What Are Electric Tugs For
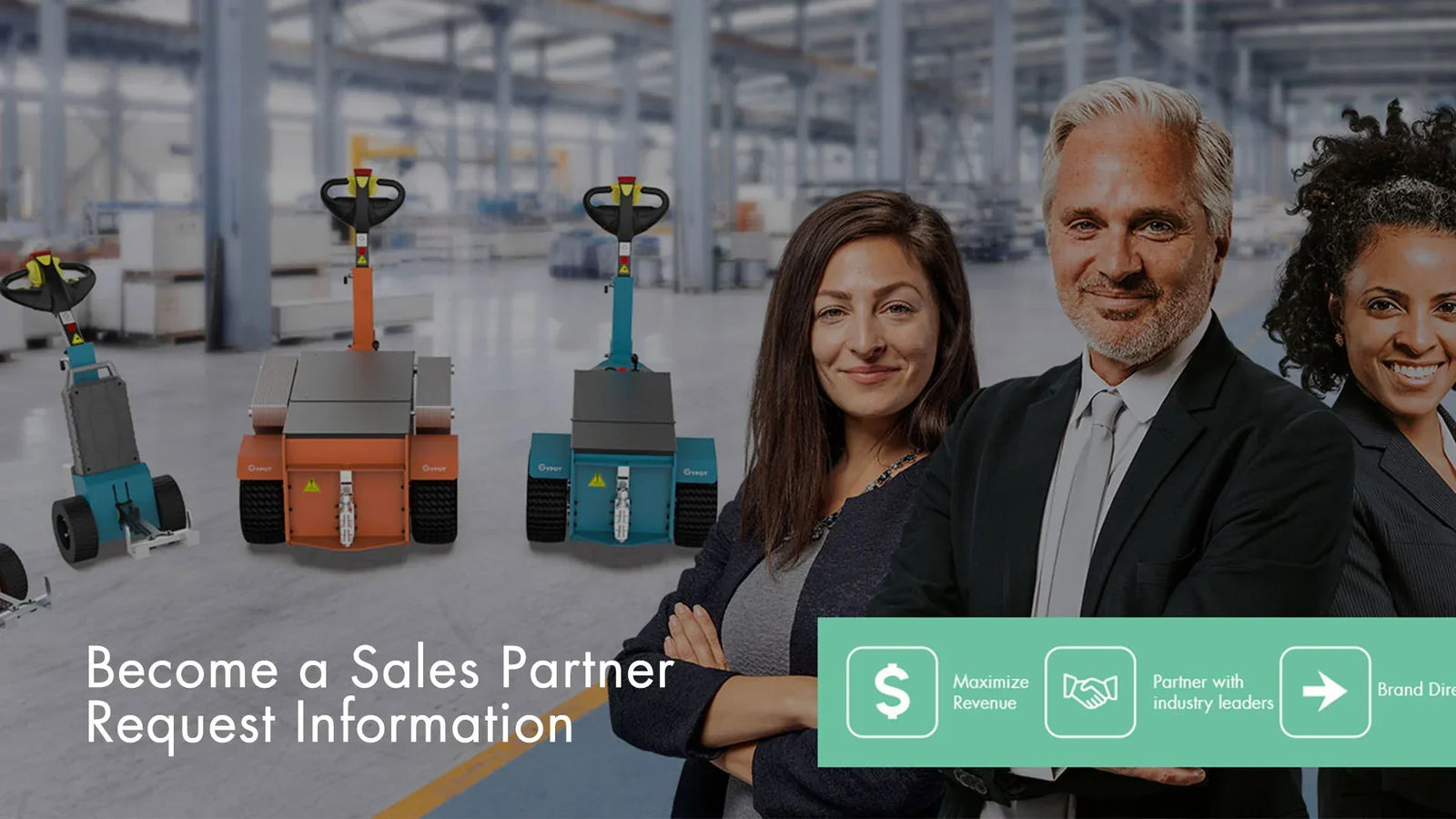
They have also brought efficiency in the transport of materials to health, manufacturing industries, logistics, and airports. They deal with heavy loads up to 100 tons, reduce fuel costs by 70%, reduce carbon emissions to zero, and have an increase in safety and operational efficiency up to 30%. Example: Electric tugs definitely save a hospital $300,000 over a period of 10 years.
