tugger Blog

Electric tugs, for example, optimize the entire pharmaceutical logistics process by decreasing downtimes up to 90%, from 8.5h to 0.9h per month, and energy costs from $430K to $228K annually such that the failure rates decrease further beyond the existing...
Continue reading
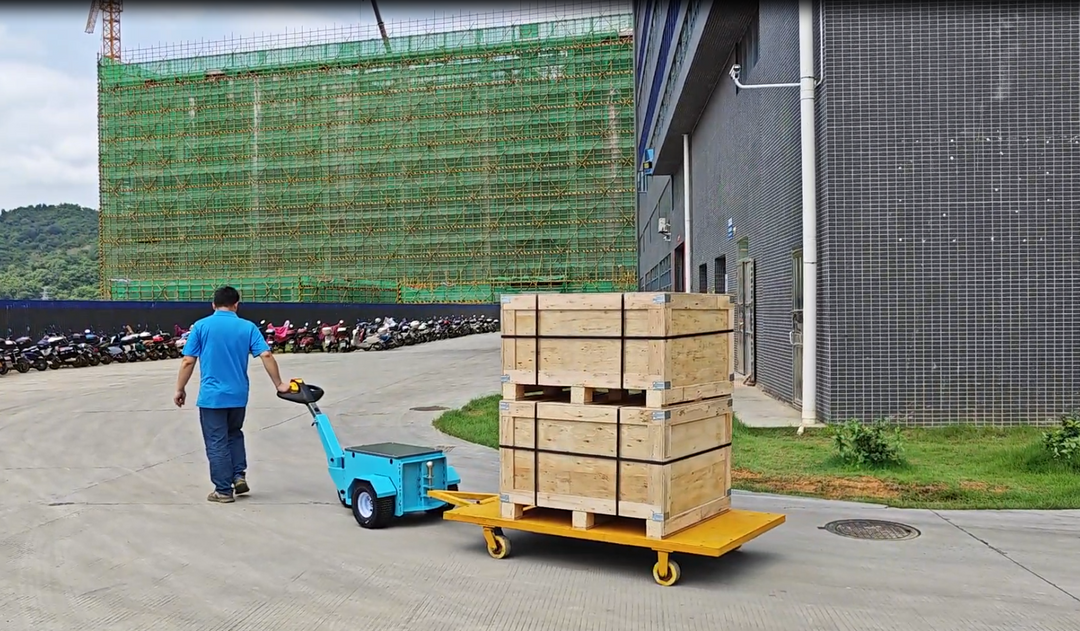
The GYPOT tugger offers 30% faster task completion, 40% higher pressure resistance, and 25% lower energy consumption. With a failure rate under 0.2% and 800-hour maintenance intervals, it enhances productivity by up to 25% and saves $50,000 annually on energy costs....
Continue reading
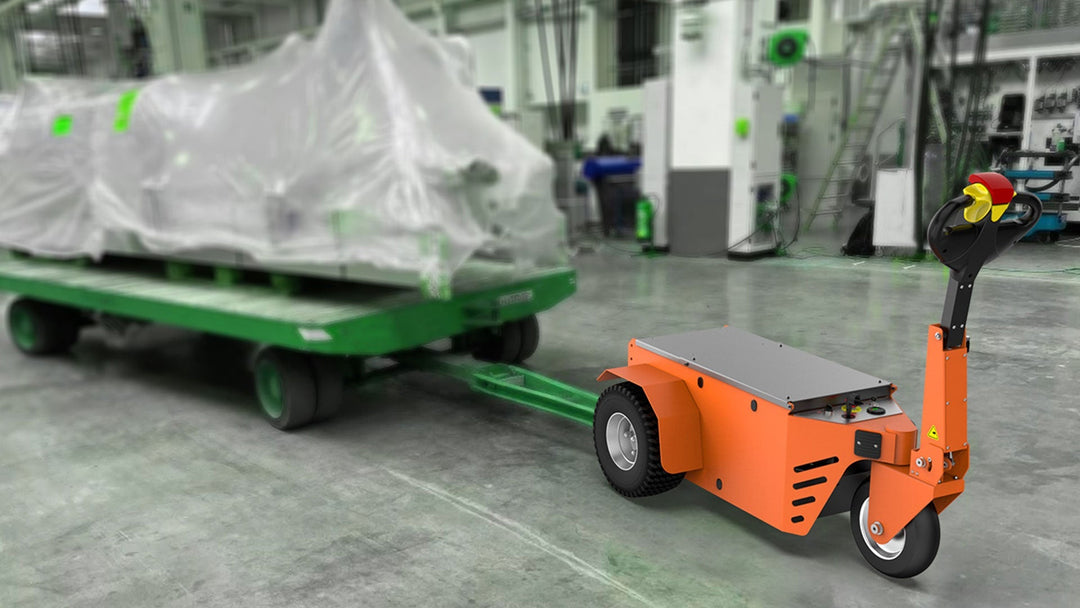
Tugging equipment boosts efficiency by 25%–40%, cuts fuel costs by over 50%, and reduces carbon emissions by 40%. It minimizes downtime by 62%, lowers maintenance costs by 30%, and enhances safety by cutting workplace accidents by 35%, ensuring sustainable and cost-effective operations....
