tugger Blog

Electric tug brakes require daily three-step tests (empty/half/full load), monthly gap checks with feeler gauges (>0.8mm adjust), and quarterly dynamic tests (1.5-ton load on 3° slope) under ISO 3691-2023 250-hour deep inspections, with hydraulic oil changes every 300-500 hours depending on...
Continue reading
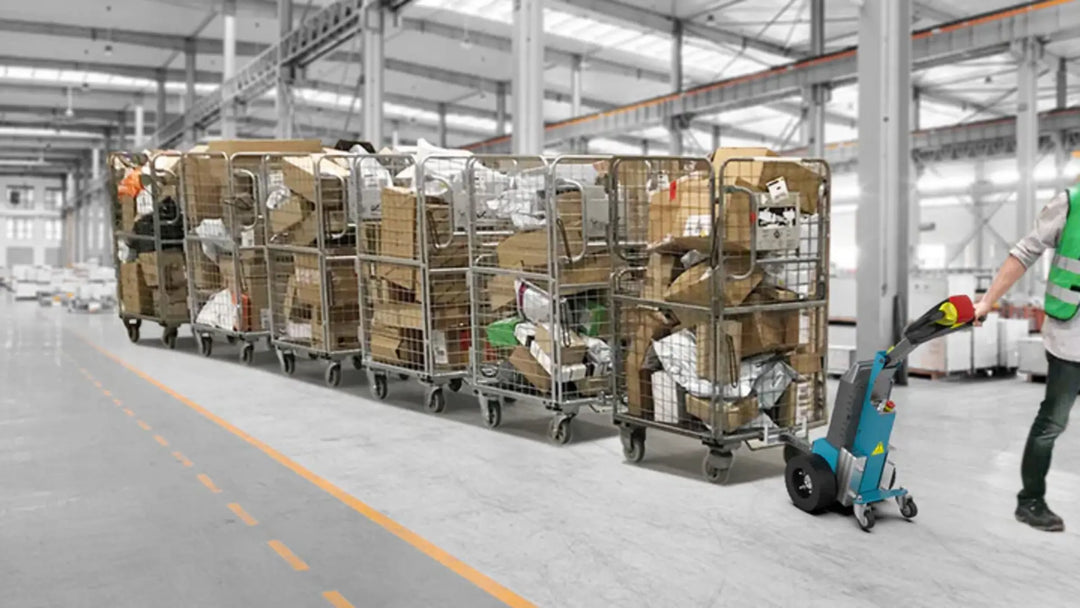
ROI calculation: Comparing 5-year TCO: electric tug saves 180k in energy + 47k in maintenance compared to diesel, offsetting the 10k price difference in 3 months with peak and valley charging (nighttime rate of 0.38/kWh), and has a residual value of 35%....
Continue reading

Integrate electric tugs with conveyors by installing Hilscher NT50 gateways (120Ω terminal resistors), implementing triple safety interlocks (mechanical/photoelectric/PLC), using S-curve acceleration (15% power in 0.5s), and laser scanning for spatial adaptation (±50cm docking zones). Tug-conveyor compatibility 1. Death Red Line of...
Continue reading

German electric tuggers achieve ±0.02mm motion precision through VDI 2854-standard drive systems, maintain 99.3% transmission efficiency after 2000h operation, and feature 15-minute modular controller swaps. Their IP69K-rated components survive 50 thermal shock cycles (-25℃↔60℃) while predictive maintenance algorithms detect bearing failures...
Continue reading
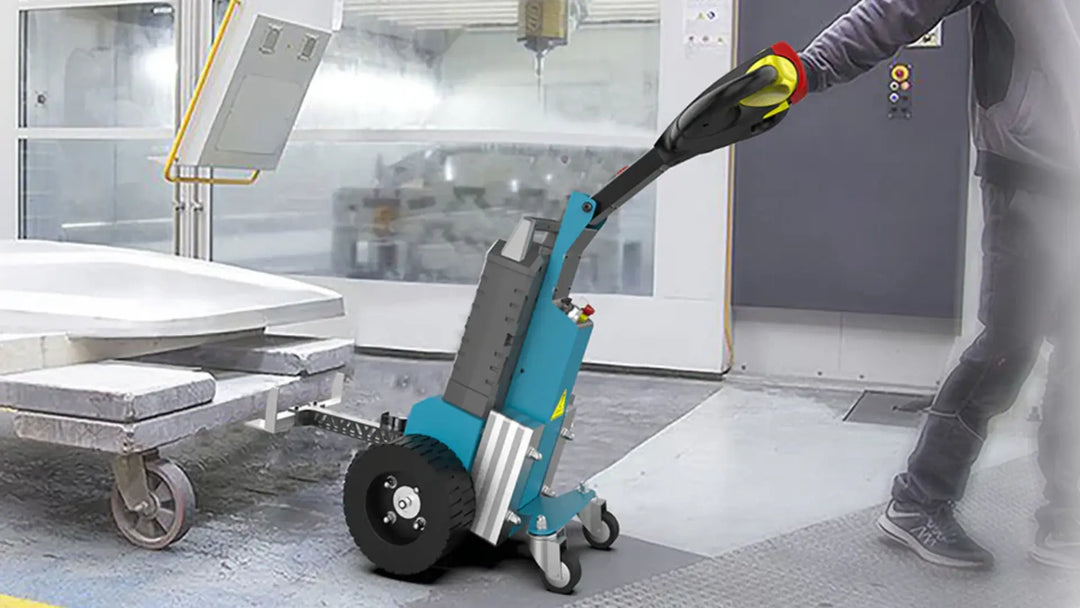
The introduction of the Electric Tug into the workplace has significantly diminished cases of injuries, especially those occurring due to physical strain. It, for example, reduces muscle injury by as much as 64% through automatic load adjustments. Further to this, the ergonomic...
Continue reading