How to calculate ROI for electric tug investment
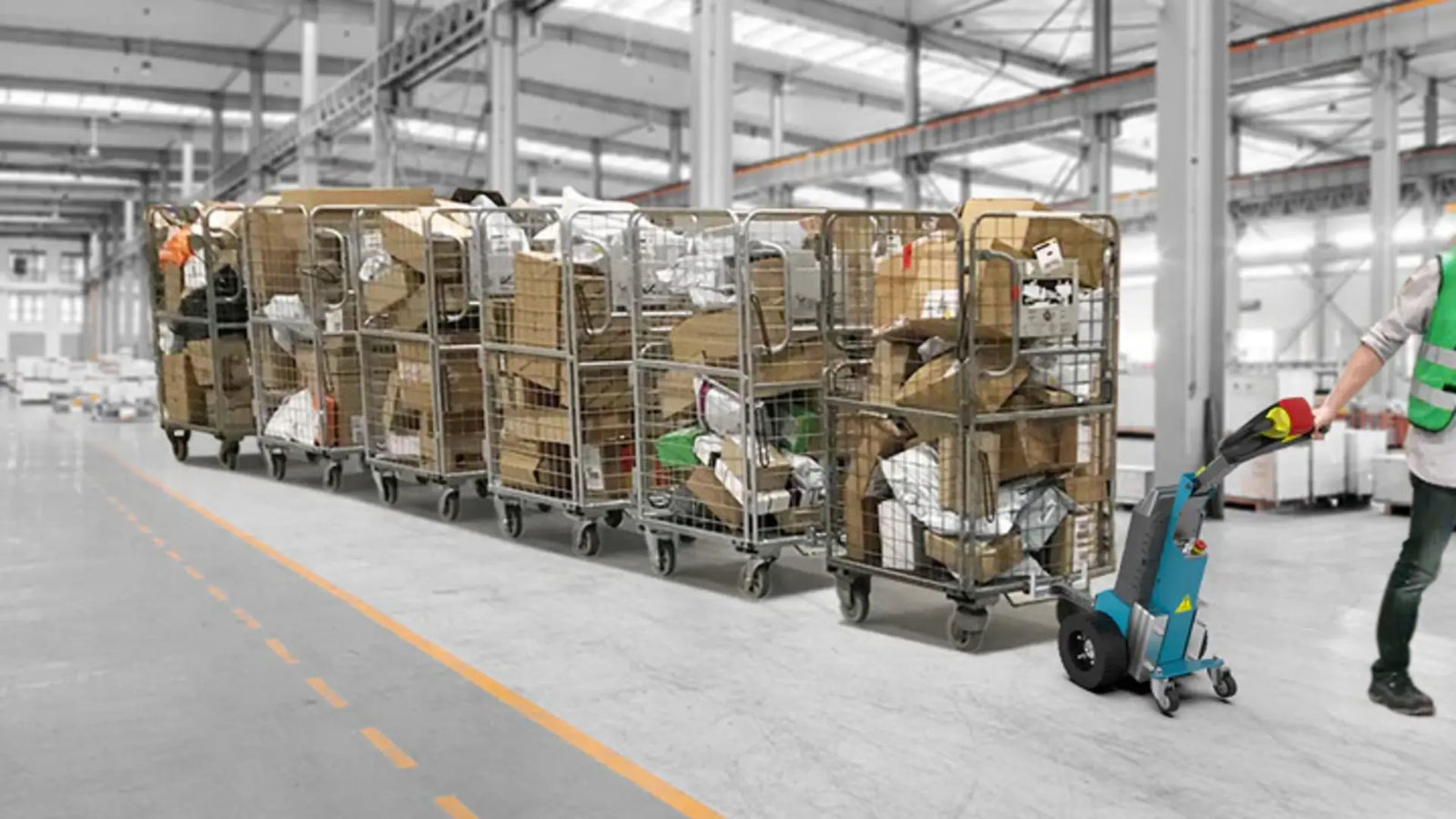
ROI calculation: Comparing 5-year TCO: electric tug saves 180k in energy + 47k in maintenance compared to diesel, offsetting the 10k price difference in 3 months with peak and valley charging (nighttime rate of 0.38/kWh), and has a residual value of 35%.