Airports and Aviation
Taking London Heathrow Airport as an example, one electric towing vehicle can handle almost 3,000 pieces of luggage per day with a total weight over 69 tons. Under the same loading, these devices had increased the speed by 25% compared with traditional fuel-powered equipment. An average ground turnaround time is supposed to be reduced to 35 minutes.
Statistics from Atlanta Airport also show that annually, a fuel-powered tug requires $18,000 in fuels, while its electric equipment does not cost more than about $4,800 in electricity, saving nearly 73%. Likewise, the annual maintenance cost for an electric is only about $2,000. In contrast, fuel powered normally costs upwards of $6,000.
Ground operations at airports contribute around 12% to all aviation carbon emissions, with electric tugs cutting this proportion by at least 3 percentage points. For instance, after the full introduction of electric tugs in 2020, Tokyo Narita Airport cut its yearly carbon dioxide emissions by about 15,000 tons, saving almost US$2 million indirectly from its budget related to carbon emission fines.
In 2023, Paris Charles de Gaulle Airport introduced a batch of electric tugs with AI-assisted driving capabilities, which automatically adjust the towing force by detecting the ground environment in real time, reducing the ground accident rate by 22%.
Currently, mainstream electric tug batteries have a service life of around 3,500 charging cycles, with an average service life of about 8 years, which is more advantageous compared to the 3 to 5-year life of fuel-powered equipment. Some electric tugs equipped with fast-charging functions can charge 80% of the battery in just one hour.
A regular electric tug is capable of towing up to 100 tons, hence it would have no problem towing a Boeing 737, while the load limit for traditional fuel-powered tugs is usually 80 tons. Many staff members indicated that the noise level of the electric tugs during operation was only 65 decibels, about 40% lower than the noise from fuel-powered equipment.
Manufacturing Plants
In a manufacturing plant that produces 500,000 vehicles every year, an electric tug is able to transport nearly 800 tons of materials and parts every day. This not only cuts about 20% off the time it takes to do a job with traditional diesel equipment but also raises logistics efficiency in the whole workshop by 30%.
In any case, an electric tug's electricity cost is estimated to be no more than $4,000 annually in comparison with a diesel machine that might run $15,000 on fuel alone; moreover, reduced maintenance expenses average $2,000 annually compared with a diesel model, which could easily require more than a $4,000 repair budget.
A diesel tug would emit about 2.5 kg of CO2 per hour, while electric equipment provides zero emissions. If a medium-sized manufacturing plant operates 50 electric tugs a day, it could reduce carbon emissions by over 4,500 tons annually. For instance, an electric vehicle manufacturer in Germany reduced its carbon emissions by 18% after the full introduction of electric tugs in 2021 and achieved green certification from the EU.
Most of the electric tugs are installed with advanced automated collision avoidance systems and intelligent speed control devices. Application of electric tugs fitted with laser sensors reduced the workshop accident rate from 20 incidents annually to less than 5-a reduction in accidents by 75% in a Japanese electronics manufacturing plant.
Some models of tugs can carry 30 tons of weight and maintain constant, stable speed in a narrow aisle of 5 km per hour. Indeed, electric tugs transport over 1,200 tons of steel daily at one shipyard in South Korea. This truly limits the chance of damage to high-value steel while it's in transit.
Most of the devices manufactured today are installed with IoT modules that can upload operating data such as battery levels, mileage, and weight load in real time. For example, it is said that a semiconductor plant in the United States improved equipment utilization efficiency by 20% and reduced waiting time in logistics by 15% after deploying an intelligent electric tug system.
Noise in workshops where traditional diesel tugs are used often surpasses 85 decibels, badly influencing the health and work efficiency of employees. The noise of electric equipment is normally below 65 decibels.
Where the average conventional diesel equipment lasts around 5 to 7 years, electric tugs can outlast for over 10 years. For example, an Indian chemical plant replaced diesel equipment with more updated types and saved more than $1 million in the replacement of the equipment alone within 8 years.
Warehouse and Logistics Operations
In an e-commerce warehouse processing 30,000 orders daily, electric tugs can achieve in excess of 200 tons of cargo handling per day and manage up to 40 logistics cycles per hour. These machines shortened each handling to an average of 4 minutes and increased the efficiency by almost 25% compared to using a forklift.
