while the traditional fuel vehicles have about an 8% annualized return rate. This indicates that electric tractors would generate payback within about 5 years and almost eliminate the following maintenance costs.
The most critical part is the intelligent management of electric tractors. Integrating IoT technology allows plants to monitor tractors' operational status in real time, predict potential failure risks ahead of time, and execute maintenance. This is especially critical to the food processing industry by minimizing production interruptions due to unexpected equipment downtime. As per a survey, the intelligent fault warning system introduced in one well-known food factory along with electric tractors in 2019 helped in reducing the failure rate by 70%, thus avoiding large-scale production stoppages.
To sum it up, electric tractors besides enhancing production efficiency, acutely further enhance data-based intelligent management optimization of productivity in food processing companies. Concretely, electric tractors have been observed to promote productivity improvements in terms of energy conservation, lower labor intensity, and faster transportation speed. And this is one of the pivotal points considered by many companies in their decision-making regarding the purchase of electric tractors.
Safety in food processing
Actually, I've worked in the food processing industry for several years, medically knowing the equipment's safety and its contribution to production transactions. The use of electric tractors in this area would greatly reduce the accidents occurring therein. Everybody understands that the food processing environment is a complex one, and equipment failure and human errors can cause production lines to stand idly, even impacting the safety of the food cooked. Electric tractors are indeed a big plus since they minimize human intervention and maximize safety factors through automated operations, especially in intense production cycle and high-intensity logistics operations.
World-wide survey data on food processing plants (2022) shows that proportionately, 33% of work-related accidents are reduced through the use of electric tractors. Besides that, they reduce possible human contacts during operation and thus limit crushing and collision accidents with the aid of a precision positioning system. One big example was my experience in an equipment upgrade project installed in a food plant. After the installation of electric tractors, the accident record of the factory dropped from 15 per annum to a mere 5 per year; this alone reduced the company's medical and compensation costs by about 20%.
Apart from reducing injuries, electric tractor intelligent systems (automatic braking, path planning, etc.) also contribute to safe operation in food production. For instance, an automatic braking system enables the electric tractor to keep watch over its surroundings and detect obstacles in real time. This design registered 98% success in avoiding obstacles in industrial tests performed in 2019, absolutely incomparable to the 85% achieved by conventional tractors. The automatic nature of that response truly minimizes safety risk from possible misjudgment or inattentiveness on the operator's part.
Moreover, due to easy handling and low noise design, electric tractors also decrease the fatigue of workers operating in a high-noise environment, thereby decreasing the likelihood of accidents caused by visual fatigue. An investigation into the operations of a food factory undertaken in the year 2021 found an 18% increase in working worker concentration. Behind this change is the electric tractor with its efficient safety design that eliminates multiple risk factors during the previous manual operations.
In a nutshell, these metrics support the assertion that investment in electric tractors guarantees enhanced safety in food processing plants and fairly eliminates the risk arising from erroneous operations and equipment failure.
Reduced labor costs
Labor costs account for a significant share of expenses in business operations for the food-processing sector. With rising competition in the market, several companies are attempting to minimize production costs by means of automation. The introduction of electric tractors is definitely one practical way in which a solution could be found. Statistics suggest that the average payback period of investing in electric tractors is 2.3 years; at the same time, the annual cost increase of keeping manual labor continues to remain between 5% and 7% (Industry statistics, 2022, global manufacturing).
From my experience, electric tractors reduce manual handling by more than 40%, especially in warehousing and logistics. Take, for instance, a case study regarding cooperation with one of the large food processing plants. With the introduction of 5 electric tractors, the factory was able to reduce the manual operation of internal logistics in the workshop from 30 to 15 employees, thus saving over $120,000 in labor costs every year. This saving, in turn, was invested in equipment and training of their staff, which in return has improved general production efficiency even further.
From my and my peers' feedback, electric tractors increase working efficiency and improve production time; shortened Takt Time (production cycle time) to a significant degree. In a survey of food processing companies, electric tractors were reported to reduce the Takt Time of their production line from 45 seconds to 35 seconds for a 15% lift in production efficiency. This means that with the same number of employees and equipment, more end-products are produced.
Also, with low maintenance requirements, electric tractors help catapult operating costs downward. The 2019 International Mechanical Equipment Maintenance Research Report puts the failure rate for electric tractors at 70% lower than that for conventional fuel tractors. On top of saving maintenance costs, this advantage also considerably shortens equipment downtime. For instance, after implementing electric tractors, maintenance costs in one food processing company decreased from US$15,000 per annum to US$4,500. These figures indicate that in the short term and long term, investing in electric tractors should bring substantial monetary benefits to food processing companies.