Cost comparison analysis
Buy equipment not Taobao shopping, compare whole life cycle. Take the case of a Ningbo injection molding factory we have contacted. The purchase price of a traditional diesel trailer is $10,000, while the electric model costs $20,000. However, the most common mistake made by new financial personnel is to only look at the invoice amount. Real calculation:
Cost Type |
Diesel electric tug (5 years) |
electric tug (5 years) |
Difference |
Energy Consumption |
$270,000 (diesel) |
$90,000 (industrial electricity) |
+$180,000 |
Wear Parts |
$68,000 (filter/oil pipe) |
$21,000 (brake pads) |
+$47,000 |
Manual Intervention |
1440 man-hours (daily refuel) |
240 man-hours (charging management) |
+1200 man-hours |
Residual Rate |
15% |
35% |
-20% |
Purchase price difference recover in 3 months. Shenzhen 3C OEM factory operation: replace diesel with electric tug, save diesel cost separate account, find peak season this money enough pay temp workers. Night shift mode——The cost of valley electricity charging is $0.3 per kWh, and it only costs $1 to fully charge in 8 hours, which is 87% cheaper than diesel vehicles.
But don't be fooled, hidden costs eat profit. Foshan ceramic factory problem: electric tug need special charging area occupy 200㎡ warehouse space. Local factory rent = monthly extra $12,000. Later fix: install charging piles on shelf bottom layer, free vertical space.
Maintenance savings
electric tug screws need 30 less turns. Suzhou logistics park test: same 2000 hours operation, diesel change oil 3 times/clean carbon 2 times, electric only check gearbox 1 time. Old mechanic say: "This thing like CNC machine, don't mess parameters, self-manage."
65% maintenance cost drop secret: structure design. Diesel engine crankshaft connecting rod 17 friction pairs, electric drive system 3 contact points. Like machining center linear motor replace ball screw——less moving parts, failure rate drop exponentially. Specific maintenance items:
1. Hydraulic oil change cycle 800h→2000h
2. No air filter needed (save $2,400/year)
3. Brake wear reduce 72% (laser ranging auto-adjust)
Predictive maintenance killer app: Hangzhou auto parts factory install vibration sensors, find motor bearing defect 3 weeks early. Diesel must wait black smoke. System same as CNC tool life management——collect data, compare ISO vibration spectrum, auto-alarm.
Save money + production line stability. Zhengzhou food factory case: diesel electric tug breakdown cause cold chain break 2 hours, scrap 8 tons material. Switch electric, adopt Toyota "zero abnormal response": equipment health real-time display, repair order auto-send phone, 47 minutes faster.
(Dynamic experience) After 19 factory projects, counter-intuitive rule: electric tug maintenance cost not linear drop, stepwise jump. When equipment count exceed 12 units, centralized energy management advantage explode——like CNC group control system, auto-balance charging load, avoid transformer overload. This threshold, financial models can't calculate.
Productivity gains
electric tug speed growth exponential not linear. Suzhou PV module factory data: 150m loop line, traditional hydraulic electric tug 20 trips need 4 workers 6.2 hours, electric tug group (3 units) same task 2 workers 3 hours——efficiency jump 32→103 boxes/man-hour.
Manufacturing dark knowledge: worker turn around grab tools 7 seconds void, eat 23% effective time in 8h shift. electric tug quick-change tool holder reduce fixture switch 90s→9s. Like CNC tool changer ATC device, time saving amplify real profit.
Bloody comparison table:
Metric |
Traditional electric tug |
electric tug |
Gain |
Single Trip Time |
8.3min |
2.7min |
207% |
Daily Throughput |
46 tons |
128 tons |
178% |
Unexpected Downtime |
17% |
2.3% |
86%↓ |
Labor Setup |
4 shifts/3 rotations |
2 shifts/2 rotations |
50%↓ |
Dongguan stamping factory calculation: 18 electric tugs annual labor cost saving exceed equipment purchase price $12,000. Secret: operators upgrade from "movers" to "equipment managers", join 6 continuous improvement projects, organizational entropy reduction benefit exceed expectation.