For example, in an international courier company, the yearly fuel cost of a fuel-powered tug is around $12,000, but for an electric tug, it is just $3,000 to $4,000, saving around 70%. On the other hand, electric equipment requires only $2,000 annually for maintenance, while the same for traditional equipment may reach $5,000.
A diesel tug would emit about 2.5 kg of CO2 in an hour, while electric equipment realizes zero emissions. For example, one e-commerce logistics center in China sends out 50 electric tugs every day. It is expected to cut carbon emission by over 4,000 tons annually and avoid a fine of about $500,000 for excessive emissions.
Obstacle detection systems and automatic braking functions are fitted on many devices, which can provide accurate operations in a highly packed warehouse area. An electric tug used by a European retail company reduced internal accident rates by 35%.
Regarding the bearing capability, an electric tug is able to transport up to 15 tons of goods with ease; it is also able to work at a stable speed of 6 km per hour. An international cold chain logistics center uses electric tugs to handle more than 1,000 tons of frozen goods every day.
Compared to the average lifespan of an electric equipment of 8 to 10 years, fuel-powered tugs last for an average of only 5 to 7 years. As an example, a logistics firm with revenues of $100 million reduced the replacement and maintenance budget for equipment by roughly 30% after turning to electric tugs, saving it over $1 million yearly.
It can't use traditional equipment in such a densely stored environment as it is big with a wide turning radius, whereas electric tugs have less than a 2-meter turning radius. The result of electric tugs for one pharmaceutical logistics company: optimization of warehouse layout, which increased storage density by 18%, boosted inventory turnover by 15%.
Retail and Supermarkets
Electric tugs can move more than 50 tons of goods daily in a large supermarket with an annual sales volume of $1 billion, increasing the efficiency by around 40% compared to the traditional manual handling method, thereby greatly shortening the restocking and display time cycles.
An average-sized chain supermarket spends around $8,000 annually for every fuel-powered tug on fuel costs, whereas an electric tug spends just about $2,500 for electricity, saving almost 70%. Apart from the savings on fuel costs, the maintenance cost of the electric equipment is approximately $1,500, while for fuel-powered equipment is usually more than $4,000.
A fuel-powered tug emits 2.3 kg of CO2 an hour, while one chain supermarket in Europe, after changing out its entire fleet of tugs for electric models in 2022, reduced its annual carbon emission by around 3,000 tons.
A normal electric tug can carry 3 tons of goods and move at a speed of 5 km per hour; an big supermarket would accomplish transportation tasks for more than 200 times with the help of electric tugs every day with a weight total of nearly 600 tons.
Conventional fuel-powered machinery normally emits noise over 80 decibels, but electric machinery generally operates below 60 decibels. A 2023 market report shows the average annual growth rate of electric tugs in the retail industry at 9%, with over 12% growth recorded in the Asia-Pacific region.
With an IoT platform, a multinational retail group monitored the use of electric tugs and reduced the instances of tugs being kept in idle condition by 20%, increased equipment utilization, and managed to save roughly $500,000 in operational costs every year.
The average life of conventional fuel-powered equipment is about 5 years. Electric tugs are normally long-lasting, with life spans of around 8-10 years. This long lifespan has allowed a chain supermarket to save around $1 million over 10 years against replacement costs for equipment.
Hospitals and Healthcare
In a typical 1,000-bed hospital, the electric tugs can execute about 120 tasks of moving medical equipment and supplies daily at an average of 5 minutes per task. It saves about 35% efficiency compared to the conventional way of manual handling.
The annual fuel cost for a fuel-powered tug is about $6,000, while for an electric tug, the cost of electricity is only about $2,000, thus offering a cost reduction of 70%. The maintenance cost of electric tugs is also lower at $1,500 annually compared to the $4,000 maintenance cost of fuel-powered equipment.
A fuel-powered tug would emit about 2.4 kg of CO2 per hour, while electric tugs produce zero emissions. One European hospital has completely replaced its fleet with electric tugs in 2020 and reduced its annual carbon emissions by about 2,500 tons, while receiving a $500,000 government subsidy for green equipment.