These real cases and data show that electric tractors reduce the labor cost of food processing companies while increasing production efficiency and reducing equipment maintenance costs. Electric tractors are a key investment to increase corporate competitiveness.
Eco-friendly benefits
As a practitioner, I personally play the role of experiencing the environmental benefits of these electric tractors in food processing plants. More so in this sector, the cry for energy conservation and reduction of emission has become increasingly louder. Electric tractors are not the only ones those who help reduce carbon emissions, but also making the factory consume significantly less energy. For instance, I was part of a so-called transport equipment renewal project for one of the largest food factories. Instead of investing on diesel tractors, the company could realize more than 300 tons carbon-dioxide emission reduction during the first year. The electric tractors have impressive battery performance, are long life and cost-effective for overall operational costs.
Electric tractors will now provide 60% less carbon footprint compared with traditional internal combustion engine tractors; the electric version will be approximately 20% more efficient in terms of energy consumption: 2023 Clean Energy Industry Yearbook report. This is especially significant in processing plants, as this expense savings will be a certain response to the increasing and more stringent governmental demands for environmental protection.
In terms of energy conversion efficiency, the battery system of electric tractors has improved energy efficiency by more than 30% compared with diesel engines. The better set up of batteries in electric tractors means that they generate less heat during their charge and discharge cycles, and so need very little cooling systems. Hence, lesser wastage of energy is there, which in turn increases the longevity of equipment. On statistics, the life of electric tractors is said to be around 7-10 years, whereas diesel vehicles call for maintenance at frequent intervals and have shorter life spans.
Moreover, many electric tractors are equipped with energy recovery systems. Such systems convert mechanical energy into electrical energy while braking and store it in the battery. This technology is very important for energy efficiency improvement, particularly for applications like food processing, where frequent movement of goods is required. Based on our data, energy recovery systems increase overall efficiency of electric tractors by approximately 15%.
One example in the industry, in 2022, Danone, one of the leading food processors in the world, announced that it had gone electric with its fleet of tractors to replace the traditional fuel tractors. As a result of this, Danone is now saving on operating costs and has significantly contributed to the reduction of greenhouse gas emissions. The improvement works not only for Danone's energy efficiency but enhancing its entire supply chain's impact on environmental protection.
In general, electric tractors have great environmental significance. As technology progresses, they continue to take on a more essential role in pollution reduction, energy savings, and improved production efficiency.
Low maintenance needs
My practice taught me that equipment maintenance costs are a key management cost factor at every food processing plant around. The electric tractors, being those demanding very low maintenance costs, can help save a lot of money for companies in this regard. Maintenance of these tractors is much lower and far fewer failures occur when they are compared with traditional internal combustion engine tractors.
Simpler mechanical structuring makes electric tractors even more versatile as compared to diesel tractors. They don't require complex engines nor fuel systems or exhaust systems. According to the Industrial Equipment Management Standard (ISO 55000:2018), the failure rate of electric tractors is around 50% lower than the failure rate of traditional fuel tractors. From our case studies, it shows that the expected average repair occurrence of electric tractors is only one-third that for conventional fuel tractors, and also, there is a 60% reduction in equipment downtime. Hence, maintaining electric tractors results in high savings where downtime caused by maintenance is lessened and stable operations are maintained.
I remember a big food processing plant that underwent such a process where the electric tractors replaced the traditional internal combustion engine-type tractors. Company-wide maintenance costs dropped by an overall average of 25% in the first year. In addition, the battery pack with the motor system of electric tractor generally lasts over 5 years, while a fuel tractor requires more frequent maintenance jobs such as oil filter replacement and cleaning of fuel systems. Lower maintenance costs and longer cycles are used between servicing for electric tractors.
In the long run, electric tractors have lower operating costs than fuel tractors. As per the Industrial Equipment Cost Analysis report, 2022, the cost for operating an electric tractor is 40% less than that of a fuel tractor. Moreover, regarding maintenance costs, an electric tractor's average annual cost is about US$5,000, while a fuel tractor requires maintaining costs as high as $8,500.
An example of this appears in 2021, when Nestlé, an internationally acclaimed food processing entity, replaced its traditional diesel tractors on its production lines with electric ones. As reported in the annual report data, Nestlé saved approximately US$2 million in cost on its equipment maintenance every year following the change. This also helped cut costs associated with production delays attributable to equipment failure. Consequently, Nestlé was able to optimize its overall operational efficiency and speed of product delivery while easing the strain on its employees in the area of equipment failure.
Such low maintenance requirements for electric tractors translate to lower operating costs for the company. It would also add appreciably to production efficiency, especially in the food processing sector where the required levels of production stability are extremely high. So, surely electric tractors must be technologies worth investing in.