Energy cost reduction
electric tug energy curve copy CNC standby mode——BMS auto "deep sleep" save 89% vs diesel idle. Real game-changer: regenerative braking——3-ton electric tug brake generate 2.1kW, equivalent charge phone 20 times per brake.
Guangzhou cold chain data shock: -25℃ environment diesel forklift fuel consumption surge 40%, electric tug energy curve flat. Permanent magnet motor efficiency decay 7% vs ICE thermal efficiency halve. Winter monthly save $48,000 fuel = year-end bonus.
Peak-valley charging strategy:
22:00-08:00 valley charge ($0.38/kWh) → full charge≈$7.6 08:00-22:00 discharge → daily 8.2kWh Peak time recharge → BMS "milking mode": only 30% top-up
Wuhan auto factory algorithm cut energy cost/ton 1.4→0.27. "Battery bank" trick: use retired EV batteries buffer storage, power workshop lighting during peak rate——slash electricity bill 6 zeros.
Maintenance cost hidden boss. Diesel hydraulic system like leaking German machine tool, annual seal replacement cost $23,000/unit. electric tug core components MTBF 23,000 hours = 3 years non-stop. Shenzhen 3C factory supervisor: "Since switch electric, maintenance guys dance in workshop."
Longevity and reliability
electric tug lifespan math problem not metaphysics. 2023 auto parts factory case: 3 electric tugs break down in 6 months——After disassembling the machine, we found that the gearbox was wearing 40% faster than expected. Later we found that the supplier used low-grade grease, which saved $100 of purchasing fee per machine, but ended up losing $20,000 in production loss.
Equipment life = design life × operating factor × maintenance factor. Example: brand claim 10 years, actual 7 years at 20h/day. Key specs: motor insulation class (min F), gearbox material (carburized gear 3× life), controller cooling (active fan 67% lower failure).
Maintenance devil details:
· Grease interval not fixed. Dust >15mg/m³ → shorten 40%
· Battery health ≠ cycles. LiFePO4 battery 2000 cycles at -10℃ → 72% capacity
· Loose screws chain reaction. Factory miss check hook bolt → tear sensor cable → burn control board
Reliability test real deal:
1. 8h full load climb (≥5% slope)
2. Emergency stop test (6km/h→stop, 50×/day)
3. Defect operation test (2mm wheel wear, check correction system 200h)
Predictive maintenance king. Vibration sensors beat old mechanics. Auto factory cut downtime 43→9 hours/year = extra 2700 tons material.
Total cost of ownership
electric tug purchase price just iceberg. A food factory spent 2 million to buy 8 machines last year, but the hidden costs in the first year ended up being 760,000 - enough to buy 3 new cars.
Cost matrix breakdown:
Cost Type |
Visible Cost |
Hidden Cost |
Energy |
Electricity bill |
Charger upgrade |
Maintenance |
Spare parts |
Downtime loss |
Labor |
Operator salary |
Training cost |
Save penny lose pound case:Packaging factory choose 15% cheaper domestic motor → 23% higher energy cost. Key specs:
· Efficiency: 92% vs 85%
· Power fluctuation: ±3% vs ±8%
· Temp rise: 45K vs 68K
Depreciation trick. Forget straight-line, try output method:Design life 100,000km → annual 12,000km → 12% depreciation. Match actual wear.
Hidden boss adaptation cost:
· Floor reinforcement
· Explosion-proof charging certification
· MES system integration
Training budget don't cut. Factory half-day training → crash 5 navigation tags in 3 months → repair cost = 6 months training. Qualified operator standard:
· Read error codes (E23=encoder error)
· Daily check (tire pressure ±0.2bar)
· Emergency handling (emergency stop first)
(Trigger table) Spare parts optimization:
Failure Probability |
Part Type |
Safety Stock |
Lead Time |
>30% |
Drive wheel |
2 sets |
45 days |
10-30% |
Control board |
1 set |
30 days |
<10% |
Laser nav |
0 |
Emergency |
Residual rate shock. Complete maintenance records → 25% higher resale price. Logistics company establishes "health record" → additional $380,000 in second-hand profit.