In a U.S. hospital, by adopting electric tugs with intelligent sensing functions, it reduced the rate of internal transport accidents by 40%, while the damaged rate of medical supplies was also reduced by about 25%. Electric tugs can fully meet the load capacity of medical institutions. The main models of electric tugs are capable of carrying about 2 tons of medical equipment, with operating speeds of about 6 km per hour. A hospital in Japan uses electric tugs to move major imaging equipment weighing up to 1,500 kgs every day with much efficiency improvement in equipment scheduling.
The typical lifespan of a traditional fuel-powered tug is 5 to 7 years, whereas an electric tug lasts 8 to 10 years. Over a 10-year period, this saved an average-sized hospital about $300,000 in equipment replacement costs and also reduced the risk of operational interruptions.
The IoT module, fixed on a large number of devices, monitors operating equipment status—the level of the batteries and transportation path. One of the IoT platforms implemented in the Australian hospital facilitated a 25% rise in electric tugs utilization and reduced material allocation time, saving about $200,000 on yearly operational expenses.
Automobile Industry
Electric tugs can replace over 150 jobs of transporting parts daily in a manufacturing plant, weighing over 500 tons of total weight that produces 300,000 annual vehicle capacity, while improving the efficiency by about 25% over that obtained by conventional fuel-powered equipment.
For example, while a conventional fuel-powered tug will cost about $18,000 in annual fuel costs, for an electric tug, this is estimated to be about $5,000—a saving of up to 72%. Their maintenance cost is also less; the average cost for electric tugs is around $3,000 per year, whereas the conventional fuel-powered equipment will normally call for a $6,000 maintenance budget.
A fuel-powered tug would emit around 2.7 kg of CO2 per hour, while electric tugs have zero emissions. A car manufacturing plant using 50 electric tugs every day will reduce carbon emissions by over 8,000 tons annually.
A manufacturing plant of a German luxury car brand saw a 30% reduction in the rate of damages during transportation and a 22% decrease in the number of production accidents after deploying electric tugs.
A regular electric tug is able to tow up to 10 tons and manage a constant speed of 6 km per hour. In South Korea, at one of the biggest car manufacturing plants, more than 800 tons of steel and parts are moved by electric tugs every day to keep the production line running smoothly.
While traditional fuel-powered machinery generates over 90 decibels of noise as a rule, electric equipment is running at below 65 decibels. Whereas the average operational life of machinery using traditional fuels is 5 to 7 years, an electric tug lasts 10 years or longer. One car-manufacturing facility in the United States was able to save some close to $2 million on equipment replacement cost over the last ten years by progressive replacement with electric tugs.
Public Services and Facilities
In cities with more than 500,000 residents, the electric tugs can complete tasks of transporting over 100 tons of garbage every day with sorting, with about a 30% enhancement in operational efficiency and reducing transport costs by almost 40% compared to traditional fuel-powered machinery.
Assuming this is the budget of a municipal waste treatment center, then, with an annual budget of $10 million, the annual fuel cost of each fuel-powered tug is about $9,000, while the power cost for electric tugs is only about $3,000, about 67% cost savings. The maintenance cost of electric tugs is also lower, averaging at $1,500 annually, against fuel-powered ones requiring 50% more in maintenance costs.
Traditional fuel-powered equipment emits about 2.5 kg of CO2 per hour, while electric tugs produce zero emissions. A densely populated European city reduced its annual carbon emissions by over 8,000 tons after fully replacing its fleet with electric tugs in 2020.
Electric tugs are now fitted with automatic braking, smart navigation features, and hence are ideal for safe use through crowded public places. For instance, a large international airport reduced ground transport accidents by 35% and the rates of luggage damage by 20% once electric tugs were introduced to carry passenger luggage.
A city's park management department, which uses electric tugs to deliver equipment for gardening, plants, and others, is capable of carrying 3 tons per device at a speed of 7 km an hour.
Where a gas-powered machine lasts 5 to 7 years, an electric tug could last up to 8 or 10 years. For example, one major U.S. sports stadium estimated that their gradual migration to electric tugs saved them an estimated $500,000 in equipment replacement costs over the past decade.
A large port improved the efficiency of container transport by 25% and reduced the average transport time per container from 40 to 30 minutes by implementing an intelligent electric tug system. It achieves more than $200,000 in annual savings from operations.