Continue reading
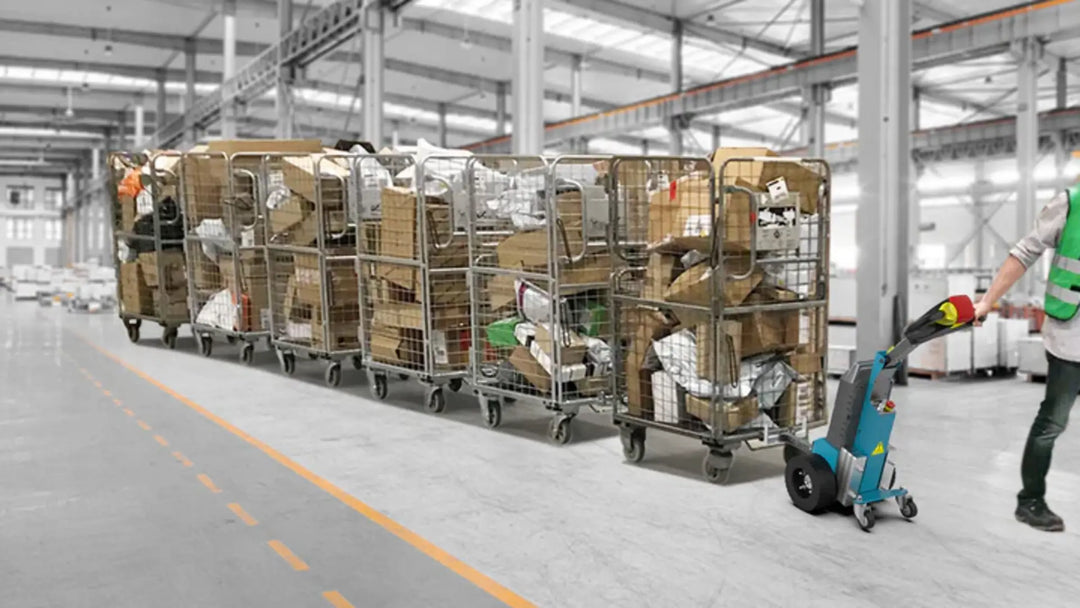
Switching enhances efficiency by 50%, reduces energy costs by 60%-70%, and cuts accident rates by 70%. With intelligent diagnostics, it lowers equipment failure rates by 30% and boosts space utilization by 25%, ensuring safer, faster, and more cost-effective operations. Increases...
Continue reading
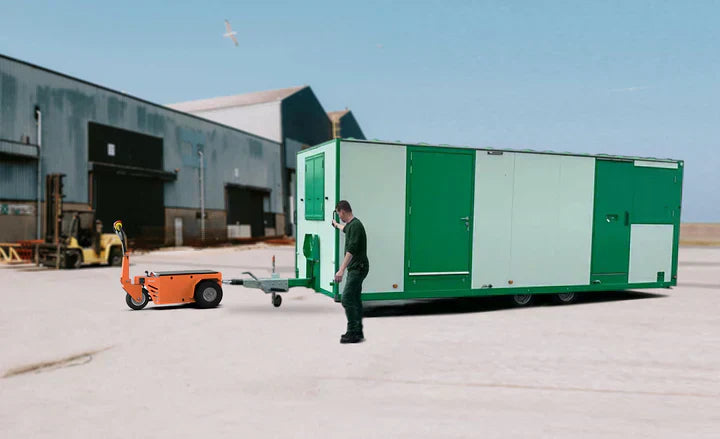
Maintenance for electric tuggers involves annual servicing, checks on batteries every 500 hours, and replacement of the brake pads every 2 years. Regular lubrication reduces energy consumption by 10%, while cleaning cuts failure rates by 25%–30%. Carelessness in that respect...
Continue reading